Process Control Interview Questions and Expert Answers for Experienced Candidates
Prepare for your process control interview with our expertly-curated collection of questions and answers for your industrial career.
Process Control Interview Questions and Expert Answers
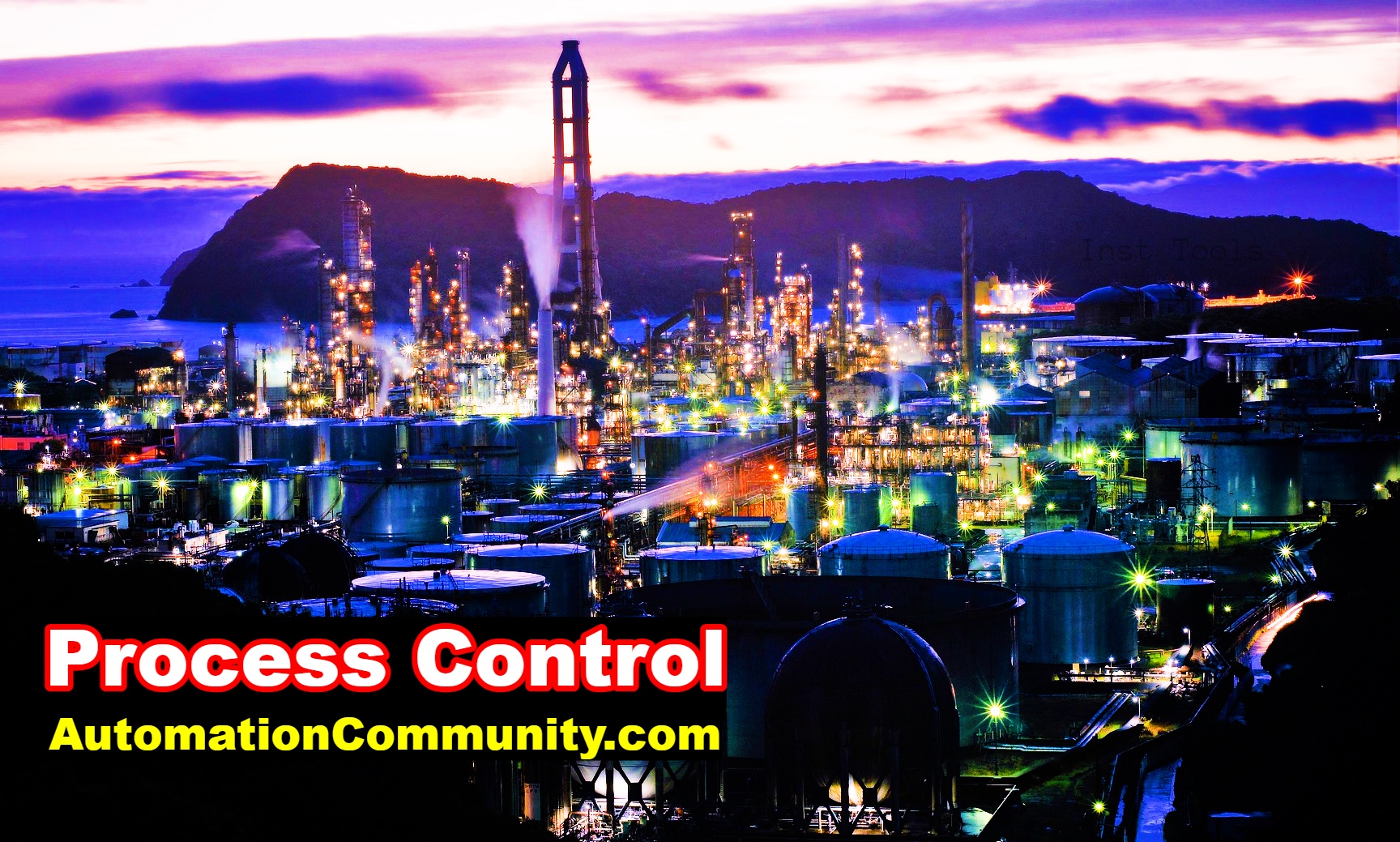
Designed for experienced candidates, this resource covers a broad range of topics, from fundamental principles to advanced process control strategies. Gain the confidence and knowledge you need to impress your interviewers and excel in your process control career.
What is the purpose of process control in an industry?
Process control aims to monitor and regulate various parameters such as temperature, pressure, flow rate, and level in industrial processes. It ensures that these variables remain within desired ranges, promoting operational efficiency, product quality, and safety.
How would you define a control loop?
A control loop consists of a process variable, a sensor to measure the variable, a controller to analyze the measurement and make adjustments, and a final control element to actuate changes in the process. It forms a closed-loop system that continuously monitors and adjusts the process to maintain desired conditions.
What are the main components of a PID controller?
A PID (Proportional-Integral-Derivative) controller comprises three components:
Proportional: Adjusts the control output based on the difference between the measured and desired values.
Integral: Integrates the error over time to eliminate steady-state errors.
Derivative: Reacts to the rate of change of the process variable, helping to stabilize the system response.
How do you determine the appropriate tuning parameters for a control loop?
Tuning parameters for a control loop are usually determined through methods like trial and error, the Ziegler-Nichols method, or advanced techniques like model predictive control (MPC). The aim is to find the right balance between stability and responsiveness for optimal control performance.
What is the purpose of a deadband in control systems?
A deadband is a range around the desired setpoint in which no control action is taken. It prevents unnecessary control adjustments when the process variable is within an acceptable deviation, minimizing wear on control devices and reducing energy consumption.
How would you handle a control loop that exhibits oscillations or instability?
Oscillations in a control loop can be addressed by adjusting the tuning parameters, particularly the proportional and derivative gains. Reducing the gains can help stabilize the system response while implementing filters or smoothing algorithms may also be effective.
What is cascade control and when is it used?
Cascade control involves using two or more control loops in series, where the output of one loop serves as the setpoint for another. It is employed when precise control of an intermediate process variable is crucial to achieving optimal control of the overall system.
How do you approach the integration of safety systems into process control?
Safety systems should be integrated with process control to ensure safe operations. This can be achieved by implementing interlocks, emergency shutdown systems, safety instrumented systems (SIS), and following recognized safety standards like IEC 61511 or ANSI/ISA-84.
Can you explain the concept of feedforward control?
Feedforward control anticipates disturbances by measuring and compensating for them before they affect the process variable. It relies on a predictive model of the process and is often used alongside feedback control to improve overall control performance.
How do you ensure the cybersecurity of process control systems?
Cybersecurity in process control systems involves implementing measures such as firewalls, access controls, network segmentation, encryption, regular software updates, and employee training. It is important to follow industry best practices and stay updated on emerging threats.
Describe your experience with implementing advanced control strategies like model predictive control (MPC)?
Advanced control strategies like MPC utilize mathematical models of the process to optimize control actions. You should highlight their experience in developing or implementing MPC algorithms and how they have improved process performance in previous projects.
How do you monitor and analyze the performance of a control loop?
Performance monitoring can be done through data analysis, statistical process control techniques, and control performance metrics such as control loop oscillation, response time, and steady-state error. Continuous monitoring allows for timely adjustments and ensures efficient control operation.
Can you discuss the role of process instrumentation in effective process control?
Process instrumentation plays a crucial role in process control, providing accurate and reliable measurements of variables like temperature, pressure, and flow rate. It enables the control system to make informed decisions and take appropriate actions to maintain process stability and optimization.
How would you approach troubleshooting a malfunctioning control system?
Troubleshooting a control system involves a systematic approach. You should explain steps like reviewing control algorithms, checking instrumentation, examining communication networks, and collaborating with relevant stakeholders to identify and resolve the underlying issues.
Can you describe a project where you successfully optimized a process control system for improved efficiency or cost reduction?
You should provide an example of a project where they identified inefficiencies, implemented control strategies, or fine-tuned existing control loops to achieve measurable improvements such as reduced energy consumption, increased throughput, or cost savings.
How do you handle the integration of process control systems with other plant-wide automation systems?
Integrating process control systems with other automation systems involves ensuring seamless communication and data exchange between different subsystems. You should mention their experience in working with protocols like OPC (OLE for Process Control) or using middleware solutions to enable interoperability.
Can you explain the concept of multi-variable control and its advantages?
Multi-variable control involves considering multiple process variables simultaneously to optimize control actions. This approach allows for coordinated control, taking into account the interactions and dependencies between variables. You should highlight the benefits of improved stability, reduced variability, and enhanced overall system performance.
How do you address control system performance degradation over time?
Control system performance degradation can occur due to factors like aging instrumentation, changes in process dynamics, or drift in control algorithms. You should mention strategies such as regular maintenance, periodic tuning adjustments, and monitoring performance metrics to proactively identify and rectify performance degradation.
Can you discuss the role of data analytics and machine learning in process control?
Data analytics and machine learning techniques can be used to extract valuable insights from process data, identify patterns, and predict future behavior. You should mention applications such as anomaly detection, predictive maintenance, or optimizing control strategies using historical and real-time data.
How would you approach control system redundancy and fault tolerance?
Redundancy and fault tolerance in control systems involve duplicating critical components or implementing backup systems to ensure continuous operation in the event of failures. You should discuss techniques like redundant controllers, backup power supplies, or implementing fault detection and isolation algorithms.
How do you ensure compliance with regulatory standards and industry best practices in process control?
Compliance with regulatory standards requires understanding and adhering to specific guidelines, such as those outlined by organizations like the International Society of Automation (ISA) or regulatory bodies. Youshould emphasize the importance of documentation, audits, and regular reviews to ensure compliance.
Can you describe a situation where you successfully implemented advanced control strategies like fuzzy logic or neural networks?
You should provide an example where they applied advanced control strategies beyond PID control, such as fuzzy logic or neural networks. They should explain the problem they addressed, the implementation approach, and the resulting benefits in terms of improved control performance or enhanced system efficiency.
How do you handle the challenges of control system upgrades or migrations?
Upgrading or migrating control systems can be complex and require careful planning. You should mention their experience in conducting system assessments, creating migration plans, ensuring compatibility between old and new systems, and minimizing disruptions during the transition.
Can you discuss the importance of operator training and interface design in effective process control?
Operator training and intuitive interface design are crucial for effective process control. You should emphasize the importance of providing operators with comprehensive training on system functionality and response to different scenarios. They should also highlight the significance of clear, user-friendly interfaces to facilitate operator decision-making and response.
How do you approach process control optimization for energy efficiency?
You should discuss their approach to identifying energy-intensive processes, monitoring energy consumption, and implementing control strategies to optimize energy usage. They should mention techniques like demand control, load balancing, or implementing energy management systems to achieve energy efficiency goals.
Can you explain the concept of adaptive control and its applications?
Adaptive control involves adjusting control parameters in real-time based on changing process dynamics or conditions. You should discuss how adaptive control algorithms can improve control performance in situations where process characteristics vary or change over time, such as in batch processes or systems with varying disturbances.
How do you address cybersecurity risks in process control systems, especially in the context of increasing connectivity and industrial IoT?
You should mention measures like network segmentation, strong access controls, regular vulnerability assessments, implementing security patches, and promoting cybersecurity awareness among personnel. They should also emphasize the importance of staying updated on emerging threats and best practices in industrial cybersecurity.
Can you describe your experience in conducting root cause analysis for control system failures or abnormal behavior?
You should discuss their experience in investigating control system failures or anomalies, including their approach to root cause analysis. They should mention techniques like fault tree analysis, data analysis, or conducting physical inspections to identify the underlying causes and implement corrective actions.
How do you ensure the scalability and flexibility of process control systems to accommodate future expansions or modifications?
Scalability and flexibility are crucial considerations in designing process control systems. You should mention their experience in using modular architectures, selecting scalable hardware and software platforms, and adopting open standards to accommodate future expansions or modifications with minimal disruptions.
Can you discuss the role of real-time monitoring and control in ensuring process safety?
Real-time monitoring and control systems play a vital role in ensuring process safety. You should emphasize how these systems enable timely detection of abnormal conditions or deviations from safe operating limits, allowing for immediate corrective actions or activating safety measures to prevent accidents or equipment damage.
How can advanced control techniques such as model predictive control (MPC) improve process performance?
Advanced control techniques like model predictive control (MPC) utilize mathematical models of the process to predict future behavior and optimize control actions. MPC considers constraints, process dynamics, and objectives to make optimal decisions, resulting in improved process performance, reduced variability, increased efficiency, and better response to disturbances.
What are the benefits of implementing adaptive control in process control systems?
Adaptive control continuously adjusts control parameters based on changing process conditions, variations, and uncertainties. The benefits include improved stability, enhanced control performance in the face of disturbances or parameter changes, reduced manual tuning requirements, and increased robustness against system uncertainties.
How can real-time optimization (RTO) be applied in process control?
Real-time optimization (RTO) involves continuously optimizing process variables based on real-time data and dynamic models. It allows for optimal setpoints and operating conditions to be determined, considering objectives such as energy efficiency, production rates, quality, and cost savings. RTO can lead to improved process performance, increased productivity, and reduced resource consumption.
What are the key considerations in implementing multivariable control (MVC) in process systems?
Implementing multivariable control (MVC) requires a detailed understanding of process interactions and dynamics. Key considerations include model identification and validation, selection of appropriate control strategies, managing coupling and interactions between variables, tuning of control loops, and addressing issues of stability and robustness.
How does predictive maintenance play a role in process control?
Predictive maintenance utilizes advanced analytics and condition monitoring techniques to detect potential equipment failures or performance degradation before they occur. By proactively identifying issues, maintenance can be scheduled at optimal times, minimizing downtime, maximizing equipment reliability, and optimizing overall process performance.
What are the challenges and benefits of integrating process control systems with industrial Internet of Things (IIoT) technologies?
Integrating process control systems with IIoT technologies allows for real-time data collection, analysis, and remote monitoring. Challenges include ensuring data security, managing the scale and complexity of data, and interoperability between different devices and systems. The benefits include improved visibility, predictive analytics, enhanced decision-making, and the potential for autonomous or self-optimizing systems.
How do machine learning and artificial intelligence (AI) impact process control?
Machine learning and AI techniques can analyze large amounts of process data, identify patterns, and make predictions or recommendations for optimal control actions. They can assist in fault detection, optimization, anomaly detection, and adaptive control, leading to improved process efficiency, reduced maintenance costs, and enhanced overall performance.
What is Model Predictive Control (MPC), and how does it differ from traditional control methods?
Model Predictive Control (MPC) is an advanced control technique that utilizes mathematical models of the process to predict future behavior and optimize control actions. Unlike traditional control methods, MPC considers process constraints, dynamics, and objectives in real-time, allowing for more accurate and proactive control decisions.
How does Adaptive Control differ from traditional control approaches?
Adaptive Control continuously adjusts control parameters based on changing process conditions and uncertainties. It adapts to variations or changes in the process by updating the controller based on real-time measurements. In contrast, traditional control approaches use fixed control parameters and do not account for dynamic changes or uncertainties.
What are the advantages of using Neural Network Control (NNC) in process control?
Neural Network Control (NNC) is effective for controlling complex systems with non-linearities and time-varying dynamics. NNC utilizes artificial neural networks to model the process and generate control signals based on historical data. The advantages include improved control performance in non-linear systems and the ability to handle complex relationships and uncertainties.
How can Fuzzy Logic Control (FLC) be beneficial in process control applications?
Fuzzy Logic Control (FLC) is particularly useful when dealing with uncertain or imprecise information. By employing linguistic variables and fuzzy rules, FLC can effectively handle non-linear systems and uncertainties. FLC provides a flexible and intuitive control approach, allowing for better control performance and robustness.
What is Multivariable Control (MVC), and when is it used?
Multivariable Control (MVC) deals with systems with multiple input and output variables. It considers interactions between variables and optimally controls them to achieve desired performance. MVC techniques, such as decentralized control or centralized control with coordination, are used when controlling individual variables independently is not sufficient or may lead to suboptimal performance.
What are some common process control problems faced in industries?
Industries often encounter various process control problems, including:
- Oscillations and instability: Unstable control loops can result in oscillations, leading to inconsistent process performance and product quality.
- Non-linearity: Many industrial processes exhibit non-linear behavior, which can pose challenges for traditional control techniques designed for linear systems.
- Dead-time: Dead-time refers to delays in the process response to control actions. It can lead to sluggish control and difficulties in achieving desired setpoints.
- Disturbance rejection: Industrial processes are often subjected to disturbances, such as changes in raw material properties, environmental conditions, or equipment malfunctions. Effective disturbance rejection is crucial for maintaining stable and optimal operation.
- Multivariable interactions: In complex systems, interactions between multiple process variables can complicate control efforts, as changes in one variable can affect others.
- Constraints: Processes may have physical or operational constraints that need to be considered in control strategies. Failure to address these constraints can lead to suboptimal control performance or even safety issues.
- Model mismatch: Inaccurate process models or uncertainty in model parameters can lead to discrepancies between predicted and actual process behavior, affecting control performance.
- Controller tuning: Proper tuning of control loops is critical for achieving stable and responsive control. However, finding the optimal tuning parameters can be challenging, especially for complex systems with varying operating conditions.
- Sensor noise and measurement errors: Imperfections in sensor measurements, such as noise, drift, or calibration errors, can impact control system performance and accuracy.
How can advanced process control techniques address these industry-specific control problems?
Advanced process control techniques provide solutions for industry-specific control problems by leveraging advanced algorithms and strategies. For example:
- Model Predictive Control (MPC) can handle non-linearities, dead time, and constraints, allowing for optimized control even in complex systems.
- Adaptive Control can adapt to changing process conditions, providing robust and responsive control performance in the presence of uncertainties.
- Neural Network Control (NNC) and Fuzzy Logic Control (FLC) are capable of handling non-linearities and uncertainties, offering improved control performance.
- Multivariable Control (MVC) techniques consider interactions between variables, ensuring coordinated control and optimal system-wide performance.
- Real-Time Optimization (RTO) continuously optimizes process variables, taking into account dynamic conditions and objectives, leading to improved efficiency and profitability.
- Soft Sensing techniques enable the estimation of unmeasured variables, enhancing process monitoring and control.
How can advanced process control techniques help in improving energy efficiency in industries?
Advanced process control techniques play a vital role in improving energy efficiency in industries by optimizing process variables, minimizing energy consumption, and reducing waste.
Some ways in which these techniques contribute to energy efficiency include:
- Optimal setpoint selection: Advanced control algorithms can determine optimal setpoints for process variables, considering energy consumption and production requirements. This ensures that the process operates at the most energy-efficient operating points.
- Load balancing: Advanced control strategies can balance loads across different units or equipment, avoiding unnecessary energy consumption and optimizing resource utilization.
- Demand response: By utilizing real-time data and predictive models, advanced control techniques can enable effective demand response strategies, allowing industries to participate in energy management programs and reduce energy costs during peak demand periods.
- Equipment optimization: Advanced control techniques can optimize the operation of equipment, such as compressors, pumps, or fans, by adjusting control parameters based on real-time conditions. This minimizes energy losses and improves overall efficiency.
- Process integration: Advanced control methods facilitate the integration of various process units, allowing for energy exchange and optimization across the entire system. This integration can help capture waste heat or utilize excess energy from one unit to meet the requirements of another.
- Process modeling and optimization: Accurate process models coupled with optimization algorithms enable the identification of energy-efficient operating regimes, optimal control strategies, and the reduction of energy-intensive operations.
How do advanced process control techniques contribute to improving product quality in industries?
Advanced process control techniques have a significant impact on improving product quality in industries by enabling tighter control over process variables and reducing variability.
Here are some ways in which these techniques contribute to enhanced product quality:
- Tighter control: Advanced control algorithms allow for precise control over process variables, minimizing deviations from setpoints and ensuring consistent product quality.
- Enhanced disturbance rejection: Advanced control techniques can effectively reject disturbances and variations in process conditions, preventing them from affecting product quality.
- Non-linear process handling: Many industrial processes exhibit non-linear behavior that can impact product quality. Advanced control techniques, such as model predictive control (MPC) and fuzzy logic control (FLC), are well-suited to handle non-linearities, maintaining product quality even in complex systems.
- Multivariable optimization: Advanced process control techniques consider interactions between multiple process variables, optimizing their values simultaneously to achieve the desired product quality. This ensures that all variables are controlled in harmony, minimizing the risk of one variable negatively affecting the quality of another.
- Real-time monitoring and adjustments: Advanced control systems continuously monitor key process variables and make real-time adjustments to maintain product quality within specified tolerances. This allows for prompt corrective actions in case of deviations.
- Statistical process control: Advanced process control techniques can incorporate statistical process control methods, enabling the monitoring and analysis of process data to identify trends, anomalies, and potential quality issues. This proactive approach helps to identify and address quality-related problems early on.
- Model-based control: Advanced control techniques utilize mathematical models of the process to predict its behavior. These models can be refined and updated over time, enabling better control performance and adherence to quality standards.
Read Next: