Honeywell Safety and Productivity Solutions Questions and Answers
Honeywell Safety and Productivity Solutions is like a big toolbox for businesses, especially those in industries like manufacturing, logistics, and retail.
Let’s break it down in simple terms:
Safety Gear (PPE): Imagine you’re a worker in a factory; Honeywell SDS makes special helmets, gloves, goggles, and other gear to keep you safe from accidents or harmful materials.
Connected Workers: Think of a team of workers all wearing smartwatches that talk to each other. This part of Honeywell SDS helps workers and bosses communicate, share information, and keep track of what’s happening in real-time.
Vehicle Computers: If you’re a truck driver, Honeywell SDS puts a special computer in your truck that helps you find the best route, track shipments, and make sure everything’s running smoothly.
Thermal Printing: Imagine you’re in a shop, and you need to print price tags or shipping labels quickly. Honeywell SDS has special printers that do this fast and in different ways, depending on what you need.
Automation Tools: Think of a conveyor belt in a warehouse that sorts and moves boxes all by itself. Honeywell SDS creates tools and machines that can do many things automatically, making work easier and more efficient.
Data Collection and Analysis: Imagine a coach keeping track of a team’s performance. Honeywell SDS collects information on how things are going in a business and helps managers understand what’s working well and what needs to improve.
Custom Solutions: Every business is different, just like every person has unique needs. Honeywell SDS works with companies to create special tools and solutions that fit just right.
In simple terms, Honeywell SDS is like a friend to businesses, helping them do their work better, safer, and more efficiently by providing all kinds of cool tools and technology. Whether it’s keeping workers safe, making deliveries quicker, or printing labels, Honeywell SDS has something to help!
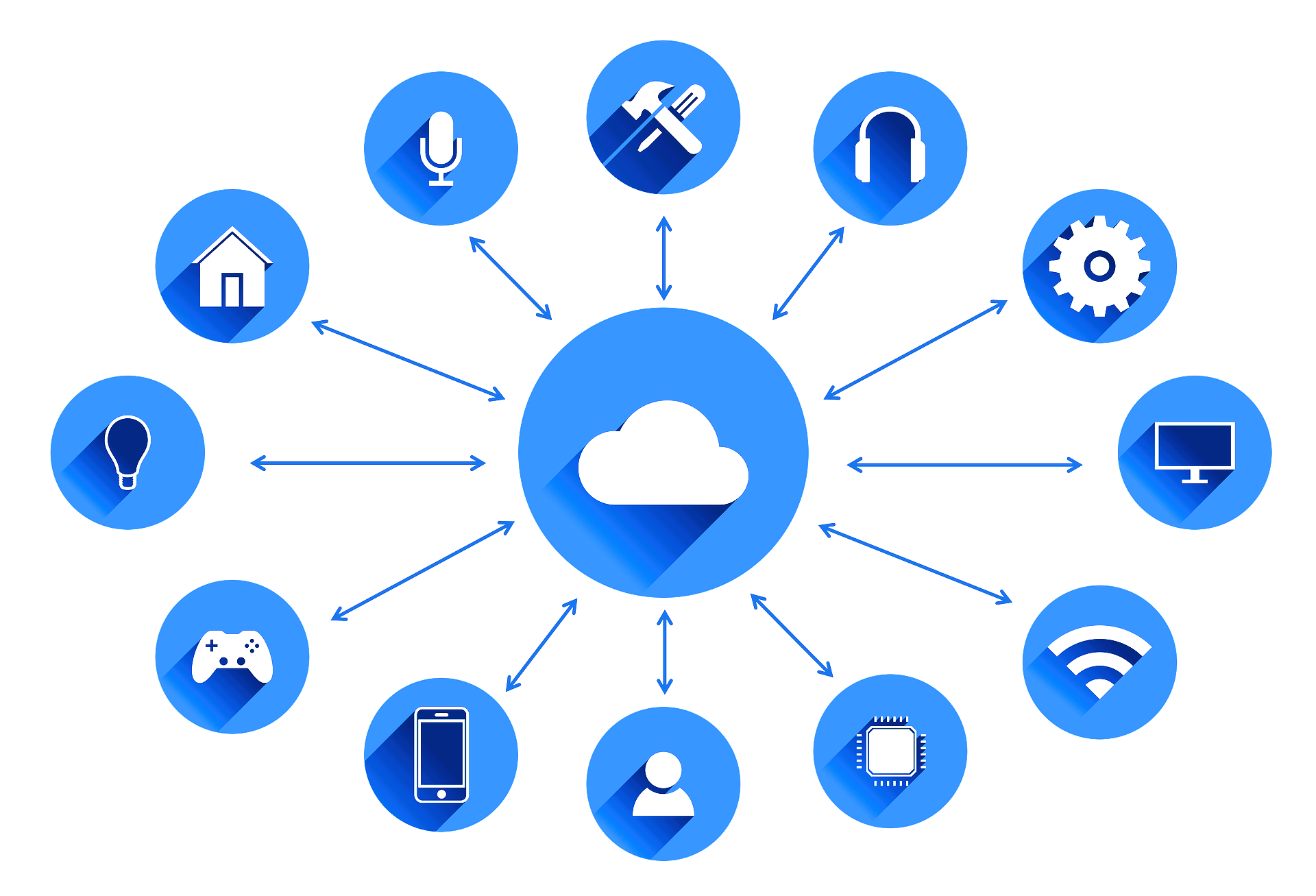
What is Honeywell SDS, and what is its primary function?
Honeywell Safety and Productivity Solutions (SDS) is a division of Honeywell that focuses on providing products, software, and services to enhance productivity, workplace safety, and asset performance. Its primary function is to assist industries like manufacturing, supply chain, healthcare, and others in improving their efficiency, safety standards, and compliance with regulations.
How does Honeywell SDS contribute to workplace safety?
Honeywell SDS offers a range of safety products such as personal protective equipment (PPE), gas detection systems, and safety software. By providing these tools, Honeywell SDS helps organizations to monitor and control potential hazards, ensuring a safer working environment for employees.
What types of industries can benefit from Honeywell SDS products and solutions?
Honeywell SDS provides solutions for various industries, including manufacturing, logistics, retail, healthcare, construction, and aerospace. By offering tailored products and services, Honeywell SDS helps these industries meet specific safety and productivity challenges.
What are some examples of Honeywell SDS’s personal protective equipment (PPE)?
Honeywell SDS offers a wide range of PPE, including safety eyewear, hearing protection, respirators, protective gloves, and safety footwear. These items are designed to protect workers from specific hazards such as chemicals, noise, airborne particles, and physical injuries.
How does Honeywell SDS’s gas detection technology work?
Honeywell SDS’s gas detection technology includes portable and fixed devices that monitor the presence of harmful gases and vapors. Using advanced sensors, these devices can detect specific gases at various concentrations and alert workers or management if dangerous levels are reached. This technology helps prevent exposure to toxic substances and ensures compliance with safety regulations.
Can Honeywell SDS solutions be integrated with existing systems?
Yes, Honeywell SDS provides solutions that can be integrated with existing systems and workflows. This flexibility allows organizations to implement Honeywell’s safety and productivity tools without completely overhauling their current infrastructure, enabling a smoother transition and maximizing the value of previous investments.
How does Honeywell SDS support asset performance management?
Honeywell SDS offers asset performance management solutions that help organizations monitor, maintain, and optimize their physical assets. By providing real-time data, predictive analytics, and maintenance tools, Honeywell SDS enables companies to reduce downtime, extend asset life, and increase overall efficiency.
What kind of support and training does Honeywell SDS provide for its customers?
Honeywell SDS offers comprehensive support and training to its customers. This includes technical support, product training, maintenance services, and consultation on best practices. The aim is to ensure that customers can effectively utilize Honeywell’s solutions and achieve their safety and productivity goals.
How does Honeywell SDS utilize data analytics in its solutions?
Honeywell SDS leverages data analytics to collect and analyze vast amounts of data from various sources, including sensors, equipment, and software. This data-driven approach enables organizations to gain insights into their operations, identify inefficiencies, predict potential problems, and make informed decisions. By utilizing data analytics, Honeywell SDS helps customers optimize performance, reduce waste, and enhance safety measures.
What is the role of Honeywell SDS in healthcare settings?
In healthcare settings, Honeywell SDS offers solutions for patient care, asset management, and facility monitoring. These include barcode scanners for patient identification, mobile computers for medical staff, and sensors for monitoring environmental conditions. By integrating these technologies, Honeywell SDS helps healthcare providers enhance patient safety, streamline workflows, and maintain regulatory compliance.
How does Honeywell SDS contribute to sustainable practices?
Honeywell SDS supports sustainability by offering products and solutions that minimize waste, reduce energy consumption, and promote efficient use of resources. This includes energy-saving technologies, waste reduction strategies, and tools to monitor environmental impact. By fostering sustainable practices, Honeywell SDS aids organizations in meeting their environmental goals and compliance with green regulations.
What are the key features of Honeywell SDS’s warehouse management solutions?
Honeywell SDS’s warehouse management solutions offer features like inventory tracking, order processing, labor management, and shipment coordination. Utilizing barcode scanners, mobile computers, and software platforms, these solutions provide real-time visibility into warehouse operations, automate manual processes, and optimize space utilization. The goal is to enhance productivity, reduce errors, and enable agile responses to market demands.
How does Honeywell SDS ensure the reliability of its products?
Honeywell SDS employs rigorous quality control measures, including thorough testing, certification, and compliance with industry standards. By evaluating the performance, durability, and safety of its products, Honeywell ensures that they meet the expectations of customers and function reliably in various environments and conditions.
Can Honeywell SDS provide customized solutions to meet specific industry needs?
Yes, Honeywell SDS offers customized solutions tailored to the specific needs and challenges of different industries. By working closely with customers to understand their unique requirements, Honeywell SDS can design and implement solutions that align with their goals and integrate seamlessly with existing systems. This collaborative approach ensures that the provided solutions offer maximum value and effectiveness.
What is Honeywell SDS’s approach to cybersecurity in its solutions?
Honeywell SDS takes a comprehensive approach to cybersecurity by implementing multi-layered security measures in its products and services. This includes encryption, authentication, access control, and continuous monitoring. By safeguarding data and network integrity, Honeywell SDS helps customers protect their critical information and maintain the trust of stakeholders.
How does Honeywell SDS’s voice-directed technology enhance productivity?
Honeywell SDS’s voice-directed technology allows workers to receive instructions and provide feedback using voice commands. This hands-free approach streamlines tasks such as picking, packing, and inventory management, reducing manual errors and enhancing efficiency. By enabling workers to interact naturally with systems, Honeywell SDS’s voice technology fosters a more intuitive and agile working environment.
What are the primary considerations for implementing Honeywell SDS solutions in a manufacturing environment?
Implementing Honeywell SDS solutions in a manufacturing environment requires careful consideration of factors such as:
Compatibility: Ensuring that the chosen solutions integrate seamlessly with existing systems and processes.
Specific Needs: Identifying the particular challenges and requirements of the manufacturing process that the solutions need to address.
Training: Providing proper training to staff on the usage and maintenance of new equipment and software.
Compliance: Ensuring that the solutions comply with industry regulations and standards.
ROI Analysis: Evaluating the cost-effectiveness and potential return on investment of the implemented solutions.
Honeywell SDS typically works closely with customers to assess these factors and customize solutions that best meet their needs.
How does Honeywell SDS’s mobility solutions enhance field operations?
Honeywell SDS’s mobility solutions include tools like mobile computers, tablets, and software applications designed to empower field workers. These tools:
Provide Real-time Access: Field workers can access crucial information, like customer data, work orders, and inventory levels, on the go.
Enhance Communication: Mobility solutions enable seamless communication between field staff and the central office, allowing for quicker decision-making.
Increase Efficiency: Automation of manual processes and paperless documentation saves time and reduces errors.
Improve Customer Service: With access to real-time data, field workers can respond to customer needs more effectively and provide timely service.
Overall, mobility solutions enhance productivity, accuracy, and responsiveness in field operations.
How does Honeywell SDS assist in the management of cold chain logistics?
Cold chain logistics involves the transportation and storage of temperature-sensitive goods, such as food and pharmaceuticals. Honeywell SDS assists in this area by:
Monitoring Temperature: Providing sensors and monitoring systems to track temperature continuously, ensuring that goods are kept within required ranges.
Enhancing Visibility: Offering tracking tools that provide real-time visibility into the location and condition of shipments.
Ensuring Compliance: Facilitating adherence to regulatory requirements by maintaining accurate records and providing reporting tools.
Improving Efficiency: Utilizing automation and data analytics to optimize routes, reduce energy consumption, and minimize waste.
Honeywell SDS’s solutions enable organizations to maintain the integrity of temperature-sensitive goods throughout the supply chain, reducing spoilage and ensuring quality.
What are Honeywell SDS’s software platforms, and how do they integrate with hardware solutions?
Honeywell SDS offers various software platforms designed to work with its hardware solutions, such as scanners, mobile computers, and sensors. These platforms may include:
Warehouse Management Systems (WMS): Facilitating inventory control, order processing, and overall warehouse optimization.
Asset Performance Management (APM): Enabling real-time monitoring, predictive maintenance, and analytics for physical assets.
Field Service Solutions: Supporting field workers with scheduling, route planning, and customer engagement tools.
These software platforms are engineered to integrate seamlessly with Honeywell’s hardware, providing a cohesive ecosystem that enhances functionality, usability, and overall efficiency.
How does Honeywell SDS promote innovation in its products and solutions?
Honeywell SDS promotes innovation by:
Investing in Research and Development (R&D): Funding R&D activities to explore new technologies, materials, and methodologies.
Collaborating with Customers: Working closely with customers to understand their unique challenges and developing tailored solutions.
Partnering with Academia and Industry Experts: Engaging in partnerships to leverage external knowledge and expertise.
Emphasizing Sustainability: Innovating in ways that support environmental stewardship and social responsibility.
Fostering a Culture of Innovation: Encouraging creativity and experimentation within the organization.
Through these strategies, Honeywell SDS ensures that it stays at the forefront of technology and continues to offer cutting-edge products and solutions.
What role does Honeywell SDS play in enhancing retail operations?
Honeywell SDS plays a vital role in retail operations by providing technologies and solutions that focus on the following areas:
Customer Experience: Offering tools like self-service kiosks and mobile scanners that enhance the shopping experience.
Inventory Management: Providing solutions to track and manage inventory in real-time, reducing overstock and stockouts.
Labor Efficiency: Implementing systems that automate routine tasks, allowing staff to focus on customer interaction and value-added services.
Data Analytics: Utilizing data to analyze shopping patterns, optimize store layouts, and personalize marketing strategies.
Loss Prevention: Implementing security measures, such as Electronic Article Surveillance (EAS), to reduce theft.
Omni-channel Integration: Ensuring seamless integration between in-store, online, and mobile channels for a unified shopping experience.
Through these multifaceted approaches, Honeywell SDS helps retailers improve efficiency, profitability, and customer satisfaction.
How does Honeywell SDS support automation in logistics and supply chain management?
Honeywell SDS supports automation in logistics and supply chain management through various tools and technologies, including:
Warehouse Automation: Utilizing robotics, conveyance systems, and warehouse management software to automate tasks such as picking, packing, and sorting.
Transportation Optimization: Implementing software solutions that plan and optimize routes, considering factors like traffic, delivery windows, and fuel efficiency.
Real-time Tracking: Providing sensors and tracking systems that offer real-time visibility of shipments and assets.
Predictive Analytics: Applying machine learning and analytics to predict potential disruptions and automate decision-making processes.
Integration with Suppliers and Partners: Offering platforms that facilitate seamless collaboration with suppliers, carriers, and other partners, automating information exchange and coordination.
These solutions enable logistics and supply chain managers to streamline operations, reduce costs, and increase responsiveness to market demands.
What types of Honeywell SDS’s handheld devices are used in industrial settings, and what are their functions?
Honeywell SDS offers various handheld devices designed for industrial settings, each serving specific functions:
Barcode Scanners: These devices read barcodes and QR codes on products and components, aiding in inventory management, tracking, and quality control.
Mobile Computers: Offering robust computing power in a handheld format, these devices support data collection, communication, and task management on the factory floor.
Portable Printers: Enabling on-the-go printing of labels, receipts, and other documents, these printers support various industrial processes and documentation requirements.
Gas Detectors: These handheld devices monitor the presence of harmful gases in the environment, alerting workers to potential hazards and maintaining safety compliance.
Rugged Tablets: Designed to withstand harsh industrial conditions, these tablets provide access to manuals, schematics, and other essential information, enhancing productivity and decision-making.
These handheld devices are essential tools in modern industrial operations, enhancing efficiency, accuracy, and safety.
How does Honeywell SDS facilitate regulatory compliance in various industries?
Compliance with industry regulations is crucial, and Honeywell SDS facilitates this through:
Customized Solutions: Designing products and services that adhere to industry-specific regulations, standards, and best practices.
Monitoring and Reporting Tools: Providing systems that continuously monitor compliance-related metrics and generate reports required by regulatory authorities.
Consultation and Support: Offering expert advice and ongoing support to ensure that customers understand and meet their compliance obligations.
Integration with Existing Systems: Ensuring that Honeywell’s solutions can integrate with existing compliance management systems, providing a cohesive approach to meeting regulatory requirements.
Training and Education: Conducting training sessions and providing educational materials to ensure that users understand how to use Honeywell’s products in a manner that maintains compliance.
By focusing on these areas, Honeywell SDS helps organizations navigate complex regulatory landscapes, reduce the risk of non-compliance, and maintain their reputation and integrity.
What methods does Honeywell SDS employ to ensure the quality of its products and solutions?
Honeywell SDS employs various methods to maintain and ensure the quality of its products and solutions, including:
Quality Standards: Adhering to international quality standards such as ISO 9001 and industry-specific certifications.
Testing and Validation: Conducting rigorous testing under various conditions to validate performance, durability, and functionality.
Customer Collaboration: Working closely with customers to understand their specific needs and tailoring products accordingly.
Supplier Management: Implementing stringent supplier qualification and monitoring processes to ensure the quality of raw materials and components.
Continuous Improvement: Applying methodologies like Six Sigma to continuously analyze and improve processes.
Compliance and Regulatory Adherence: Ensuring that products meet all applicable legal and regulatory requirements.
These combined efforts contribute to the consistent delivery of high-quality products that meet or exceed customer expectations.
How does Honeywell SDS leverage Internet of Things (IoT) technology in its solutions?
Honeywell SDS leverages Internet of Things (IoT) technology to create interconnected systems that enhance various aspects of operations, including:
Real-time Monitoring: Using sensors and connected devices to monitor equipment, environmental conditions, and other variables in real-time.
Predictive Maintenance: Utilizing IoT data and analytics to predict equipment failures and schedule timely maintenance.
Asset Tracking: Enabling precise tracking of assets and inventory across supply chains through IoT-enabled devices.
Energy Efficiency: Monitoring and controlling energy consumption through IoT-enabled energy management systems.
Remote Operations: Facilitating remote control and monitoring of machinery, systems, and processes.
Enhanced Collaboration: Allowing seamless data sharing and collaboration between different departments, partners, and stakeholders.
By harnessing IoT technology, Honeywell SDS delivers smarter, more responsive, and more efficient solutions.
How does Honeywell SDS support healthcare providers in improving efficiency and patient care?
Honeywell SDS supports healthcare providers by offering various technologies and solutions that enhance both efficiency and patient care, such as:
Patient Tracking: Utilizing RFID and barcode technologies to monitor patient movements, ensuring safety and timely care.
Asset Management: Tracking medical equipment and supplies, reducing search times and improving availability.
Data Integration: Facilitating seamless integration of patient data between different systems and departments, enhancing coordination and decision-making.
Pharmacy Automation: Automating medication dispensing and tracking to minimize errors and enhance efficiency.
Infection Control: Offering solutions to monitor hygiene and infection control protocols.
Mobile Healthcare Solutions: Providing mobile devices and applications to support healthcare staff in accessing information and communicating effectively on the go.
These technologies enable healthcare providers to offer more personalized, responsive, and efficient care, contributing to improved patient outcomes.
How does Honeywell SDS approach sustainability in its products, solutions, and operations?
Honeywell SDS’s approach to sustainability encompasses various aspects, including:
Eco-Friendly Design: Designing products that consume less energy, use recyclable materials, and minimize waste.
Energy Efficiency Solutions: Offering solutions that help customers reduce their energy consumption and carbon footprint.
Sustainable Supply Chain Management: Implementing practices that promote responsible sourcing and reduce environmental impacts throughout the supply chain.
Community Engagement: Participating in community initiatives that promote environmental stewardship and social responsibility.
Compliance with Environmental Regulations: Ensuring that all products, operations, and facilities meet or exceed applicable environmental regulations and standards.
Employee Training and Awareness: Encouraging employees to engage in sustainable practices both at work and at home.
Honeywell SDS’s commitment to sustainability reflects a holistic approach that integrates environmental responsibility into all aspects of its business.
What types of customer support and services does Honeywell SDS provide to ensure the successful implementation and use of its solutions?
Honeywell SDS offers comprehensive customer support and services to ensure successful implementation and ongoing use of its solutions, including:
Pre-Sale Consultation: Assisting customers in identifying the most suitable products and solutions for their specific needs.
Implementation Support: Providing technical expertise to guide and support the successful installation and integration of products.
Training and Education: Offering training programs to ensure that users understand how to use the products effectively.
Technical Support: Providing ongoing technical support through various channels such as phone, email, and online portals.
Maintenance and Repair Services: Offering regular maintenance, repair, and upgrade services to ensure that products continue to function optimally.
Customized Services: Creating tailored service packages based on the unique requirements and challenges of each customer.
Feedback and Continuous Improvement: Actively seeking customer feedback and using it to continuously improve products and services.
Through these comprehensive support mechanisms, Honeywell SDS fosters strong customer relationships and ensures that its products and solutions deliver maximum value.
What role does Honeywell SDS play in the manufacturing industry, and how does it support manufacturers?
Honeywell SDS plays a pivotal role in the manufacturing industry by offering solutions that enhance efficiency, safety, and productivity, including:
Automation Solutions: Implementing robotics, automated conveyors, and other automated systems that reduce manual labor and enhance efficiency.
Quality Control Systems: Providing inspection systems and quality control technologies that ensure the production of high-quality products.
Data Analytics and Insights: Utilizing data analytics tools to monitor and analyze production processes, enabling predictive maintenance and process optimization.
Supply Chain Visibility: Offering solutions for real-time tracking and management of materials and finished goods throughout the supply chain.
Workforce Management: Implementing systems to manage scheduling, task assignment, and performance monitoring, fostering a more productive workforce.
Compliance and Safety Solutions: Ensuring that manufacturing processes meet regulatory standards and safety requirements through tailored compliance solutions.
By focusing on these areas, Honeywell SDS supports manufacturers in staying competitive, reducing costs, and maintaining the highest levels of quality and safety.
How does Honeywell SDS contribute to the safety of workers in various industries?
Honeywell SDS places significant emphasis on worker safety and provides solutions tailored to various industries, such as:
Personal Protective Equipment (PPE): Offering a wide range of PPE, including helmets, gloves, and respiratory protection, to safeguard workers from occupational hazards.
Gas Detection Systems: Implementing gas detection systems that continuously monitor for harmful gases, providing immediate alerts to protect workers.
Ergonomic Solutions: Designing products and systems that promote ergonomic well-being, reducing the risk of strain and injury.
Safety Training and Education: Providing comprehensive training programs that educate workers on safety practices and equipment usage.
Emergency Response Solutions: Offering tools and systems that enable quick and effective response to emergencies, minimizing potential harm.
Safety Compliance Management: Implementing solutions that help organizations comply with industry-specific safety regulations and standards.
Through these multifaceted safety initiatives, Honeywell SDS helps organizations create a safer working environment, minimizing accidents and related costs.
How does Honeywell SDS’s mobility solutions enhance field operations for various businesses?
Honeywell SDS’s mobility solutions are designed to enhance field operations across various industries, and they encompass:
Mobile Computers and Devices: Offering rugged and reliable mobile devices that enable field workers to access essential information, communicate, and perform tasks on the go.
Real-time Data Synchronization: Providing solutions that allow real-time synchronization of data between field workers and central systems, ensuring accurate and up-to-date information.
Route Optimization Tools: Implementing software that helps in planning and optimizing routes, saving time and fuel.
Remote Collaboration and Support: Facilitating remote collaboration and support through video conferencing and remote assistance tools, enhancing problem-solving capabilities in the field.
Task Management and Scheduling: Enabling efficient task management and scheduling, ensuring that field workers are aligned with organizational priorities.
Security Measures: Implementing robust security measures to protect sensitive data accessed and transmitted by field devices.
By focusing on these elements, Honeywell SDS’s mobility solutions enable organizations to extend their reach, improve responsiveness, and increase the efficiency of their field operations.
How does Honeywell SDS enable digital transformation within organizations?
Honeywell SDS supports digital transformation within organizations through a holistic approach that includes:
Integration of Systems and DatA:Facilitating the seamless integration of various systems, platforms, and data sources, creating a cohesive digital environment.
Automation of Processes: Implementing automated solutions that streamline manual processes, enhancing efficiency and accuracy.
Analytics and Intelligence: Utilizing advanced analytics and artificial intelligence to generate insights, enabling better decision-making and forecasting.
Cloud-Based Solutions: Offering cloud-based platforms that provide scalability and flexibility, supporting growth and innovation.
Enhanced Collaboration and Communication: Implementing collaboration tools that foster better communication and coordination within and outside the organization.
Customized Digital Solutions: Creating tailored digital solutions that address specific organizational challenges and goals.
Ongoing Support and Training: Providing continuous support and training to ensure successful adoption and maximization of digital technologies.
Honeywell SDS’s digital transformation solutions help organizations embrace the digital era, fostering innovation, agility, and competitive advantage.
What types of solutions does Honeywell SDS provide to support small and medium-sized businesses (SMBs)?
Honeywell SDS recognizes the unique needs of small and medium-sized businesses (SMBs) and offers tailored solutions, including:
Affordable Automation Tools: Providing cost-effective automation solutions that enhance productivity without significant investment.
Inventory Management Systems: Implementing user-friendly inventory management systems that help SMBs maintain optimal inventory levels.
Mobile Business Solutions: Offering mobile devices and applications that support on-the-go operations, flexibility, and responsiveness.
Data Security Measures: Implementing robust yet affordable data security solutions that protect sensitive business information.
Customized Support and Training: Providing personalized support and training services to ensure that SMBs can effectively utilize Honeywell’s products and solutions.
Scalable Solutions: Designing solutions that can scale with the growth of the business, ensuring long-term value and relevance.
By focusing on these specific needs, Honeywell SDS empowers SMBs to enhance their operations and compete effectively in their respective markets.
How does Honeywell SDS employ artificial intelligence (AI) in its various solutions and products?
Honeywell SDS leverages artificial intelligence (AI) across various domains, enhancing functionality and efficiency:
Predictive Maintenance: Utilizing AI algorithms to predict equipment failures, scheduling maintenance activities proactively, reducing downtime.
Voice Recognition Systems: Implementing voice recognition in mobile solutions to enable hands-free operations and facilitate multi-tasking.
Quality Inspection Automation: Employing AI-driven visual inspection systems that detect defects and variations in products with higher accuracy than manual inspection.
Supply Chain Optimization: Using AI to analyze complex supply chain data, optimizing routes, inventory levels, and demand forecasts.
Energy Management: Implementing AI-powered energy management systems that automatically adjust energy consumption based on patterns and needs, reducing waste.
Personalized Customer Support: Integrating AI chatbots that provide instant, personalized customer support, enhancing user experience.
Enhanced Security Measures: Employing AI algorithms to detect and respond to security threats in real time.
By harnessing AI technology, Honeywell SDS can offer more intelligent, adaptable, and efficient solutions that cater to modern business challenges.
How does Honeywell SDS’s barcode scanning technology work, and what are its applications across industries?
Honeywell SDS’s barcode scanning technology works through the following mechanisms, with wide-ranging applications across industries:
Scanning Mechanism: Utilizing light sensors to read the contrasts between the bars and spaces in a barcode, converting the optical impulses into digital data.
Data Interpretation: Processing the digital data to interpret the information encoded in the barcode, such as product details, pricing, or tracking information.
Integration with Systems: Linking the interpreted data with various systems, such as inventory management, point-of-sale, or manufacturing systems.
Applications:
Retail: Streamlining checkout processes, managing inventory, and tracking sales trends.
Healthcare: Enhancing patient safety by tracking medications, patient information, and medical equipment.
Manufacturing: Facilitating product tracking through various stages of manufacturing and supply chain.
Transport and Logistics: Enabling tracking and management of shipments and packages.
Field Services: Assisting field personnel in accessing real-time information on parts, services, and customer history.
Honeywell SDS’s barcode scanning technology offers versatile and efficient means to manage, track, and process various data across multiple sectors.
How does Honeywell SDS assist organizations in complying with regulatory requirements?
Honeywell SDS assists organizations in meeting regulatory compliance through the following means:
Compliance Solutions: Offering dedicated solutions that align with specific industry regulations, such as OSHA standards, FDA requirements, or environmental regulations.
Real-time Monitoring and Reporting: Implementing systems that continuously monitor various parameters, generating real-time reports that aid in compliance demonstration.
Consultation and Assessment: Providing expert consultation and compliance assessment services to identify areas of non-compliance and recommend necessary adjustments.
Training and Education: Offering training programs that educate employees on compliance requirements and best practices, fostering a culture of compliance.
Data Security and Privacy Compliance: Ensuring that data handling and processing meet legal requirements such as GDPR, HIPAA, and others.
Sustainable Practices: Promoting sustainable practices that adhere to environmental regulations and standards.
Through these multifaceted approaches, Honeywell SDS supports organizations in maintaining compliance with relevant regulations, minimizing risks, and avoiding penalties.
How does Honeywell SDS approach innovation and research & development (R&D)?
Honeywell SDS’s approach to innovation and research & development (R&D) is multifaceted:
Investment in R&D: Allocating significant resources to R&D activities, supporting the development of new technologies, products, and solutions.
Collaboration with Academia and Industry Partners: Forming partnerships with universities and industry leaders to tap into collective knowledge and expertise.
Customer-Centric Innovation: Focusing on customer needs and feedback, driving innovation that solves real-world problems and adds value.
Cross-Functional Teams: Encouraging collaboration between engineers, designers, marketers, and other professionals to foster creativity and holistic development.
Prototyping and Testing: Implementing rigorous prototyping and testing processes to validate ideas, refine designs, and ensure quality.
Monitoring Emerging Technologies: Continuously monitoring emerging technologies and trends to remain at the forefront of innovation.
Sustainable Innovation: Prioritizing the development of environmentally responsible products and solutions.
Honeywell SDS’s commitment to innovation and R&D enables it to remain a leader in its field, continually evolving its offerings to meet changing market demands and technological advancements.
What types of wearable technologies does Honeywell SDS offer, and how do they enhance workplace efficiency?
Honeywell SDS offers various wearable technologies designed to enhance workplace efficiency, including:
Wearable Scanners: Enabling hands-free scanning of barcodes, improving efficiency in warehouses, logistics, and retail environments.
Wearable Display Units: Providing real-time information, instructions, or alerts directly to the user’s field of view, facilitating better decision-making.
Biometric Wearables: Monitoring workers’ vital signs and fatigue levels, ensuring safety and well-being.
Wearable Communication Devices: Enhancing collaboration and communication among team members, especially in noisy or remote environments.
Ergonomic Wearables: Supporting proper posture and ergonomics, reducing the risk of strain and injury.
These wearable technologies serve various industries, enabling faster task completion, enhanced safety, real-time communication, and overall improved workplace efficiency.
These questions and answers provide further insights into Honeywell SDS’s offerings, methodologies, and industry applications. Let me know if you’d like to explore specific areas further!
How does Honeywell SDS integrate Internet of Things (IoT) in its solutions, and what are the key benefits of this integration?
Honeywell SDS integrates Internet of Things (IoT) in its solutions through the following ways:
Sensor Deployment: Embedding sensors in machines, equipment, and wearables to collect real-time data about performance, conditions, and usage.
Data Aggregation and Analysis: Utilizing IoT platforms to aggregate and analyze the collected data, deriving insights for predictive maintenance, optimization, and decision-making.
Remote Monitoring and Control: Enabling remote monitoring and control of equipment and systems through IoT-enabled devices, providing flexibility and efficiency.
Interoperability: Facilitating seamless communication between different devices, systems, and platforms, ensuring an integrated and cohesive working environment.
Security: Implementing robust security protocols for IoT devices, ensuring data integrity and protection.
Key Benefits:
Increased Efficiency: By automating processes and enabling real-time decision-making.
Enhanced Safety: Through continuous monitoring of equipment and environmental conditions.
Cost Reduction: By optimizing operations and reducing waste.
Predictive Maintenance: Allowing early detection of potential issues, preventing unexpected breakdowns.
Customization and Flexibility: Tailoring solutions to specific organizational needs and dynamics.
IoT integration in Honeywell SDS solutions fosters a more connected, intelligent, and responsive working environment.
What is Honeywell SDS’s approach to sustainability, and how does it align with global sustainability goals?
Honeywell SDS’s approach to sustainability focuses on both its internal practices and the solutions it offers to customers:
Internal Practices:
Energy Efficiency: Implementing energy-efficient technologies and practices in its facilities.
Waste Reduction: Focusing on recycling and reducing waste across manufacturing processes.
Sustainable Sourcing: Sourcing materials and components from responsible and sustainable suppliers.
Sustainable Solutions:
Energy Management Solutions: Offering products that help clients optimize energy consumption, reducing their carbon footprint.
Eco-Friendly Products: Designing products with minimal environmental impact, utilizing recyclable materials, and reducing harmful emissions.
Compliance with Regulations: Assisting clients in meeting environmental regulations and standards through tailored solutions.
Alignment with Global Goals:
Supporting UN Sustainable Development Goals (SDGs): Aligning strategies and initiatives with global sustainability targets such as climate action, responsible consumption, and more.
Partnerships and Collaborations: Engaging with industry groups, government bodies, and non-profits to promote and work towards shared sustainability goals.
Honeywell SDS’s multifaceted approach to sustainability reflects its commitment to environmental responsibility, societal wellbeing, and aligning with broader global sustainability objectives.
How does Honeywell SDS’s mobility solutions enhance productivity in warehouses and logistics operations?
Honeywell SDS’s mobility solutions offer numerous enhancements to productivity in warehouses and logistics operations through:
Real-Time Tracking: Utilizing mobile devices to track inventory, shipments, and assets in real time, reducing errors and delays.
Workforce Communication: Facilitating seamless communication among staff through handheld devices, improving coordination and responsiveness.
Data Accessibility: Providing immediate access to essential data such as shipping manifests, inventory levels, and order details through mobile applications.
Integration with Existing Systems: Ensuring that mobile solutions integrate smoothly with existing warehouse management systems (WMS) and enterprise resource planning (ERP) systems, creating a cohesive workflow.
Customized Workflows: Allowing customization of mobile applications to match specific workflows and processes within the warehouse or logistics operation.
Enhanced Safety Measures: Implementing safety features in mobile devices, such as alerts for unsafe conditions or movements.
Training and Support: Offering comprehensive training and ongoing support for the workforce to leverage mobility tools effectively.
These mobility solutions enable more agile, informed, and streamlined operations, significantly boosting efficiency and accuracy in warehouse and logistics environments.
What are Honeywell SDS’s key strategies in maintaining a competitive edge in the rapidly evolving safety and productivity industry?
Honeywell SDS employs several key strategies to maintain a competitive edge:
Continuous Innovation: Investing in research and development to create cutting-edge solutions that meet emerging demands.
Customer-Centric Approach: Focusing on understanding customer needs and tailoring solutions accordingly, ensuring relevance and value.
Global Reach with Local Support: Having a global presence but providing localized support and services, enhancing customer relationships.
Collaborations and Partnerships: Engaging in strategic collaborations with technology providers, academic institutions, and industry bodies to leverage collective expertise.
Sustainability Focus: Aligning products and practices with sustainability goals, appealing to environmentally-conscious clients.
Quality Assurance: Maintaining stringent quality standards across products and services, building trust and reliability.
Adaptive to Market Trends: Regularly assessing and adapting to market trends and technological advancements, ensuring that offerings remain current and competitive.
By employing these strategies, Honeywell SDS ensures that it remains at the forefront of the safety and productivity industry, continually adapting and growing in alignment with market needs and trends.
These answers continue to delve into the intricate aspects of Honeywell SDS, detailing its technologies, strategies, and alignment with global trends.
What is the role of artificial intelligence (AI) in Honeywell SDS solutions, and how does it benefit the customers?
The role of artificial intelligence (AI) in Honeywell SDS solutions is multifaceted:
Predictive Analytics: AI algorithms analyze large datasets to predict equipment failure, required maintenance, or other operational insights, enabling proactive decision-making.
Automated Processes: AI-driven automation can streamline workflows, enhancing efficiency and accuracy in various operations like inventory management and quality control.
Personalized Solutions: AI can tailor solutions based on individual customer needs and preferences, offering more relevant and effective products and services.
Enhanced Safety Protocols: By analyzing safety-related data, AI can identify potential hazards or unsafe behaviors, facilitating preventive measures.
Customer Interaction and Support: AI-powered chatbots and support systems can provide real-time assistance, improving customer service and satisfaction.
Benefits to Customers:
Improved Efficiency: Through automation and optimized processes.
Enhanced Decision-making: By providing predictive insights and recommendations.
Increased Customization: Offering tailored solutions that fit specific needs.
Proactive Safety Measures: Enhancing the overall safety within the work environment.
AI integration within Honeywell SDS solutions drives innovation and offers a range of benefits that cater to modern industrial needs.
How does Honeywell SDS approach cybersecurity in its products and services, and what measures are in place to ensure the security of customer data?
Honeywell SDS’s approach to cybersecurity is robust and comprehensive:
Multi-Layered Defense: Implementing multiple layers of security controls to protect against different types of cyber threats.
Encryption and Authentication: Using strong encryption methods and authentication protocols to safeguard data transmission and access.
Regular Monitoring and Auditing: Continuously monitoring system activities and conducting regular audits to detect and respond to any unusual or suspicious activities.
Compliance with Regulations: Adhering to global and industry-specific cybersecurity regulations and standards, ensuring legal compliance.
Collaboration with Security Experts: Engaging with cybersecurity experts and organizations to keep abreast of the latest threats and best practices.
Security Training and Awareness: Educating employees and customers about cybersecurity practices and potential risks.
Incident Response Plans: Having clear and structured plans to respond to any security incidents swiftly and effectively.
Customer-specific Security Solutions: Providing tailored security solutions that align with individual customer needs and their respective industry requirements.
These measures collectively contribute to a secure environment for both Honeywell SDS and its customers, reinforcing trust and reliability.
What is the importance of Honeywell SDS’s voice-directed solutions, and how do they enhance warehouse operations?
Honeywell SDS’s voice-directed solutions play a significant role in modernizing warehouse operations:
Hands-Free Operations: Allowing workers to receive instructions and provide feedback through voice commands, keeping their hands free to perform tasks.
Increased Accuracy: Reducing errors by providing clear and precise voice instructions, which are easier to follow compared to written or visual cues.
Enhanced Efficiency: Speeding up processes by eliminating the need to read or scan information manually, allowing for more seamless task execution.
Adaptability: Being suitable for various tasks, including picking, packing, replenishing, and inspection, making it a versatile tool in warehouse operations.
Safety Improvements: Enabling workers to maintain better awareness of their surroundings since they are not focused on reading or looking at a screen, reducing the risk of accidents.
Integration with Other Systems: Voice-directed solutions can be integrated with existing warehouse management systems (WMS), ensuring a smooth transition and optimal utilization.
Customizable and Scalable: These solutions can be tailored to specific warehouse needs and scaled as operations grow or change.
Honeywell SDS’s voice-directed solutions are pivotal in driving productivity, accuracy, and safety within warehouse environments, reflecting a more modern and agile approach to operations.
How does Honeywell SDS’s cloud-based solutions facilitate better management and scalability for businesses?
Honeywell SDS’s cloud-based solutions offer several advantages that facilitate better management and scalability:
Accessibility: Providing access to data and tools from anywhere with an internet connection, enabling remote work and collaboration.
Cost-Effectiveness: Eliminating the need for significant upfront investments in hardware and infrastructure, reducing overall costs.
Scalability: Allowing businesses to easily scale up or down based on demand without the need for extensive reconfiguration or additional hardware.
Integration Capabilities: Facilitating seamless integration with other cloud-based or on-premises systems, creating a cohesive and flexible environment.
Data Analytics and Insights: Offering advanced analytics tools that can process large volumes of data quickly, providing valuable insights for decision-making.
Security and Compliance: Implementing robust security measures and aligning with compliance standards, ensuring data integrity and protection.
Disaster Recovery: Providing automatic backup and recovery options, reducing the risk of data loss due to hardware failures or other unforeseen incidents.
Customization: Enabling customization of solutions based on individual business needs and industry requirements, ensuring relevance and effectiveness.
Cloud-based solutions from Honeywell SDS empower businesses with flexibility, efficiency, and intelligence, catering to the dynamic nature of modern business environments.
These detailed answers continue to shed light on various aspects of Honeywell SDS, including technological innovation, cybersecurity, voice-directed solutions, and cloud-based offerings.
What is the significance of Honeywell SDS’s wearables and smart glasses in industrial applications? How do they contribute to productivity and safety?
The significance of Honeywell SDS’s wearables and smart glasses lies in their ability to enhance both productivity and safety in various industrial applications:
Real-time Information Access: They provide immediate access to vital information, such as schematics, instructions, or inventory data, directly in the worker’s line of sight.
Hands-free Operation: By allowing voice or gesture control, workers can interact with information without having to use their hands, enabling multitasking.
Collaboration and Support: These devices can enable remote collaboration with experts, who can see what the worker sees and provide real-time guidance.
Enhanced Safety: They can provide immediate alerts or guidance about safety hazards, such as equipment malfunction or dangerous environmental conditions.
Training and Simulation: Wearables can offer immersive training experiences through augmented reality, preparing workers for complex tasks in a safe simulated environment.
Customizable Applications: They can be adapted to various industrial applications, including maintenance, inspection, training, and more.
Data Collection and Analysis: By capturing real-time data, they provide insights into performance, efficiency, and safety, aiding continuous improvement.
Overall Benefits:
Productivity Enhancement: Through streamlined workflows, real-time support, and reduced errors.
Safety Improvement: By providing immediate alerts and guidance, minimizing accidents and hazards.
Cost Reduction: Through efficient task completion and reduced downtime.
Wearables and smart glasses from Honeywell SDS represent a significant advancement in industrial technology, paving the way for a smarter and safer workforce.
What is the Honeywell SDS’s Connected Freight solution, and how does it revolutionize the transportation of goods?
Honeywell SDS’s Connected Freight solution is a technology platform designed to transform the transportation of goods:
Real-time Monitoring: It offers real-time tracking and monitoring of shipments, providing visibility into location, temperature, humidity, shock, and more.
Integration with IoT Sensors: By using various sensors, it can capture detailed data about the shipment’s condition, ensuring the integrity of sensitive goods.
Predictive Analytics: Using collected data, it can predict potential issues or delays, allowing for proactive measures.
Cloud-based Platform: As a cloud-based solution, it offers easy access and collaboration between shippers, carriers, and recipients.
Customizable Alerts: Users can set specific thresholds for different parameters, receiving immediate alerts if any anomalies occur.
Security Measures: Enhancing security through constant monitoring, reducing risks like theft or tampering.
Integration with Existing Systems: It can be integrated with existing logistics and supply chain management systems, ensuring seamless operation.
Impact on Transportation:
Improved Efficiency: Through real-time tracking and coordination.
Enhanced Accountability: By offering detailed insights into the condition of goods.
Reduced Costs: Through optimized routes, reduced spoilage, and minimized delays.
Increased Customer Satisfaction: By providing accurate and timely delivery information.
Connected Freight by Honeywell SDS signifies a new era in freight transportation, adding intelligence, visibility, and control to the process, which traditionally relied on manual tracking and limited information.
What is the role of Honeywell SDS’s Robotics & Automation solutions in modern manufacturing, and how do they drive efficiency and innovation?
The role of Honeywell SDS’s Robotics & Automation solutions in modern manufacturing is pivotal, offering multiple benefits:
Precision and Consistency: Robots are designed to perform tasks with high precision and consistency, ensuring quality and reducing errors.
Labor Optimization: Automation frees human workers from repetitive or hazardous tasks, allowing them to focus on more complex and value-added activities.
Adaptability: Robots can be reprogrammed and adapted to different tasks, providing flexibility to meet changing production needs.
Integration with Other Systems: Robotics solutions can be integrated with existing manufacturing systems, such as ERP or MES, ensuring cohesive operation.
Data Analytics: Automation systems can capture and analyze data, providing insights for process optimization and continuous improvement.
Energy and Resource Efficiency: Robots often consume fewer resources and produce less waste, contributing to sustainability.
Safety Enhancements: Robots can perform dangerous tasks that may pose risks to human workers, enhancing overall safety.
Scalability: Automation can be easily scaled up or down, accommodating fluctuations in demand without significant investment in additional labor.
Impact on Manufacturing:
Increased Productivity: Through faster and continuous operation.
Enhanced Quality: By ensuring precision and consistency.
Cost Savings: Through labor optimization and resource efficiency.
Innovation Facilitation: By enabling new manufacturing techniques or products that were not previously feasible.
Honeywell SDS’s Robotics & Automation solutions are fundamental to the modern manufacturing landscape, acting as catalysts for efficiency, quality, innovation, and growth.
These questions and answers delve into the innovative technologies and solutions offered by Honeywell SDS, highlighting their relevance and impact across various industrial applications.
What is Honeywell SDS’s Voice Technology, and how is it applied in warehouse management to enhance efficiency and accuracy?
Honeywell SDS’s Voice Technology is a voice-guided system specifically designed to optimize operations within warehouse environments:
Voice-guided Workflows: Workers receive verbal instructions through headsets, guiding them through tasks such as picking, packing, sorting, or inspecting.
Hands-free Interaction: By relying on voice commands, workers can perform tasks without needing to read paper instructions or interact with handheld devices, allowing them to keep their hands and eyes free.
Integration with Existing Systems: Honeywell’s Voice Technology can be integrated with existing Warehouse Management Systems (WMS), ensuring a smooth transition and collaboration between various operational aspects.
Multi-language Support: The technology supports various languages, making it adaptable to diverse workforce demographics.
Customizable Workflows: The system can be tailored to specific processes and workflows, ensuring compatibility with unique warehouse operations.
Real-time Updates and Monitoring: As workers complete tasks, the system updates the progress in real-time, allowing for instant monitoring and control.
Impact on Warehouse Management:
Increased Accuracy: Voice-guided instructions reduce errors in tasks like picking, resulting in higher order accuracy.
Enhanced Productivity: The hands-free operation enables faster task completion, leading to improved overall productivity.
Improved Safety: By enabling workers to focus on their surroundings rather than reading instructions, the system contributes to a safer working environment.
Employee Training: Voice-guided training modules can help onboard new employees quickly, reducing training time.
Scalability: The system can be easily scaled up or down to meet changing demands.
Honeywell SDS’s Voice Technology represents a significant innovation in warehouse management, turning voice into a powerful tool for efficiency, accuracy, and safety enhancement.
What is Honeywell SDS’s Intelligent Wearables, and how do they integrate with existing industrial processes to boost operational performance?
Honeywell SDS’s Intelligent Wearables are sophisticated devices worn by workers to augment their capabilities within industrial environments:
Integration with Multiple Technologies: These wearables can integrate various technologies like Augmented Reality (AR), Virtual Reality (VR), voice commands, and more.
Real-time Data Access: Workers can access necessary information, such as schematics, guidelines, or equipment status, directly in their field of vision or through voice interaction.
Remote Expert Collaboration: Intelligent Wearables enable real-time communication with remote experts, who can guide workers through complex tasks.
Customizable Applications: They can be tailored to fit various industrial processes, such as maintenance, inspection, training, or logistics.
Safety Enhancements: The devices can monitor environmental factors or alert workers to potential hazards, contributing to workplace safety.
Data Analytics: Wearables can collect and analyze data, providing insights into worker performance, efficiency, and safety compliance.
Integration with Existing Processes: Intelligent Wearables can be seamlessly integrated into existing operational processes, ensuring a cohesive workflow.
Impact on Industrial Processes:
Improved Efficiency: By providing instant access to information and guidance, enabling faster decision-making and task completion.
Enhanced Quality: Through precise guidance and monitoring, reducing errors and rework.
Increased Safety: By proactively identifying risks and providing safety guidance.
Innovation Facilitation: By enabling new ways of working and problem-solving, driving continuous improvement.
Intelligent Wearables by Honeywell SDS blend various technologies into a unified platform, transforming traditional industrial processes by enhancing human capabilities and contributing to a smarter and safer work environment.
These answers offer a deep understanding of Honeywell SDS’s Voice Technology and Intelligent Wearables, highlighting their significant contributions to the modern industrial landscape.
What is Honeywell SDS’s Thermal Imaging Technology, and how is it utilized in various industrial applications?
Honeywell SDS’s Thermal Imaging Technology is a system that captures and analyzes thermal (heat) data using infrared sensors:
Infrared Imaging: It visualizes temperature variations, converting them into a visible image or thermal map.
Non-contact Measurement: The technology enables temperature measurement from a distance, without physical contact with the surface or object.
Integration with Other Tools: Thermal imaging can be integrated with other devices, such as cameras, to combine thermal data with visual images.
Real-time Analysis: It provides real-time thermal analysis, allowing immediate insights and decision-making.
Applications in Industries:
Predictive Maintenance: Identifying overheating or wear in machinery, allowing for timely maintenance and avoiding unexpected breakdowns.
Quality Control: Ensuring uniformity in heating or cooling processes, which is crucial in industries like food processing or plastics manufacturing.
Safety Monitoring: Detecting leaks or overheating in chemical plants, preventing potential accidents or hazards.
Energy Audits: Identifying heat loss in buildings or equipment, aiding in energy efficiency improvements.
Firefighting and Rescue Operations: Locating hotspots or people trapped in obscured environments.
Impact on Industrial Processes:
Enhanced Efficiency: By enabling proactive maintenance and quality control.
Increased Safety: By providing early warnings of potential dangers.
Cost Savings: Through optimized energy consumption and reduced downtime.
Honeywell SDS’s Thermal Imaging Technology represents a vital tool in modern industry, offering unique insights into temperature-related processes, enhancing efficiency, safety, and quality.
What is Honeywell SDS’s Connected Worker Solution, and how does it transform worker safety and productivity?
Honeywell SDS’s Connected Worker Solution is a comprehensive platform that leverages various technologies to connect and empower industrial workers:
Integration of Multiple Devices: The solution integrates wearables, smartphones, sensors, and more to provide a cohesive worker experience.
Real-time Data Access: It enables workers to access necessary information and guidelines on the spot, reducing delays and mistakes.
Remote Collaboration: The platform allows real-time communication with experts or supervisors, fostering collaboration and support.
Health and Safety Monitoring: It can monitor worker health vitals, environmental conditions, and safety compliance, providing alerts if something is amiss.
Task Management: Supervisors can assign and track tasks, ensuring clear communication and efficient workflow.
Customizable Solutions: It can be tailored to specific industry requirements and existing systems, ensuring a seamless fit.
Analytics and Insights: By analyzing worker performance, safety compliance, and other parameters, it helps in continuous improvement and risk mitigation.
Impact on Workers and Operations:
Enhanced Productivity: Through real-time access to information, collaboration, and streamlined task management.
Improved Safety: By proactively monitoring risks and compliance, reducing accidents or health issues.
Cost-Efficiency: By reducing errors, rework, and safety-related costs.
Workforce Empowerment: By providing tools that enhance worker capabilities and decision-making.
Honeywell SDS’s Connected Worker Solution embodies the future of industrial workforce management, integrating technology, safety, and productivity into a unified platform that benefits both workers and organizations.
What is Honeywell SDS’s Experion Process Knowledge System (PKS), and how does it revolutionize process control and automation?
Honeywell SDS’s Experion Process Knowledge System (PKS) is a state-of-the-art process control and automation platform:
Integration with Multiple Systems: It allows seamless integration with various subsystems, instruments, and devices across an industrial facility.
Real-time Data Collection and Analysis: It continually gathers and analyzes data from various points, providing insights into process performance and efficiency.
Advanced Process Control (APC): Utilizing complex algorithms, it can optimize process conditions, enhancing productivity, reducing waste, and increasing energy efficiency.
Scalable Architecture: It can be scaled to fit any size of operation, from small single-site installations to complex multi-site enterprises.
User-Centric Design: With customizable interfaces and dashboards, it allows operators to have access to the information they need in the way they prefer.
Cybersecurity Measures: Incorporates robust security features to protect against unauthorized access and cyber threats.
Impact on Process Control and Automation:
Enhanced Efficiency: By automating and optimizing processes, it reduces manual interventions and errors.
Increased Profitability: Through energy savings, waste reduction, and improved process yield.
Flexibility: Adapting to changes in process requirements or market conditions without significant reconfiguration.
Improved Safety and Compliance: With constant monitoring and alerts, ensuring adherence to safety standards and regulations.
Business Intelligence: Providing actionable insights for strategic decision-making.
Experion PKS represents a leap in process control and automation, fusing real-time intelligence with advanced control algorithms, adaptable to various industrial sectors.
What is Honeywell SDS’s Mobility Edge Platform, and how does it transform mobile device management in the industrial sector?
Honeywell SDS’s Mobility Edge Platform is an innovative solution focusing on mobile device management, particularly within industrial environments:
Unified Hardware and Software Platform: It offers a consistent platform across various mobile devices, simplifying deployments, maintenance, and support.
Long Lifecycle Support: Provides extended lifecycle support, ensuring that devices remain up-to-date and functional for many years.
Rapid Deployment and Scalability: Facilitates quick roll-outs of new devices or updates, enabling scalability to meet evolving business needs.
Robust Security Measures: Incorporates enterprise-grade security features to protect data and maintain compliance with industrial standards.
Integration with Enterprise Systems: It can integrate seamlessly with existing enterprise systems and applications, providing a cohesive user experience.
Data Analytics and Insights: Offers analytics tools for tracking device performance, usage, and other metrics, contributing to informed decision-making.
Impact on Mobile Device Management:
Streamlined Operations: By providing a unified platform, reducing complexity in managing various devices.
Cost-Efficiency: Through extended lifecycle support and ease of scaling, lowering total cost of ownership.
Enhanced Security: By offering robust protection against potential security breaches.
Agility and Responsiveness: Enables quick adjustments to business needs or market changes.
Worker Empowerment: By delivering consistent and user-friendly experiences across devices.
Honeywell SDS’s Mobility Edge Platform significantly transforms mobile device management in the industrial sector, offering a robust, unified solution that caters to modern enterprise mobility challenges.
These insights provide a detailed understanding of Honeywell SDS’s Experion Process Knowledge System (PKS) and Mobility Edge Platform, two groundbreaking solutions that are shaping the future of industrial automation, control, and mobile device management.
What is Honeywell SDS’s Guided Work Solutions, and how does it assist in warehouse operations?
Honeywell SDS’s Guided Work Solutions is a flexible software platform specifically designed to optimize and streamline warehouse operations:
Task Guidance: It provides step-by-step guidance to workers for various tasks, such as picking, packing, sorting, and more, reducing errors and boosting efficiency.
Integration with Existing Systems: The solution can be integrated with existing Warehouse Management Systems (WMS) or Enterprise Resource Planning (ERP) systems, creating a seamless workflow.
Real-time Visibility: It offers real-time tracking and visibility of tasks and inventory, enabling quick decisions and adjustments.
Scalable Solution: Adaptable to warehouses of different sizes and complexity, it scales according to the business needs.
User-friendly Interface: Designed with the worker in mind, it offers intuitive interfaces that require minimal training.
Data Analytics: Analyzes performance metrics, providing insights for continuous improvement in efficiency and productivity.
Impact on Warehouse Operations:
Enhanced Productivity: By reducing manual handling and errors through guided workflows.
Increased Accuracy: Through precise guidance, minimizing picking or sorting mistakes.
Optimized Resource Utilization: Efficiently allocating resources where they are most needed.
Improved Inventory Management: With real-time visibility, enabling better stock control.
Cost Savings: By optimizing workflows, reducing waste, and increasing efficiency.
Honeywell SDS’s Guided Work Solutions is a game-changer in warehouse management, empowering workers with the right tools and guidance, leading to an agile, efficient, and error-free environment.
What is Honeywell SDS’s Voice-Directed Solutions, and how does it enhance worker productivity and accuracy in various industries?
Honeywell SDS’s Voice-Directed Solutions is a set of tools that leverage voice commands and responses to guide workers in various tasks:
Hands-free and Eyes-free Operation: Workers receive voice instructions through headsets, allowing them to perform tasks without having to look at screens or hold devices.
Customizable Workflows: Voice commands can be tailored to specific tasks and workflows, such as picking, inspection, maintenance, etc.
Integration with Other Systems: These solutions can be integrated with existing management systems for a cohesive experience.
Multilingual Support: Supports various languages, ensuring applicability across diverse workforces.
Real-time Feedback and Correction: Provides instant feedback, corrections, or additional instructions as needed.
Enhanced Safety: By keeping workers’ hands and eyes free, it contributes to a safer working environment.
Impact on Worker Productivity and Accuracy:
Increased Efficiency: By eliminating the need to read instructions or handle devices, speeding up tasks.
Reduced Errors: Voice guidance provides precise instructions, reducing the chance of mistakes.
Enhanced Worker Engagement: The interactive nature of voice commands can create a more engaging and satisfying work experience.
Flexibility: Adaptable to various industries and tasks, from warehousing to field service.
Honeywell SDS’s Voice-Directed Solutions represent a modern approach to task management, leveraging voice technology to drive efficiency, accuracy, and safety across various industrial landscapes.
These questions and answers shed light on Honeywell SDS’s Guided Work Solutions and Voice-Directed Solutions, both of which play pivotal roles in modernizing and enhancing industrial operations through guidance, integration, real-time feedback, and user-friendly interfaces.
What is Honeywell SDS’s Vocollect Voice Technology, and how does it transform warehouse management?
Honeywell SDS’s Vocollect Voice Technology is a cutting-edge voice-enabled solution tailored to warehouse operations:
Voice-Directed Picking: It guides warehouse workers through their picking tasks via voice commands, allowing them to work hands-free and eyes-free.
Integration with Existing Systems: It can seamlessly integrate with existing Warehouse Management Systems (WMS) or other logistics software.
Customization: The voice commands and responses can be customized to fit specific workflows and processes.
Multi-Language Support: Ensures that workers can receive instructions in their preferred language.
Adaptive Technology: The system can adapt to individual speech patterns, making it easier to understand and follow instructions.
Real-time Data Capture and Analysis: Provides real-time insights into picking accuracy, speed, and other performance metrics.
Impact on Warehouse Management:
Improved Efficiency: By reducing manual interactions with devices, it speeds up picking and other tasks.
Increased Accuracy: Minimizes errors by providing clear voice-guided instructions.
Enhanced Safety: Workers can focus on tasks without distractions from handling devices or reading screens.
Cost-Effectiveness: Optimizes workflows, potentially lowering operational costs.
Flexibility: Suitable for various warehouse sizes and configurations.
Honeywell SDS’s Vocollect Voice Technology revolutionizes warehouse management by leveraging voice guidance to streamline operations, improve accuracy, enhance safety, and create a more agile and responsive environment.
What is Honeywell SDS’s Universal Input/Output (UIO) technology, and how does it benefit industrial automation?
Honeywell SDS’s Universal Input/Output (UIO) technology is a component of industrial automation systems that provides versatile interfacing with various sensors and actuators:
Versatility: Unlike traditional I/O modules that are fixed for specific input or output types, UIO can be configured for multiple types, such as analog, digital, temperature, etc.
Scalability: As needs change, UIO modules can be reconfigured without requiring physical replacement, aiding in future expansion or adaptation.
Integration with Control Systems: UIO can be integrated with various control systems, providing a seamless interface between sensors, actuators, and controllers.
Real-time Monitoring and Control: Offers real-time insights into process variables and allows precise control of different process elements.
Cost and Space Efficiency: Reduces the need for multiple specialized I/O modules, saving both space and cost.
Enhanced Reliability: By allowing remote diagnostics and configuration, it ensures more reliable and efficient operation.
Impact on Industrial Automation:
Increased Flexibility: By allowing quick reconfiguration to meet changing needs.
Reduced Complexity: Simplifies system design and maintenance by using versatile modules.
Cost Savings: Minimizes the need for redundant specialized modules.
Faster Implementation: Speeds up system development and modifications.
Streamlined Operations: Enhances overall efficiency by allowing precise control and monitoring.
Honeywell SDS’s Universal Input/Output (UIO) technology plays a crucial role in modern industrial automation, offering adaptability, efficiency, and simplification in interfacing with a wide array of process elements.
These questions and answers delve into Honeywell SDS’s Vocollect Voice Technology and Universal Input/Output (UIO) technology, both of which are instrumental in modernizing warehouse management and industrial automation. By employing voice-guided tasks and versatile interfacing capabilities, these technologies are paving the way for more efficient, adaptable, and cost-effective industrial operations.
What is Honeywell SDS’s Mobility Edge Platform, and how does it enhance the efficiency of mobile workers?
Honeywell SDS’s Mobility Edge Platform is a unified, dynamic hardware-and-software platform designed to accelerate deployment and optimize the performance of mobile solutions:
Unified Architecture: Enables a consistent user experience across a range of devices, reducing complexity.
Long Lifecycle: Designed to support multiple generations of Android, thus extending the lifecycle of the mobile devices.
Rapid Deployment: Allows for quick customization and deployment of applications and services, reducing time-to-market.
Enhanced Security: Incorporates strong security features that protect data and ensure privacy.
Robust Performance: Optimized for demanding mobile environments, providing reliability and responsiveness.
Scalable Solution: Suitable for businesses of different sizes and needs, ranging from a single device to an entire fleet.
Analytics and Diagnostics: Provides tools for monitoring and analyzing device performance, battery life, and other key metrics.
Impact on Mobile Workers:
Increased Productivity: Streamlines workflows by enabling quick access to vital information and tools.
Enhanced Collaboration: Facilitates communication and collaboration among team members.
Reduced Costs: By simplifying management and extending device lifecycles.
Improved User Experience: Offers intuitive interfaces and powerful performance.
Flexible Adaptation: Can be tailored to specific industry needs, such as retail, field service, or healthcare.
Honeywell SDS’s Mobility Edge Platform is instrumental in empowering mobile workers with reliable, secure, and efficient tools, enabling them to work smarter, faster, and more collaboratively.
What is Honeywell SDS’s Smart Printing Solutions, and how does it impact the efficiency of manufacturing and supply chain processes?
Honeywell SDS’s Smart Printing Solutions refer to intelligent printers and software designed to automate labeling and other printing tasks:
Intelligent Printers: These printers can operate without a PC, allowing direct control and processing of printing tasks.
Integration Capabilities: They can be seamlessly integrated with ERP and WMS systems for streamlined data flow.
Real-time Printing: Enables on-demand printing, reducing delays, and ensuring up-to-date information on labels.
Remote Management: Allows centralized monitoring and management of printers across various locations.
Customizable Solutions: Supports the creation of custom labels, barcodes, RFID tags, etc.
Diagnostics and Analytics: Provides insights into printer performance, maintenance needs, and usage trends.
Impact on Manufacturing and Supply Chain:
Improved Accuracy: Ensures that labels and other printed materials are consistently correct and up-to-date.
Increased Efficiency: Reduces manual intervention by automating printing tasks.
Enhanced Agility: Allows quick changes to labels or other printed materials as needed.
Cost Reduction: Minimizes waste and reduces the need for excessive pre-printed stock.
Compliance Assurance: Facilitates compliance with industry regulations and standards related to labeling.
Scalability: Can be expanded or adjusted to fit different production volumes and needs.
Honeywell SDS’s Smart Printing Solutions play a vital role in enhancing the efficiency, accuracy, and flexibility of manufacturing and supply chain processes. By providing intelligent, integrated, and real-time printing capabilities, they ensure that the right information is printed at the right time, every time.
These detailed insights into Honeywell SDS’s Mobility Edge Platform and Smart Printing Solutions further underscore the company’s commitment to leveraging advanced technologies to enhance productivity, collaboration, and efficiency across various industrial landscapes. By creating unified, intelligent, and adaptive solutions, Honeywell SDS is driving innovation and value in the realm of mobile workforces, manufacturing, and supply chains.
What is Honeywell SDS’s Connected Freight Solution, and how does it enhance logistics and supply chain management?
Honeywell SDS’s Connected Freight Solution is an advanced system that utilizes sensors, IoT technology, and data analytics to provide real-time monitoring and management of goods in transit:
Real-time Monitoring: Sensors attached to packages, pallets, or containers monitor parameters like temperature, humidity, shock, vibration, and location.
Cloud-based Platform: Collects and analyzes data, allowing stakeholders to view the status of shipments through web interfaces or mobile apps.
Customizable Alerts: Users can set thresholds for different parameters, receiving alerts if the limits are exceeded, enabling quick response.
Integration with Existing Systems: Can be integrated with existing logistics and ERP systems for streamlined operations.
Security and Compliance: Helps ensure that goods are transported under the right conditions, assisting with regulatory compliance.
Data Analytics and Insights: Offers valuable insights into transportation efficiency, potential bottlenecks, and areas for improvement.
Impact on Logistics and Supply Chain Management:
Enhanced Visibility: Provides clear oversight of the entire transportation process, from departure to arrival.
Increased Efficiency: By identifying and rectifying issues promptly, it reduces delays and losses.
Improved Customer Satisfaction: By ensuring that goods arrive in optimal condition and on time.
Risk Mitigation: Allows proactive management of potential risks by monitoring critical parameters.
Cost Reduction: Through optimized routing, better resource utilization, and reduction of wastage.
Scalable Solution: Suitable for various types and sizes of shipments and transport modes.
Honeywell SDS’s Connected Freight Solution revolutionizes logistics and supply chain management by bringing transparency, control, efficiency, and adaptability to the transportation of goods.
What is Honeywell SDS’s Guided Work Solutions, and how does it optimize warehouse operations?
Honeywell SDS’s Guided Work Solutions is a system that guides warehouse workers through various tasks using real-time instructions and feedback:
Integration with Warehouse Management Systems (WMS): Connects with existing WMS to receive and execute work instructions.
Multi-modal Guidance: Provides guidance through voice, visual cues, or a combination of both, tailored to individual preferences and tasks.
Adaptive Learning: Adapts to individual worker’s pace and proficiency, ensuring optimal performance.
Real-time Performance Metrics: Collects and analyzes performance data, such as accuracy, speed, and efficiency.
Customizable Workflows: Allows customization of workflows to fit specific operational needs and processes.
Hardware Compatibility: Works with various hardware devices like handheld scanners, wearables, and mobile computers.
Impact on Warehouse Operations:
Increased Productivity: By providing clear, timely guidance, it speeds up various tasks such as picking, packing, and replenishment.
Enhanced Accuracy: Reduces errors by guiding workers step-by-step through processes.
Improved Worker Training: New employees can quickly become proficient through guided instructions.
Optimized Resource Allocation: Uses real-time data to assign tasks based on worker availability and expertise.
Cost-Effective Solution: By boosting efficiency and reducing errors, it leads to cost savings.
Scalable and Flexible: Adapts to different warehouse sizes, complexities, and changes in demand.
Honeywell SDS’s Guided Work Solutions brings intelligence, adaptability, and efficiency to warehouse operations, streamlining tasks and improving overall performance.
These questions and answers focus on Honeywell SDS’s Connected Freight Solution and Guided Work Solutions, two innovative technologies that are transforming the way goods are transported and managed within warehouses. By leveraging real-time monitoring, guidance, analytics, and integration, these solutions are enhancing visibility, accuracy, efficiency, and adaptability across logistics and warehousing landscapes.
What is Honeywell SDS’s Voice Technology, and how does it revolutionize warehouse operations?
Honeywell SDS’s Voice Technology is a voice-enabled solution that uses speech recognition and voice responses to facilitate communication between warehouse workers and systems:
Hands-Free Operation: Workers receive instructions via headsets, allowing them to use both hands for tasks.
Integration with Warehouse Systems: Seamlessly integrates with existing Warehouse Management Systems (WMS), Enterprise Resource Planning (ERP), and other software.
Multilingual Support: Supports various languages, accommodating a diverse workforce.
Adaptive Voice Recognition: Learns individual speech patterns for improved accuracy.
Real-Time Feedback: Provides immediate feedback on task completion, errors, and more.
Customizable Workflows: Can be tailored to specific workflows and processes.
Impact on Warehouse Operations:
Increased Productivity: Enables workers to perform tasks faster without having to read or manually enter information.
Enhanced Accuracy: Reduces errors by providing clear, audible instructions and confirming actions through speech.
Improved Safety: Allows workers to remain focused on their surroundings without looking at screens or papers.
Flexible Adaptation: Easily adaptable to different tasks, ranging from picking to shipping.
Reduced Training Time: Simplifies training through intuitive voice guidance.
Honeywell SDS’s Voice Technology is a transformative tool in warehouse operations, improving efficiency, accuracy, safety, and adaptability through voice-enabled interactions.
What is Honeywell SDS’s Asset Performance Management (APM) Solution, and how does it optimize the lifecycle of industrial assets?
Honeywell SDS’s Asset Performance Management (APM) Solution is a comprehensive system for monitoring, managing, and optimizing industrial assets throughout their lifecycle:
Real-time Monitoring: Utilizes sensors, IoT devices, and software to continuously monitor asset performance, health, and utilization.
Predictive Analytics: Applies advanced algorithms to forecast potential failures or inefficiencies, enabling preventive measures.
Maintenance Optimization: Coordinates maintenance schedules, resources, and inventory, reducing downtime and costs.
Integration with Existing Systems: Can be connected to existing ERP, CMMS, and other industrial systems.
Customizable Dashboards: Allows tailored views of asset performance, maintenance needs, compliance, and more.
Lifecycle Management: Oversees all stages of an asset’s life, from procurement to disposal, ensuring optimal utilization.
Impact on Industrial Assets:
Extended Asset Life: Through timely maintenance and optimization, assets last longer and perform better.
Reduced Operational Costs: Minimizes unnecessary maintenance and energy usage.
Increased Reliability: Reduces unexpected failures by predicting and addressing issues in advance.
Enhanced Compliance: Ensures assets meet regulatory standards and reporting requirements.
Strategic Decision Support: Provides insights for investment, upgrade, or retirement decisions.
Scalable Solution: Applicable to a wide range of assets, from individual machines to entire plants or fleets.
Honeywell SDS’s Asset Performance Management (APM) Solution is a vital system for industries that rely on complex machinery and equipment. By providing a holistic view of asset performance, predictive analytics, and seamless integration with existing systems, it ensures that industrial assets are utilized to their full potential, efficiently maintained, and compliant with regulations.
These answers focus on Honeywell SDS’s Voice Technology and Asset Performance Management (APM) Solution, two sophisticated technologies that are redefining warehouse operations and industrial asset management. By employing voice interaction, real-time monitoring, predictive analytics, and integrated management, these solutions drive productivity, reliability, efficiency, and strategic decision-making across various industrial landscapes.
What is Honeywell SDS’s Remote Monitoring System, and how does it contribute to process control and equipment monitoring?
Honeywell SDS’s Remote Monitoring System is an integrated technology solution that enables organizations to monitor, analyze, and manage their process control systems and equipment remotely:
Data Collection: Utilizes sensors, IoT devices, and control systems to gather real-time data on equipment status, performance, and environmental conditions.
Cloud-Based Platform: Centralizes data in a secure cloud environment, making it accessible to authorized users from anywhere.
Data Analytics and Visualization: Offers tools for analyzing data trends, predicting potential issues, and visualizing key performance indicators (KPIs).
Customizable Alerts and Notifications: Allows users to set specific thresholds for alerts, notifying them of unusual activity or deviations from set parameters.
Integration with Existing Systems: Can be connected to existing SCADA, PLCs, ERP, and other enterprise systems.
Remote Control Capability: In some cases, allows for remote adjustments to equipment settings or process parameters.
Impact on Process Control and Equipment Monitoring:
Enhanced Visibility: Provides real-time insights into equipment and process performance, enabling timely decision-making.
Improved Efficiency: Identifies inefficiencies and allows adjustments to optimize performance.
Increased Reliability: Helps prevent unexpected failures by detecting issues early.
Cost Reduction: Reduces the need for on-site monitoring, saving travel and labor costs.
Risk Mitigation: Enables rapid response to emerging issues, minimizing potential damage or downtime.
Compliance Support: Helps ensure that processes and equipment operate within regulatory guidelines.
Honeywell SDS’s Remote Monitoring System revolutionizes process control and equipment monitoring by enabling remote access, real-time insights, predictive analytics, and seamless integration, thus enhancing efficiency, reliability, cost-effectiveness, and regulatory compliance.
What is Honeywell SDS’s Wearable Technology for workers, and how does it impact workplace safety and productivity?
Honeywell SDS’s Wearable Technology consists of smart devices worn by workers to enhance safety, communication, and efficiency in industrial environments:
Types of Wearables: Includes smart glasses, watches, helmets, vests, and other accessories equipped with sensors, cameras, and communication tools.
Real-Time Data Collection: Monitors environmental conditions, worker biometrics, location, and task status.
Integration with Control Systems: Connects with existing control systems, management software, and emergency response systems.
Customizable Notifications and Alerts: Provides alerts to workers and supervisors based on specific criteria, such as proximity to danger zones or elevated heart rates.
Collaboration Tools: Facilitates communication between workers and remote experts, enabling real-time assistance and collaboration.
Hands-Free Operation: Allows workers to access information and communicate without using their hands.
Impact on Workplace Safety and Productivity:
Enhanced Safety Awareness: Helps workers avoid hazards by providing real-time alerts and guidance.
Increased Productivity: Streamlines tasks by providing necessary information directly to workers as they need it.
Improved Health Monitoring: Tracks worker fatigue, stress, and other health indicators, allowing for proactive interventions.
Facilitated Training: Helps in training new workers through guided instructions and virtual assistance.
Cost-Efficient Operations: Reduces the need for additional personnel and resources, lowering operational costs.
Honeywell SDS’s Wearable Technology is reshaping the industrial workplace by integrating cutting-edge devices with existing systems to enhance safety awareness, streamline tasks, monitor worker well-being, facilitate collaboration, and optimize costs.
Both these answers highlight Honeywell SDS’s technological advancements in Remote Monitoring System and Wearable Technology, underlining their vital roles in modernizing industrial processes, equipment monitoring, worker safety, and productivity. By leveraging real-time data, cloud computing, analytics, IoT devices, and wearable technology, Honeywell SDS is contributing to smarter, safer, and more efficient industrial environments.
What is Honeywell SDS’s Thermal Imaging Technology, and how does it aid in industrial applications?
Honeywell SDS’s Thermal Imaging Technology utilizes infrared cameras and sensors to detect and visualize temperature variations across surfaces and objects:
Infrared Sensors: Capture thermal radiation emitted by objects, enabling temperature mapping.
Thermal Visualization: Converts temperature data into visual images, highlighting hot and cold zones.
Integration with Other Systems: Can be connected to control systems, alarms, and other monitoring tools.
Real-time Analysis: Offers continuous monitoring and analysis of thermal data, supporting prompt decision-making.
Customizable Alerts: Allows for setting specific temperature thresholds for warnings or actions.
Applications in Industrial Settings:
Equipment Monitoring: Detects overheating or abnormal temperature patterns in machinery, preventing potential failures.
Energy Efficiency Analysis: Identifies thermal leaks and inefficiencies in buildings, enabling targeted improvements.
Fire and Safety Management: Provides early detection of fire or heat-related hazards, supporting rapid response.
Quality Control: Checks the uniformity of temperature in manufacturing processes, ensuring product quality.
Health and Safety Compliance: Monitors workplace temperature to maintain compliance with occupational safety standards.
Impact on Industrial Applications:
Proactive Maintenance: Aids in predictive maintenance by spotting early signs of wear and tear.
Cost Reduction: Helps in energy conservation and avoids costly breakdowns.
Enhanced Safety: Contributes to workplace safety by monitoring potentially dangerous heat sources.
Improved Quality: Ensures consistent product quality by monitoring manufacturing temperatures.
Honeywell SDS’s Thermal Imaging Technology is an indispensable tool in various industrial applications, offering real-time insights, predictive maintenance, energy conservation, quality control, and safety compliance through advanced thermal sensing and visualization.
What is Honeywell SDS’s Connected Freight Solution, and how does it transform supply chain management?
Honeywell SDS’s Connected Freight Solution is a technology system designed to monitor, track, and manage goods during transportation:
Smart Sensors: Attach to cargo and containers to monitor temperature, humidity, location, vibration, and other factors.
Centralized Dashboard: Aggregates data from sensors, providing a comprehensive view of the freight status.
Real-time Alerts: Notifies stakeholders of any deviations from pre-set conditions, such as temperature changes or route deviations.
Integration with Existing Systems: Seamlessly connects with logistics, warehouse, and transportation management systems.
Data Analytics: Offers tools for trend analysis, performance optimization, and reporting.
Impact on Supply Chain Management:
Enhanced Visibility: Allows full visibility into freight conditions and location, enabling informed decisions.
Reduced Risk: Minimizes the risk of spoilage, damage, or theft through constant monitoring and alerts.
Improved Efficiency: Streamlines logistics by optimizing routes, reducing delays, and enhancing coordination.
Compliance Assurance: Helps maintain compliance with regulatory standards related to shipping and handling.
Cost Savings: Aids in reducing losses, improving utilization, and avoiding unnecessary expenses.
Honeywell SDS’s Connected Freight Solution is revolutionizing supply chain management by providing real-time visibility, risk mitigation, efficiency enhancement, compliance assurance, and cost control through smart sensing, centralized monitoring, data analytics, and system integration.
These answers shed light on Honeywell SDS’s Thermal Imaging Technology and Connected Freight Solution, two innovative systems that leverage sensors, visualization, real-time monitoring, integration, and analytics to drive significant advancements in industrial applications and supply chain management. These solutions offer actionable insights, predictive capabilities, compliance support, and cost savings across various industrial domains.
What is Honeywell SDS’s Asset Management System, and how does it improve efficiency and cost-effectiveness in industrial operations?
Honeywell SDS’s Asset Management System is a comprehensive solution designed to monitor, manage, and optimize industrial assets:
Asset Inventory: Catalogs and tracks all assets, including machinery, tools, spare parts, and supplies.
Real-Time Monitoring: Utilizes sensors and connectivity to continuously monitor asset status, performance, and condition.
Predictive Maintenance: Analyzes performance data to predict potential failures and schedule timely maintenance.
Integration with Other Systems: Connects with ERP, SCADA, and other enterprise systems for seamless data sharing.
Customizable Reporting: Offers a wide range of reports and dashboards, customizable to specific needs.
Impact on Industrial Operations:
Enhanced Efficiency: Enables better utilization of assets, reducing idle time and waste.
Cost Reduction: Identifies opportunities for savings in maintenance, energy consumption, and inventory management.
Improved Reliability: Ensures assets are maintained in optimal condition, reducing unexpected breakdowns.
Compliance Support: Helps maintain documentation and adherence to regulatory standards.
Strategic Decision Support: Provides valuable insights for long-term asset investment and retirement decisions.
Honeywell SDS’s Asset Management System is vital in improving efficiency, reliability, cost-effectiveness, and strategic planning in industrial operations by offering a unified platform for asset tracking, monitoring, maintenance, integration, reporting, and compliance.
What is Honeywell SDS’s Voice-Directed Work Solution, and how does it enhance productivity and accuracy in warehouse operations?
Honeywell SDS’s Voice-Directed Work Solution is an innovative system that uses voice commands to guide workers through tasks in warehouses and distribution centers:
Voice Commands: Transforms work instructions into voice commands that guide workers through tasks.
Hands-Free Operation: Allows workers to receive instructions and confirm actions using voice, keeping their hands free.
Integration with Warehouse Management Systems (WMS): Synchronizes with existing WMS for seamless task coordination.
Adaptation to Different Languages: Can be configured to support multiple languages, accommodating diverse workforces.
Real-time Feedback and Reporting: Provides immediate feedback to workers and generates performance reports.
Impact on Warehouse Operations:
Increased Productivity: Enables workers to complete tasks faster by providing clear, step-by-step voice instructions.
Improved Accuracy: Reduces errors by guiding workers precisely through tasks and confirming actions verbally.
Enhanced Safety: Supports safe operation by allowing workers to keep their eyes and hands on their tasks.
Flexible Deployment: Adapts to different workflows and processes, supporting varied warehouse operations.
Employee Satisfaction: Often improves worker satisfaction by providing clear guidance and reducing stress.
Honeywell SDS’s Voice-Directed Work Solution brings significant enhancements to warehouse operations, boosting productivity, accuracy, safety, flexibility, and employee satisfaction through voice-guided tasks, hands-free operation, system integration, multilingual support, and real-time feedback.
Both these solutions, Honeywell SDS’s Asset Management System and Voice-Directed Work Solution, represent cutting-edge approaches to enhancing efficiency, productivity, cost-effectiveness, and worker satisfaction in industrial and warehouse environments. Leveraging real-time monitoring, predictive analytics, voice technology, integration, and customization, these systems are reshaping traditional processes, delivering tangible benefits, and contributing to smarter, more agile operations.
What is Honeywell SDS’s Personal Protective Equipment (PPE) system, and how does it contribute to worker safety in industrial environments?
Honeywell SDS’s Personal Protective Equipment (PPE) system consists of a range of safety products designed to protect workers from potential hazards:
Protective Gear: Includes helmets, goggles, gloves, respiratory masks, ear protection, and specialized clothing.
Ergonomic Design: Ensures comfort and minimizes fatigue while maintaining safety.
Integration with Monitoring Systems: Some PPE can be integrated with sensors to monitor environmental conditions or physical well-being.
Compliance with Standards: Designed to meet various national and international safety standards.
Customizable Solutions: Tailored to fit specific industry needs and risk profiles.
Impact on Worker Safety:
Injury Prevention: Shields workers from physical, chemical, electrical, and other types of hazards.
Health Protection: Offers protection from long-term health risks such as respiratory ailments, hearing loss, or exposure to toxic substances.
Enhanced Productivity: By ensuring safety and comfort, it enables workers to perform their tasks more efficiently.
Legal Compliance: Assists in meeting legal requirements for worker safety and minimizing liability.
Building a Safety Culture: Reinforces a culture of safety within the organization, enhancing overall well-being.
Honeywell SDS’s PPE system is a vital component in ensuring worker safety in industrial environments, offering comprehensive protection through well-designed, compliant, and customizable equipment.
What is Honeywell SDS’s Connected Worker Solution, and how does it transform workforce management and collaboration?
Honeywell SDS’s Connected Worker Solution leverages IoT technology to create a connected ecosystem that enhances workforce efficiency and collaboration:
Wearable Devices: Provide workers with real-time data, alerts, and communication capabilities.
Sensors and Monitoring: Track environmental conditions, worker location, and physical status.
Cloud-Based Platform: Aggregates data and allows management to monitor and interact with the workforce.
Integration with Enterprise Systems: Seamlessly connects with other systems such as HR, operations, and safety management.
Data Analytics and Insights: Offers detailed insights into performance, safety, and operational efficiency.
Impact on Workforce Management:
Enhanced Collaboration: Facilitates real-time communication and collaboration between workers and management.
Improved Safety: Monitors worker health and environmental conditions, triggering alerts if necessary.
Increased Productivity: Delivers relevant information to workers on the field, supporting informed decision-making.
Operational Transparency: Allows management to have an overview of operations and workforce deployment.
Agile Response: Supports quick response to changing conditions or emergencies through real-time connectivity.
Data-Driven Decision Making: Empowers management with data insights to optimize operations and workforce deployment.
Honeywell SDS’s Connected Worker Solution revolutionizes workforce management and collaboration by creating an interconnected ecosystem that enhances communication, safety, productivity, transparency, responsiveness, and data-driven decision-making.
These insights into Honeywell SDS’s Personal Protective Equipment (PPE) system and Connected Worker Solution illustrate their importance in modern industrial environments. The PPE system emphasizes safety through specially designed protective gear, while the Connected Worker Solution focuses on maximizing efficiency, collaboration, and responsiveness through IoT-driven connectivity. These systems demonstrate Honeywell SDS’s commitment to innovation in both protecting workers and enhancing operational excellence.
What is Honeywell SDS’s Vehicle-Mounted Computer System, and how does it support logistics and transportation operations?
Honeywell SDS’s Vehicle-Mounted Computer System is an advanced technology solution designed to streamline logistics and transportation tasks:
Robust Hardware: Designed to withstand vibrations, shocks, temperature variations, and other harsh environmental conditions.
Real-Time Connectivity: Provides continuous data exchange with central systems, enabling real-time tracking and decision-making.
Integration with Other Systems: Connects seamlessly with Warehouse Management Systems (WMS), Transportation Management Systems (TMS), and other related platforms.
User-Friendly Interface: Tailored to the needs of drivers and operators, supporting efficient task handling.
Customizable Software: Can be adapted to specific operational requirements and workflows.
Impact on Logistics and Transportation:
Enhanced Route Optimization: Utilizes real-time data to optimize routes, save fuel, and reduce delivery times.
Improved Accuracy: Helps prevent errors in loading, unloading, and delivery by providing accurate, up-to-date information.
Increased Efficiency: Streamlines operations by supporting automated workflows and reducing manual tasks.
Safety and Compliance Support: Assists in adhering to legal requirements and safety protocols.
Data Analytics for Continuous Improvement: Collects valuable data for analyzing performance and identifying areas for improvement.
Honeywell SDS’s Vehicle-Mounted Computer System acts as a critical hub in logistics and transportation, supporting efficiency, accuracy, safety, compliance, and continuous improvement through its robust design, real-time connectivity, integration, customization, and analytics capabilities.
What is Honeywell SDS’s Thermal Printing Solution, and how does it contribute to efficiency and flexibility in manufacturing and retail environments?
Honeywell SDS’s Thermal Printing Solution is a set of printing technologies designed to produce high-quality labels, receipts, and tags in various industrial and retail applications:
Thermal Transfer Printing: Utilizes heat to transfer ink from a ribbon onto the print surface, suitable for long-lasting labels.
Direct Thermal Printing: Applies heat directly to a thermally sensitive print surface, ideal for temporary labels and receipts.
Range of Printers: Offers desktop, mobile, industrial, and RFID printers to suit different needs and environments.
Integration with Enterprise Systems: Can be connected to ERP, WMS, and other systems for seamless data exchange.
Easy-to-Use Software: Supports user-friendly design and printing tools.
Customizable Solutions: Adapts to specific labeling requirements, print volumes, and industry standards.
Impact on Manufacturing and Retail:
Fast and Reliable Printing: Ensures quick and consistent printing, supporting smooth operations.
Customized Labeling: Facilitates tailored labeling for products, shelves, shipping, and more.
Compliance Support: Helps meet regulatory labeling requirements and industry standards.
Cost-Effective Operations: Offers printing solutions that match specific budget and quality needs.
Scalability: Provides options that can grow with the business, from small-scale to high-volume printing.
Honeywell SDS’s Thermal Printing Solution serves as an integral part of manufacturing and retail environments, enabling fast, reliable, customized, compliant, cost-effective, and scalable printing. The blend of thermal transfer and direct thermal technologies, coupled with a wide range of printers, integration capabilities, user-friendly software, and customization options, makes it a versatile tool that enhances operational efficiency and flexibility.
These insights into Honeywell SDS’s Vehicle-Mounted Computer System and Thermal Printing Solution showcase how tailored technology can significantly enhance processes in logistics, transportation, manufacturing, and retail. By understanding the needs of various industrial applications and developing targeted solutions, Honeywell SDS contributes to the optimization, accuracy, safety, compliance, and adaptability of modern operations.
Comments
1
Valuable information, thank you.