Instrumentation Insights: Exploring Safety Integrity Level (SIL)
Safety Integrity Level (SIL) is a crucial concept in the field of functional safety that assesses the reliability of safety systems to mitigate risks and prevent hazardous incidents. SIL provides a quantitative measure of the effectiveness of safety functions, ensuring that the required risk reduction targets are achieved. Understanding SIL and its application is essential for engineers and professionals involved in designing and implementing safety-critical systems.
Safety Integrity Level
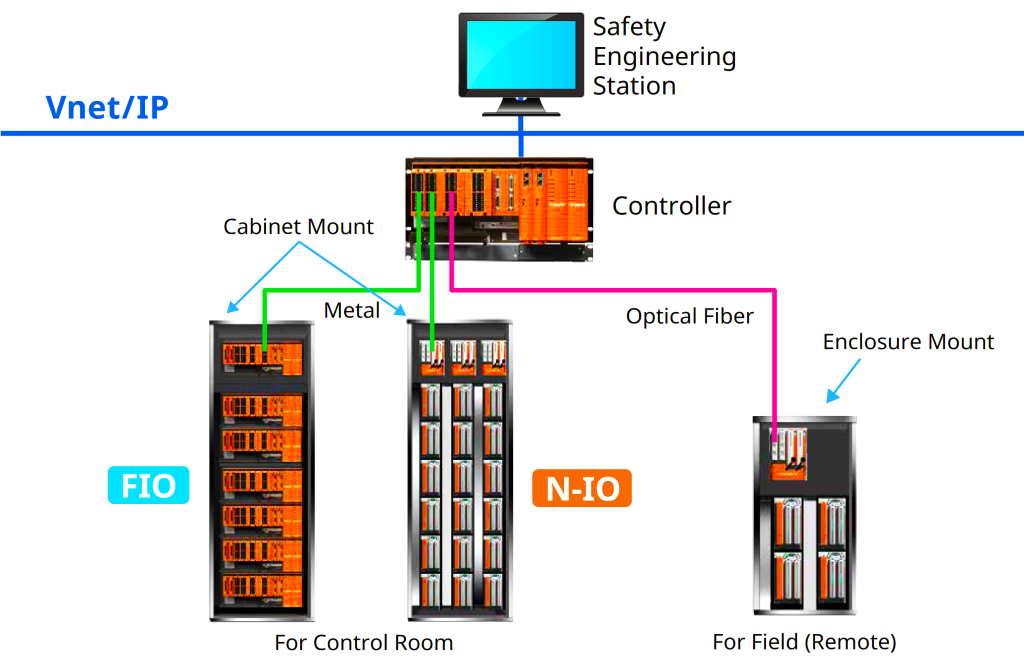
Gain valuable instrumentation insights as we delve into the world of Safety Integrity Level (SIL). Explore the significance of SIL in functional safety, its role in mitigating risks, and its impact on safety-critical systems. A must-read for professionals seeking a comprehensive understanding of SIL and its application in industrial instrumentation.
What is a Safety Integrity Level (SIL)?
A Safety Integrity Level (SIL) is a measure of safety system performance, or reliability, for a Safety Instrumented System (SIS). It is defined as a relative level of risk reduction provided by a safety function.
How many SIL levels are there?
There are four SIL levels, designated SIL 1 to SIL 4. A higher SIL level corresponds to a higher degree of safety or risk reduction.
What factors determine the required SIL for a safety function?
The required SIL for a safety function is determined by several factors, including the severity of a potential accident, the frequency of exposure to the hazard, the probability of avoiding the hazard, and the probability that the safety function will perform correctly.
What is the relationship between SIL and the Probability of Failure on Demand (PFD)?
The SIL is inversely proportional to the Probability of Failure on Demand (PFD). The higher the SIL, the lower the PFD, and thus the greater the reliability of the safety function.
What is the role of ‘SIL Verification’?
SIL Verification is the process of confirming that the proposed or existing Safety Instrumented Function (SIF) is capable of achieving the target SIL. This is typically done through reliability analysis.
What standards govern the application of SIL in the industry?
The application of SIL in industry is governed by various standards, including IEC 61508 and IEC 61511. These standards define the requirements for achieving a particular SIL.
What is ‘SIL Certification’?
SIL Certification is a confirmation provided by a third-party body that a product, system, or service meets the requirements for a specific SIL as defined by the relevant standards.
How does the required SIL influence the design of a Safety Instrumented System (SIS)?
The required SIL influences several aspects of SIS design, including system architecture, component selection, redundancy, testing intervals, and documentation requirements.
Can a system have different SIL requirements for different safety functions?
Yes, a system can have different SIL requirements for different safety functions. Each Safety Instrumented Function (SIF) within a system can have a different target SIL, depending on the risk associated with the particular process condition it is designed to mitigate.
What is ‘SIL Decomposition’?
SIL Decomposition is a method used in system design where a safety requirement with a high SIL is broken down into several requirements with lower SILs. This can allow for more flexibility in system design.
What is the difference between SIL and PL (Performance Level)?
SIL and PL are both measures of safety system performance, but they are used in different contexts. SIL is typically used for process safety applications, as defined by IEC 61508 and IEC 61511 standards. PL, on the other hand, is used for machinery safety applications, as defined by ISO 13849 standards.
What is the ‘risk reduction factor’ in the context of SIL?
The risk reduction factor is a measure of how much the risk is reduced by the implementation of a safety function. It is calculated as the ratio of the risk without the safety function to the risk with the safety function. The risk reduction factor is directly related to the SIL.
Can a device be considered SIL compliant if it is not SIL certified?
A device can potentially meet the requirements of a particular SIL without being formally certified. However, without certification from a reputable third-party body, it may be challenging to demonstrate that the device indeed meets the necessary SIL requirements.
What is the ‘Average Probability of Failure on Demand’ (PFDavg)?
The Average Probability of Failure on Demand (PFDavg) is a measure of the likelihood that a system will not perform its safety function when required. It is a key parameter in determining the SIL of a system.
What is the concept of ‘Safety Availability’ in relation to SIL?
Safety Availability is a measure of the proportion of time that a system is capable of performing its safety function. It is directly related to the SIL – a system with a higher SIL has a higher Safety Availability.
How is ‘Safe Failure Fraction’ related to SIL?
Safe Failure Fraction (SFF) is the proportion of failures that result in a safe state or in an annunciation of the failure. A higher SFF can lead to a higher allowable SIL for a subsystem.
How does redundancy affect the SIL of a system?
Redundancy can enhance the reliability and thus the SIL of a system. If one component fails, the redundant component can take over, reducing the Probability of Failure on Demand (PFD) and thus allowing a higher SIL to be achieved.
What is the significance of ‘Hardware Fault Tolerance’ (HFT) in achieving a particular SIL?
Hardware Fault Tolerance (HFT) is the ability of a system to tolerate hardware faults without losing the ability to perform a safety function. The required HFT depends on the SIL and Safe Failure Fraction (SFF).
What role does ‘Functional Safety Management’ play in achieving and maintaining a desired SIL?
Functional Safety Management is a systematic approach to ensuring that the safety functions of a system consistently achieve the desired SIL. It involves activities such as hazard and risk assessment, design and implementation of safety functions, operation and maintenance, and validation.
What is the relationship between ‘Life Cycle cost’ and SIL?
The Life Cycle cost of a system tends to increase with SIL. Higher SIL systems require more rigorous design, implementation, and maintenance processes, which can lead to higher costs over the life of the system.
How are SIL levels classified?
SIL levels are classified from SIL 1 to SIL 4. SIL 1 represents a lower level of safety required and thus a higher level of risk acceptance, while SIL 4 represents a higher level of safety required and thus a lower level of risk acceptance.
Are there any differences between SIL levels for different industries?
The definition and criteria for SIL levels are generally consistent across industries as they are defined by international standards like IEC 61508 and IEC 61511. However, the way SIL levels are applied and the specific requirements for achieving a particular SIL level can vary based on industry-specific standards and regulations.
What is the difference between Type A and Type B devices in SIL terminology?
Type A devices in SIL terminology are relatively simple in design, predictable in behavior, and usually comprise electromechanical components. Type B devices, on the other hand, are complex, typically incorporating microprocessors, and require more rigorous analysis and testing to ensure they can meet the required SIL.
What is meant by the term ‘SIL-rated’?
‘SIL-rated’ refers to products or systems that have been evaluated and certified to meet the requirements of a specific SIL level. This typically involves testing and assessment by a third-party organization to verify that the product or system meets the safety performance requirements specified by the relevant standards.
What is the difference between ‘SIL Capable’ and ‘SIL Certified’?
‘SIL Capable’ means that a device or system has the features and characteristics necessary to be used in a SIL-rated safety function, but it has not been formally assessed or certified by a third-party organization. ‘SIL Certified’ means that the device or system has undergone formal assessment and has been certified by a third-party organization to meet the requirements of a specific SIL.
How are hardware and software factors considered in determining a SIL?
Both hardware and software factors are crucial in determining a SIL. Hardware considerations include reliability, fault tolerance, and safe failure fraction. Software considerations include system design and development processes, testing and verification, and management of changes and configuration.
What is ‘Prior Use’ or ‘Proven In Use’ in the context of SIL?
‘Prior Use’ or ‘Proven In Use’ is a concept where equipment or a system can be considered suitable for use in a safety function of a specified SIL if it has a well-documented history of performance in similar environments and conditions.
Are there any ‘SIL Zero’ devices?
The term ‘SIL Zero’ is sometimes used informally to refer to a device or system that has not been rated for any Safety Integrity Level. However, this term is not officially recognized in the IEC 61508 or IEC 61511 standards.
Can a system achieve a higher SIL by adding more SIL-rated devices?
Adding more SIL-rated devices in a redundant configuration can potentially enhance the reliability of a system, but it does not automatically ensure a higher SIL. The system as a whole, including all devices and the interactions between them, must meet the requirements for the desired SIL.
What role do ‘Diagnostics’ play in achieving a particular SIL?
Diagnostics are crucial for achieving and maintaining a particular SIL. They enable the early detection of faults which could cause a safety function to fail, thereby improving the reliability and availability of the system. This can lead to
How is the Probability of Failure on Demand (PFD) calculated for a Safety Instrumented Function (SIF)?
PFD can be calculated as the sum of the product of the failure rates of each component in the system and the time of exposure to the failure. It is usually calculated over the proof test interval of the system.
What is the formula for calculating the Risk Reduction Factor (RRF)?
RRF is calculated as the inverse of the Probability of Failure on Demand (PFD). Thus, RRF = 1 / PFD.
How is Safe Failure Fraction (SFF) calculated?
SFF is calculated as the ratio of the rate of safe failures and detectable dangerous failures to the total failure rate. SFF = (λs + λdd) / λTotal, where λs is the rate of safe failures, λdd is the rate of detectable dangerous failures, and λTotal is the total failure rate.
How is Hardware Fault Tolerance (HFT) determined?
HFT is determined based on the architecture of the system. It is equal to the number of redundant channels in the system minus one. For example, a system with two redundant channels has an HFT of 1.
How do you calculate the Average Probability of Failure on Demand (PFDavg)?
PFDavg is calculated using the formula PFDavg = λDU * TI / 2, where λDU is the dangerous undetected failure rate and TI is the proof test interval.
How is the required SIL for a safety function determined?
The required SIL for a safety function is determined based on the target Risk Reduction Factor (RRF). Each SIL corresponds to a range of RRF values: SIL 1 (RRF 10 to 100), SIL 2 (RRF 100 to 1,000), SIL 3 (RRF 1,000 to 10,000), and SIL 4 (RRF 10,000 to 100,000).
Is there a formula for calculating Safety Availability?
Safety Availability can be calculated as 1 – PFDavg. It represents the proportion of time that a system is expected to be capable of performing its safety function.
How is the Spurious Trip Rate (STR) calculated?
The Spurious Trip Rate is calculated as the total rate of all failure modes which can cause a spurious trip, divided by the proof test interval. It is a measure of the system’s robustness against unnecessary shutdowns.
Is there a mathematical relationship between Safety Integrity Level (SIL) and Safety Availability?
Yes, higher SILs correspond to higher Safety Availability. The exact relationship depends on the specific definitions and criteria set by the applicable standards, but in general, a higher SIL represents a lower average probability of failure on demand, which translates to higher Safety Availability.
How does increasing the proof test interval affect the SIL of a system?
Increasing the proof test interval can potentially increase the Probability of Failure on Demand (PFD) and thus decrease the SIL of a system. Regular testing helps detect and correct dangerous undetected failures, which contributes to the reliability and safety of the system.
How does the concept of ‘Common Cause Failure’ (CCF) relate to SIL?
Common Cause Failure (CCF) is when multiple components or subsystems fail simultaneously due to a single event or cause. This concept is significant in SIL determination as it could severely impact a system’s ability to perform safety functions. Addressing CCFs typically involves incorporating diversity and redundancy into system design.
Can a Safety Instrumented System (SIS) contain elements of different SIL ratings?
Yes, a Safety Instrumented System (SIS) can contain elements of different SIL ratings. However, the overall SIL of the system cannot exceed the SIL rating of its lowest-rated component, as the system’s integrity is only as strong as its weakest link.
How does Functional Safety Assessment (FSA) influence SIL?
A Functional Safety Assessment (FSA) is an independent assessment process that verifies whether the necessary activities and tasks required by the relevant standards have been completed and are compliant. Its outcome can directly influence the SIL rating, as any identified deficiencies must be rectified to achieve the desired SIL.
How do you calculate Mean Time to Restoration (MTTR)?
Mean Time to Restoration (MTTR) is the average time taken to repair a failed device or restore a system to its operational state after a failure. It can be calculated as the total downtime divided by the number of failures within a specified period.
How do you calculate the Probability of Dangerous Failure per Hour (PFH)?
PFH is calculated by summing the rates of dangerous detected and dangerous undetected failures in a system. It is used to determine the SIL for systems operating in high-demand or continuous mode.
How do you calculate Mean Time Between Failures (MTBF)?
MTBF is calculated as the inverse of the failure rate (λ) for constant failure rate systems. It’s the expected time between consecutive failures in a system.
How do you calculate the Demand Rate (λD)?
The Demand Rate (λD) is the frequency at which a safety function is required to operate. It is usually estimated based on risk analysis and historical data, and it influences the calculation of PFD or PFH for SIL determination.
How does the ‘Fail-Safe Principle’ apply to SIL-rated systems?
The ‘Fail-Safe Principle’ means designing a system in such a way that a failure will lead the system to a safe state. In SIL-rated systems, this principle is a key component of design strategy, particularly for high SIL levels.
How is a SIL Verification Calculation performed?
SIL Verification Calculation is a quantitative analysis performed to verify whether a safety system can meet the target SIL. It typically involves calculating the PFD or PFH of the safety system and comparing it with the target value for the desired SIL.
How does the ‘1oo2’ voting principle relate to achieving a particular SIL?
The ‘1oo2’ (one out of two) voting principle is a redundancy scheme used in safety systems. It requires at least one of two redundant channels to operate correctly for the safety function to be performed. This redundancy enhances the system’s reliability and helps in achieving higher SIL ratings.
What is ‘Safety Margin’ and how does it relate to SIL?
Safety Margin is the degree to which the actual safety performance of a system exceeds the minimum required safety performance. In the context of SIL, safety margin refers to how much the calculated PFD or PFH of a safety function is below the maximum allowed for its SIL. A larger safety margin indicates a higher degree of confidence in achieving the required safety performance.
How does the ‘Fail to Danger Rate’ impact the SIL?
The ‘Fail to Danger Rate’ is the rate at which undetected dangerous failures occur. This rate directly influences the PFD or PFH calculation, and thus, the achievable SIL. Lower fail-to-danger rates help in achieving higher SIL ratings.
How do you calculate the ‘Safe Detected Failure Rate’?
The ‘Safe Detected Failure Rate’ is the rate at which safe failures that can be detected occur. It can be calculated from reliability data for the system components, considering the rates of failure modes that lead to a safe state and are detectable.
Can a subsystem with a lower SIL be used in a safety function with a higher SIL requirement?
As a general rule, a subsystem with a lower SIL cannot fulfill the requirements of a higher SIL safety function on its own. However, additional measures, such as using redundancy or diversity, might enable the overall safety function to meet the higher SIL requirement.
How is the failure rate (λ) of a device used in SIL determination?
The failure rate of a device is a key parameter in calculating PFD or PFH for a safety function, which determines the achievable SIL. Devices with lower failure rates contribute to lower PFD or PFH and can help achieve higher SIL ratings.
How do ‘Diagnostics Test Interval’ and ‘Proof Test Interval’ influence the SIL?
Both the ‘Diagnostics Test Interval’ and ‘Proof Test Interval’ have a direct impact on the SIL. Shorter intervals can lead to early detection of failures, thereby reducing the PFD or PFH and possibly allowing a higher SIL to be achieved.
What is a SIL Compliance Matrix and how is it used?
A SIL Compliance Matrix is a document that maps the requirements of a functional safety standard, like IEC 61508, to the measures taken by a product or system to meet those requirements. It’s used to demonstrate compliance with the standard and to support a SIL claim for the product or system.
How is ‘Random Hardware Failure’ considered in the calculation of SIL?
‘Random Hardware Failure’ contributes to the total failure rate, which is used to calculate the PFD or PFH of a safety function. Thus, it directly influences the SIL. Measures to reduce random hardware failures, such as using high-quality components and good design practices, can help achieve higher SIL ratings.
How is ‘Systematic Failure’ factored into SIL determination?
‘Systematic Failure’ refers to failures that are predictable, repeatable, and can be traced to a specific cause. While these failures do not contribute directly to PFD or PFH calculations, they are considered in SIL determination through safety lifecycle processes and techniques & measures for avoiding systematic failures.
How is the ‘Demand Mode’ operation considered in SIL determination?
In the ‘Demand Mode’ operation, the safety function is only required to operate in response to a specific demand event. The SIL for such systems is determined based on the average probability of failure on demand (PFDavg), which takes into account factors like failure rate, proof test frequency, and demand rate.
How is the ‘Continuous Mode’ operation factored into SIL calculations?
In ‘Continuous Mode’ operation, the safety function is continuously or frequently required to operate. The SIL for these systems is determined based on the probability of dangerous failure per hour (PFH), which takes into account the failure rate and the diagnostics coverage, and the test interval.
What does it mean for a system to ‘degrade gracefully’ in the context of SIL?
A system that ‘degrades gracefully’ is designed to fail in a way that minimizes the impact of the failure. This principle is significant in SIL-rated systems, where it’s essential to ensure that failures don’t lead to catastrophic consequences. The capacity to degrade gracefully can contribute to achieving a higher SIL.
How does ‘Architectural Constraint impact the SIL rating?
‘Architectural Constraints’ define the maximum SIL that can be claimed for a specific hardware architecture, regardless of the calculated PFD or PFH. They are determined based on factors like the type of redundancy used and the safe failure fraction. Adhering to architectural constraints is crucial in achieving the targeted SIL.
How does the ‘Route to Compliance’ affect the SIL achievement?
The ‘Route to Compliance’ is the method chosen to demonstrate that a system meets the requirements for a certain SIL. It could involve using compliant components, applying certified processes, or a combination of both. The chosen route will directly affect the ability to meet and maintain the targeted SIL.
What is a ‘Functional Safety Audit’ and how does it impact the SIL rating?
A ‘Functional Safety Audit’ is an independent examination of a safety system to verify compliance with functional safety standards. The audit findings can impact the SIL rating by identifying deficiencies that need to be rectified to achieve or maintain the required SIL.
What is the relationship between the ‘Safety Manual’ and SIL?
A ‘Safety Manual’ provides instructions and guidelines for the correct use and maintenance of a safety system. In the context of SIL, it contains vital information for achieving and maintaining the required SIL, such as safety function descriptions, installation and commissioning procedures, and requirements for proof testing and maintenance.
Read Next: