Safety PLC Interview Questions and Answers
Safety PLC (Programmable Logic Controller) is a specialized form of PLC that is designed to ensure the safe operation of machinery and equipment in the industry. Safety PLC has the ability to monitor and manage various aspects of operational safety, it serves as a crucial component in any safety-critical process. Understanding Safety PLC functions, operation, and programming is essential for any automation or control engineer.
Safety PLC Interview Questions and Answers
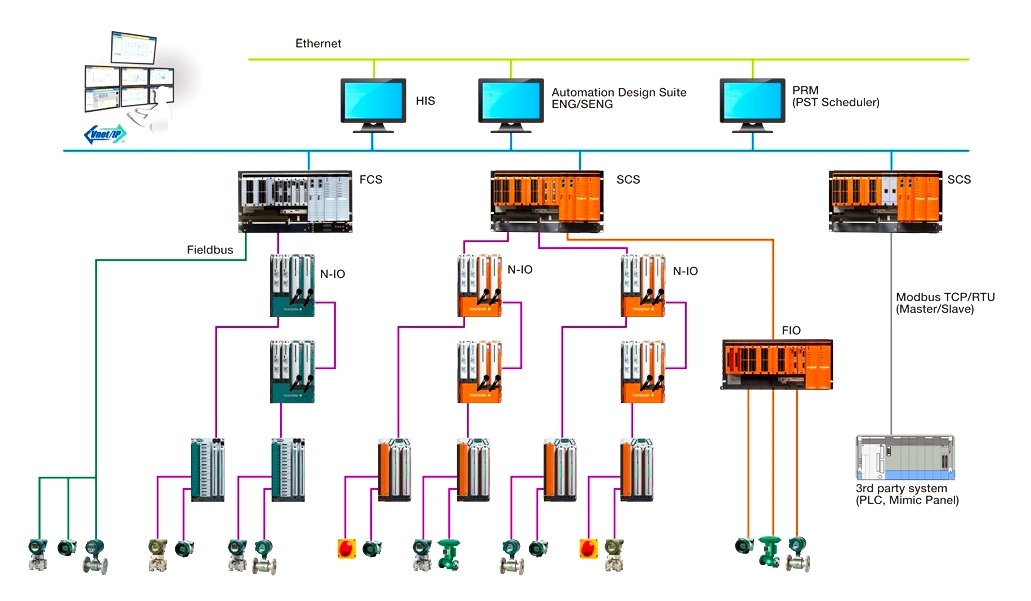
Safety PLC interview questions and answers help you to get insights into key concepts, basics, and functions of Safety PLC in industrial automation. A great resource for anyone preparing for an interview in the field of industrial safety and control systems.
What is a Safety PLC?
A Safety PLC is a specialized type of Programmable Logic Controller designed to ensure safe operation in critical industrial applications. It can process safety-related input signals and activate safety outputs, stopping a process when unsafe conditions are detected.
How does a Safety PLC differ from a standard PLC?
A Safety PLC is specifically designed to meet stringent safety standards. It features hardware and software redundancy, fault detection, and self-diagnosis capabilities that are generally not found in a standard PLC.
What are the common safety standards that Safety PLC complies with?
Safety PLCs generally comply with standards such as IEC 61508 (Functional Safety of Electrical/Electronic/Programmable Electronic Safety-Related Systems) and IEC 61511 (Safety Instrumented Systems for the Process Industry Sector).
Can you explain the concept of a ‘Safety Function’ in a Safety PLC?
A Safety Function in a Safety PLC is a specific function that the PLC performs to ensure the safe operation of a machine or process. This could include emergency stops, pressure or temperature limits, or guard door monitoring.
What does ‘SIL’ mean in the Safety PLC?
‘SIL’ stands for Safety Integrity Level. It’s a measure of safety system performance required for a specific task. SIL levels range from 1 to 4, with SIL 4 being the most reliable.
How does a Safety PLC handle fault detection?
Safety PLCs employ various techniques for fault detection, such as redundant processors, cyclic redundancy checks (CRC) for memory, and watchdog timers. Any detected fault leads to a safe state transition.
What is a ‘Safe State’ in a Safety PLC system?
A ‘Safe State’ in a Safety PLC system is a state where the risk of injury or damage is minimized. If a fault or unsafe condition is detected, the Safety PLC will bring the system to this safe state.
Can you describe the role of Safety Inputs and Safety Outputs in a Safety PLC?
Safety Inputs are signals from safety devices like light curtains or emergency stop buttons. Safety Outputs control elements of the machine or process that can bring it to a safe state, like turning off motors or closing valves.
How does a Safety PLC communicate with other systems?
Safety PLCs can communicate with other systems via standard communication protocols like Ethernet/IP or ProfiNet but with added safety features. They can also use safety-specific protocols like CIP Safety or ProfiSafe.
What is ‘Fail-Safe Programming’ in a Safety PLC?
‘Fail-Safe Programming’ is designing a Safety PLC program in a way that any failure leads to a safe state. This includes proper handling of errors and ensuring that no single fault can lead to an unsafe condition.
What is a safety signature in a Safety PLC?
A safety signature is a unique code that a Safety PLC assigns to its safety data to ensure its integrity. The receiving device verifies this signature before processing the data to prevent any manipulation or error.
What is a safety-rated motion control in a Safety PLC?
Safety-rated motion control in a Safety PLC is the capability to control motion-related operations like speed, direction, and position of a machine part in a safe manner. This involves functions like Safe Stop, Safe Limited Speed, or Safe Direction.
Can you explain the concept of ‘Fail-Safe Over EtherNet/IP’?
‘Fail-Safe Over EtherNet/IP’ is a safety communication protocol for Ethernet/IP networks. It allows for the transmission of safety-related data over the same network as standard data, ensuring safety without needing a separate safety network.
How does a Safety PLC contribute to machine availability?
By detecting faults and transitioning the system to a safe state, a Safety PLC can prevent accidents that could cause serious damage and lengthy downtime. Moreover, by isolating faults, it allows unaffected parts of a system to continue operation.
Can a Safety PLC be programmed in the same way as a standard PLC?
While the basics of programming are similar, programming a Safety PLC involves additional considerations. It’s crucial to ensure that the program brings the system to a safe state in any failure scenario and complies with relevant safety standards.
What is a Safety Fieldbus?
A Safety Fieldbus is a communication system that connects safety devices with a Safety PLC. It can transmit safety-related data with the necessary level of integrity and reliability, such as ProfiSafe for ProfiNet/Profibus networks.
How does a Safety PLC interact with a Human Machine Interface (HMI)?
A Safety PLC can communicate with an HMI to provide operators with real-time safety information. This can include the status of safety inputs/outputs, fault diagnostics, or instructions for recovery from a safe state.
What role does a Safety PLC play in risk assessment?
The capabilities of a Safety PLC, such as SIL level or safety functions, are key factors in risk assessment. By implementing a Safety PLC, the risk associated with various hazards can be reduced to an acceptable level.
How can one test a Safety PLC?
Testing a Safety PLC involves checking its functionality under normal conditions as well as simulating faults to verify the correct response. This should include testing of all safety functions, communication with safety devices, and fault diagnostics.
What is a safety lifecycle in the context of a Safety PLC?
The safety lifecycle is a systematic process covering all stages of a safety system, from initial concept and risk assessment, through design and implementation, to operation and maintenance. A Safety PLC plays a key role in many stages of this lifecycle.
What is the role of safety-certified software in a Safety PLC?
Safety-certified software in a Safety PLC is designed to execute safety functions reliably and respond appropriately to any faults. This software must comply with safety standards, and its development process usually involves rigorous testing and documentation.
How does a Safety PLC handle communication errors?
A Safety PLC uses error detection techniques, such as checksums or CRCs, to detect communication errors. If an error is detected, the Safety PLC may retry communication, report the error, or transition the system to a safe state, depending on the severity of the error.
How does a Safety PLC manage the synchronization of safety devices?
A Safety PLC can manage the synchronization of safety devices through its programming and communication capabilities. For example, it can ensure that a safety gate is closed before allowing a machine to start.
What is a safety relay and how does it compare to a Safety PLC?
A safety relay is a device used to control safety circuits, often used for simple safety functions. A Safety PLC, on the other hand, is more flexible and programmable, capable of handling complex safety functions and integrating safety communication.
How can one increase the Safety Integrity Level (SIL) of a system using a Safety PLC?
Increasing the Safety Integrity Level (SIL) of a system with a Safety PLC involves enhancing system design and safety functions, improving fault detection and diagnostics, implementing redundant safety measures, and following rigorous testing and validation processes.
Can a Safety PLC integrate with non-safety devices or systems?
Yes, a Safety PLC can integrate with non-safety devices or systems for control purposes, but it’s essential to ensure that any faults in these devices or systems do not impact the safety functions of the Safety PLC.
How does a Safety PLC use a watchdog timer?
A Safety PLC uses a watchdog timer to monitor the execution of its program. If the program takes longer than expected, the watchdog timer expires, indicating a potential problem, and the Safety PLC can transition the system to a safe state.
What is the difference between fail-safe and fail-secure in Safety PLC?
In the context of a Safety PLC, fail-safe refers to a system transitioning to a safe state upon a failure, while fail-secure refers to maintaining the current state upon a failure to prevent unauthorized actions.
Can you explain the role of safety networks in a Safety PLC system?
Safety networks in a Safety PLC system provide reliable and secure communication between safety devices and the Safety PLC. They enable the transmission of safety-related data with the necessary integrity and availability.
What is a safety-rated encoder and how does it work with a Safety PLC?
A safety-rated encoder is a device that provides a Safety PLC with reliable and accurate positional data for safety functions. It can be used for functions such as safe speed monitoring or safe direction control.
What is two-hand control and how is it implemented in a Safety PLC?
Two-hand control is a safety measure where an operator must use both hands to operate a machine, preventing them from reaching into a dangerous area. This can be implemented in a Safety PLC by requiring simultaneous activation of two separate input devices.
What does it mean to have dual channel architecture in a Safety PLC?
Dual channel architecture in a Safety PLC means that it has two independent processing channels for safety functions. Both channels must agree on the output state. This redundancy improves fault tolerance and helps ensure that the system responds safely to a failure.
What are some considerations when integrating a Safety PLC with a robotic system?
Integrating a Safety PLC with a robotic system requires considering factors such as safe speed limits, emergency stop functions, safe zone monitoring, and synchronization with other devices. The Safety PLC should be able to control these safety functions reliably.
How does a Safety PLC contribute to worker safety in industrial environments?
A Safety PLC contributes to worker safety by monitoring and controlling various safety functions in an industrial process. This can prevent accidents caused by equipment malfunctions or unsafe conditions, such as overheating, overpressure, or unauthorized access to dangerous areas.
What role does a Safety PLC play in an integrated safety system?
In an integrated safety system, a Safety PLC serves as the central control unit. It collects safety-related data from various sensors and devices, makes decisions based on this data, and controls safety outputs to mitigate risks.
How does a Safety PLC interact with safety-rated sensors?
A Safety PLC receives signals from safety-rated sensors, which monitor various aspects of a machine or process. The Safety PLC processes these signals to determine whether the system is operating safely and takes action if any unsafe conditions are detected.
What kind of diagnostic capabilities does a Safety PLC typically have?
A Safety PLC typically has diagnostic capabilities that allow it to detect and report faults in the system. This can include checking for wiring errors, monitoring the health of safety devices, detecting processor faults, and checking the integrity of communication.
What is the basic principle of operation of a Safety PLC?
A Safety PLC operates based on the principle of reading inputs, executing a program based on these inputs, and then updating outputs. For a Safety PLC, this includes safety-related inputs and outputs and executing safety functions.
Can you explain the principle of redundancy as it applies to Safety PLC?
Redundancy in Safety PLCs refers to having multiple, independent components performing the same function. This ensures that if one component fails, the others can take over, thereby maintaining the safe operation of the system.
How does IEC 61508 relate to Safety PLCs?
IEC 61508 is an international standard for the functional safety of electrical/electronic/programmable electronic safety-related systems. It provides guidelines for the design and development of Safety PLCs, including requirements for hardware and software safety integrity.
What is the basic architecture of a Safety PLC?
The basic architecture of a Safety PLC includes a processor for executing safety programs, safety-rated I/O modules for interfacing with safety devices, communication interfaces for safety networks, and often redundant components for increased reliability.
How does ISO 13849-1 apply to Safety PLC?
ISO 13849-1 is a standard that provides safety requirements and guidance on the principles for the design and integration of safety-related parts of control systems, including the design of software. For programmable electronic systems like Safety PLCs, it’s usually used in combination with IEC 61508.
What is a ‘Safety Circuit’ and how does a Safety PLC manage such circuits?
A ‘Safety Circuit’ is a circuit that performs a safety function. A Safety PLC manages such circuits by monitoring their state through safety inputs and controlling them through safety outputs. The Safety PLC ensures that the safety circuits function correctly to maintain a safe environment.
What is ‘Risk Reduction’ in the Safety PLC?
‘Risk Reduction’ in the context of a Safety PLC refers to the reduction of risks associated with a machine or process. This can be achieved by implementing safety functions in the Safety PLC, such as emergency stop, safe speed monitor, or safety door monitor.
What are the basic steps in programming a Safety PLC?
Programming a Safety PLC involves defining safety functions, creating a logic program that implements these functions, configuring safety I/O, setting up communication with safety devices, and testing the program to ensure correct operation.
Can you explain the principle of ‘Fault Exclusion’ as it applies to Safety PLC?
‘Fault Exclusion’ in Safety PLCs refers to the concept that certain types of faults are so unlikely that they can be excluded from consideration in the safety design. This is based on the quality of the components, the environment, and the expected lifetime of the system.
Can you explain the concept of ‘Safe Failure Fraction’ (SFF) in relation to Safety PLC?
‘Safe Failure Fraction‘ (SFF) in relation to Safety PLCs refers to the ratio of the rate of safe failures and detected dangerous failures to the total failure rate. A higher SFF indicates a higher likelihood that a system will fail in a safe manner.
How does a Safety PLC maintain ‘Functional Safety’?
A Safety PLC maintains ‘Functional Safety’ by executing safety functions that bring the system to a safe state in case of specific hazardous events. It does so reliably, taking into account possible failure modes and using mechanisms like redundancy, diagnostics, and fail-safe design.
What is the ‘Proof Test’ in the Safety PLC?
A ‘Proof Test’ in the context of Safety PLCs is a periodic test to reveal undetected failures that could prevent a safety function from performing its intended action. The proof test should be designed based on the system’s failure modes and safety requirements.
How does IEC 62061 relate to Safety PLCs?
IEC 62061 is a standard for the safety of machinery that provides requirements for the design, implementation, and validation of Safety PLCs. It also provides guidelines for determining the required Safety Integrity Level (SIL) for a system.
What does ‘Common Cause Failure’ mean in the Safety PLC?
‘Common Cause Failure’ in the context of Safety PLCs refers to a situation where multiple components fail due to a single event or cause, such as a power surge or environmental conditions. This is a risk, especially in redundant systems, and should be considered in the safety design.
What is the ‘Safety Function’ in a Safety PLC?
A ‘Safety Function’ in a Safety PLC is a function that the PLC performs to ensure safety. This can be a response to a specific event (like an emergency stop) or a constant monitoring function (like checking that a temperature remains within safe limits).
What does ‘Diagnostics Coverage’ mean in the Safety PLC?
‘Diagnostics Coverage’ in the context of Safety PLCs refers to the fraction of all possible failure modes that are detected by the PLC’s diagnostics. A high diagnostics coverage increases the likelihood of detecting and reacting to faults in a safe manner.
What are the considerations when choosing a Safety PLC for a specific application?
Choosing a Safety PLC for a specific application involves considering factors like the required Safety Integrity Level (SIL), the complexity of the safety functions, the number and type of safety devices to be connected, the required communication capabilities, and the environmental conditions.
What could cause a Safety PLC to enter a fault state?
Several things could cause a Safety PLC to enter a fault state, including hardware malfunctions, software errors, communication errors, I/O faults, incorrect wiring, or Undervoltage conditions.
How can you troubleshoot a Safety PLC that is not responding to safety input changes?
Troubleshooting could involve checking the wiring and status of the safety input device, verifying the correct configuration of the safety input in the PLC software, and checking for fault indicators on the Safety PLC or in its diagnostic data.
How would you address an issue where a Safety PLC’s safety output does not activate when expected?
Addressing this issue could involve checking the status and wiring of the safety output device, verifying the correct logic in the Safety PLC program, and checking for fault indicators that could suggest a problem with the output module or the PLC itself.
What are some common problems encountered when integrating a Safety PLC with safety networks?
Common problems can include network configuration errors, communication interference or noise, incompatible network devices, or incorrect network wiring.
How can you resolve communication issues between a Safety PLC and a safety-rated I/O module?
Resolving communication issues could involve checking the network wiring and connections, verifying the correct configuration of the I/O module in the Safety PLC software, and checking the status and diagnostic data of both the I/O module and the Safety PLC.
What should you do if a Safety PLC frequently enters a safe state unexpectedly?
This could indicate that the safety functions are being triggered unnecessarily or that there are false positives. It’s essential to review the safety logic, check the status and operation of safety devices, and look at the PLC’s diagnostic data to understand what’s causing the transitions to a safe state.
How can you troubleshoot a Safety PLC that is not communicating with a safety network?
Troubleshooting can involve checking the network connections and wiring, verifying the network configuration in the Safety PLC software, resetting or power cycling the PLC, and checking for network faults or errors.
What are some issues that could arise when upgrading a Safety PLC system?
Issues could include incompatibility between old and new hardware or software, difficulties in transferring the safety program, disruption of safety functions during the upgrade, or the need for revalidation of the safety system.
How can a software update affect the operation of a Safety PLC?
A software update could introduce new features or changes that affect the operation of the Safety PLC. It could also introduce bugs or compatibility issues. Therefore, it’s essential to test the system thoroughly after an update and to have a rollback plan in case problems arise.
What are some potential challenges when implementing a Safety PLC in an existing machine or process?
Challenges can include adapting the safety functions to the specifics of the machine or process, interfacing with existing non-safety devices, ensuring sufficient diagnostic coverage, achieving the required Safety Integrity Level (SIL), and integrating the Safety PLC with existing control systems.
How would you diagnose a sudden shutdown of a Safety PLC?
Diagnosing a sudden shutdown could involve checking power supply voltage levels, reviewing fault logs if available, inspecting the physical condition of the PLC and its environment (for signs of overheating or damage, for instance), and verifying the state of safety inputs at the time of shutdown.
What steps would you take if a Safety PLC fails to start up after power is applied?
If a Safety PLC fails to start, one could check the power supply, inspect wiring and connections, look for any indication of hardware damage, ensure the correct startup sequence is being followed, and check if any errors or diagnostic messages are being displayed or logged.
If you encounter unexpected results from a safety function in the Safety PLC, how would you troubleshoot it?
Troubleshooting unexpected results might involve verifying the logic of the safety function in the PLC’s program, checking the status and operation of the associated safety devices, testing the function under controlled conditions, and reviewing any diagnostics or logged data related to the function.
What might cause intermittent communication errors between a Safety PLC and safety devices, and how would you diagnose such errors?
Causes could include noisy or unstable network conditions, intermittent faults in the PLC or devices, or configuration errors. Diagnosis might involve checking network diagnostics, testing network stability, verifying device configurations, and inspecting network wiring and connections.
If a safety output device connected to a Safety PLC fails to operate correctly, what are the possible causes, and how would you troubleshoot this issue?
Causes could include a fault in the output device, an error in the PLC’s output module, incorrect wiring, or an issue in the PLC’s program. Troubleshooting might involve testing the output device independently, checking the PLC’s output status and diagnostics, inspecting the wiring, and verifying the relevant output logic in the PLC’s program.
How would you troubleshoot a Safety PLC that’s not responding to changes in a safety network’s devices?
This could be due to communication errors, configuration issues, or program logic errors. You might troubleshoot by verifying the PLC’s network configuration, checking network diagnostics and communication status, and reviewing the program logic related to the network devices.
What could cause a Safety PLC to unexpectedly trigger a safety function, and how would you diagnose this issue?
Causes could include incorrect input readings, errors in the safety function’s logic, or issues with safety devices. Diagnosing this might involve verifying the input status and operation, reviewing the safety function’s logic in the PLC’s program, and checking the PLC’s diagnostics and logged data at the time of the event.
How would you handle a situation where a Safety PLC’s fault indicators are continuously active?
You could first check the PLC’s diagnostic data or fault logs to identify the cause. If these don’t provide a clear answer, further steps might include verifying power supply levels, checking hardware status and connections, and reviewing the PLC’s program and configuration.
How would you diagnose a Safety PLC that is operating slowly or lagging?
Diagnosing this might involve checking the PLC’s CPU usage, verifying the complexity and execution time of the PLC’s program, looking for network communication delays, and checking for any hardware faults or environmental conditions that could affect performance.
If a Safety PLC is not retaining its program or configuration after power cycles, how would you troubleshoot this issue?
This could be due to a faulty or depleted memory backup battery, or issues with the PLC’s memory hardware or software. Troubleshooting might involve checking the battery status, verifying the PLC’s memory configuration, and looking for any related fault indicators or diagnostic messages.
What might cause Safety PLC to enter into a fail-safe mode and how would you troubleshoot it?
Safety PLC might enter fail-safe mode due to a safety input change, software error, a detected fault, or a power issue. Troubleshooting involves checking the status and wiring of safety devices, validating the PLC’s software, investigating the diagnostics logs, and confirming the power supply is stable.
How do you handle an issue where a Safety PLC isn’t responding to changes in the status of a safety device?
First, check the device’s status and wiring, then validate the configuration of the device in the Safety PLC software. If no issues are found, check for fault indicators on the PLC or in its diagnostic logs.
What would you do if the Safety PLC doesn’t allow downloading of a new program?
Check the PLC’s mode switch setting and ensure it’s in programming mode. Make sure the program doesn’t exceed the memory capacity of the PLC. Also, inspect for any security measures in place that prevent unauthorized downloading of programs.
How can you troubleshoot a Safety PLC that frequently resets or reboots?
Frequent resets could be due to power supply issues, CPU faults, or severe software errors. Check the power supply voltage levels and stability, examine the CPU for faults or overheating, and review the PLC’s software and error logs.
What might cause the Safety PLC to not recognize an I/O module and how would you diagnose this issue?
This might be due to incompatible hardware, configuration errors, faulty module, or issues with network communications. Verify the compatibility of the module, check its configuration in the PLC software, inspect the physical condition of the module, and review the PLC’s diagnostic logs.
How do you resolve errors when Safety PLC fails to compile a program?
Check the program for syntax errors, verify the use of correct data types, ensure that all variables are defined, and make sure that the program size does not exceed the memory capacity of the PLC.
If a Safety PLC isn’t communicating with a PC or programming device, how would you troubleshoot?
Check the physical connections and cables, confirm the communication settings match on both devices, ensure the correct drivers are installed on the PC, and check for any fault indicators or diagnostic messages.
How would you diagnose a Safety PLC that is in fault mode but no faults are indicated?
This could be due to a software error, communication issues, or internal hardware faults. Check the PLC’s software for errors, verify network communications, and inspect the internal condition of the PLC for signs of damage or faults.
What might cause safety outputs to activate incorrectly and how would you troubleshoot this?
This could be due to incorrect programming, faulty output devices, or errors in the safety input status. Verify the PLC’s programming logic, test the operation of the output devices, and check the status of safety inputs.
If a Safety PLC fails to meet its specified Safety Integrity Level (SIL), what could be the causes and how would you troubleshoot it?
Causes could include hardware faults, software errors, insufficient diagnostic coverage, or incorrect safety function implementation. Inspect the hardware, validate the software, verify diagnostic coverage, and review the implementation of safety functions.
If you detect a memory error on a Safety PLC, what are the possible causes and how would you address them?
A memory error could be caused by a hardware malfunction, incorrect software operation, or an issue with the PLC’s power supply. You would address this by checking the PLC’s memory modules for faults, verifying the software operation, and confirming the stability of the power supply.
How would you troubleshoot a situation where a Safety PLC cannot establish a connection with a safety network?
You might check the physical network connections and cabling, verify the network settings in the PLC and the network devices, and check for any network-related error messages or diagnostics.
If the I/O response time of a Safety PLC is slower than expected, how would you diagnose this issue?
Check the configuration of the I/O modules in the PLC software, verify the operation of the I/O devices, look for any related error messages or diagnostics, and test the I/O response under different conditions.
How would you address a situation where a Safety PLC is not recognizing a newly installed safety device?
You could verify the compatibility and configuration of the device, check the physical connection and wiring of the device, and look for any related error messages or diagnostics in the PLC.
If a safety function in a Safety PLC does not deactivate when expected, how would you troubleshoot this issue?
Review the logic of the safety function in the PLC’s program, check the status and operation of the associated safety inputs and outputs, and investigate any relevant diagnostic data or error messages.
What could cause a Safety PLC to not retain its safety parameters after a power cycle, and how would you diagnose this?
This could be due to a fault in the PLC’s memory or battery, an error in the PLC’s software, or a problem with the power supply. Check the condition of the PLC’s memory and battery, verify the operation of the PLC’s software, and confirm the stability of the power supply.
How can you troubleshoot a situation where a Safety PLC is not achieving the expected redundancy level?
Check the configuration of the redundancy system in the PLC software, verify the status and operation of the redundant modules, and look for any related error messages or diagnostics.
What might cause a Safety PLC to exceed its maximum CPU usage, and how would you diagnose this issue?
Excessive CPU usage could be caused by complex or inefficient programming, high network traffic, or hardware faults. Diagnose this issue by reviewing the complexity and efficiency of the PLC’s program, monitoring the network traffic, and checking for any hardware faults or error messages.
If a Safety PLC is generating excessive heat, what are the possible causes and how would you address them?
Excessive heat could be caused by an overloaded CPU, a malfunctioning cooling system, or poor environmental conditions. Address this issue by verifying the CPU usage, checking the operation of the cooling system, and reviewing the ambient temperature and ventilation in the PLC’s location.
How would you troubleshoot a Safety PLC that is not passing a safety function test?
Review the expected operation of the safety function and the associated safety devices, verify the correct configuration of the function and devices in the PLC software, and test the safety function under different conditions to identify the cause of the issue.
Read Next: