PLC Program for Welding Arm Robot Wire and Gas Consumption Calculation
In this article, we will learn the PLC program for welding arm robot wire and gas consumption in grams and in liters per second.
In this application, arm robots are used to perform Metal Inert Gas, or MIG, welding on an automotive part. Solid or flux-core welding wire, as well as a CO2 and argon gas combination, are used in this process.
Using a PLC, wire consumption in grams and gas consumption in liters per second have to be determined as required by the user. In this article, we will learn the PLC program for welding arm robots wire and gas consumption.
PLC Program for Welding Arm Robot
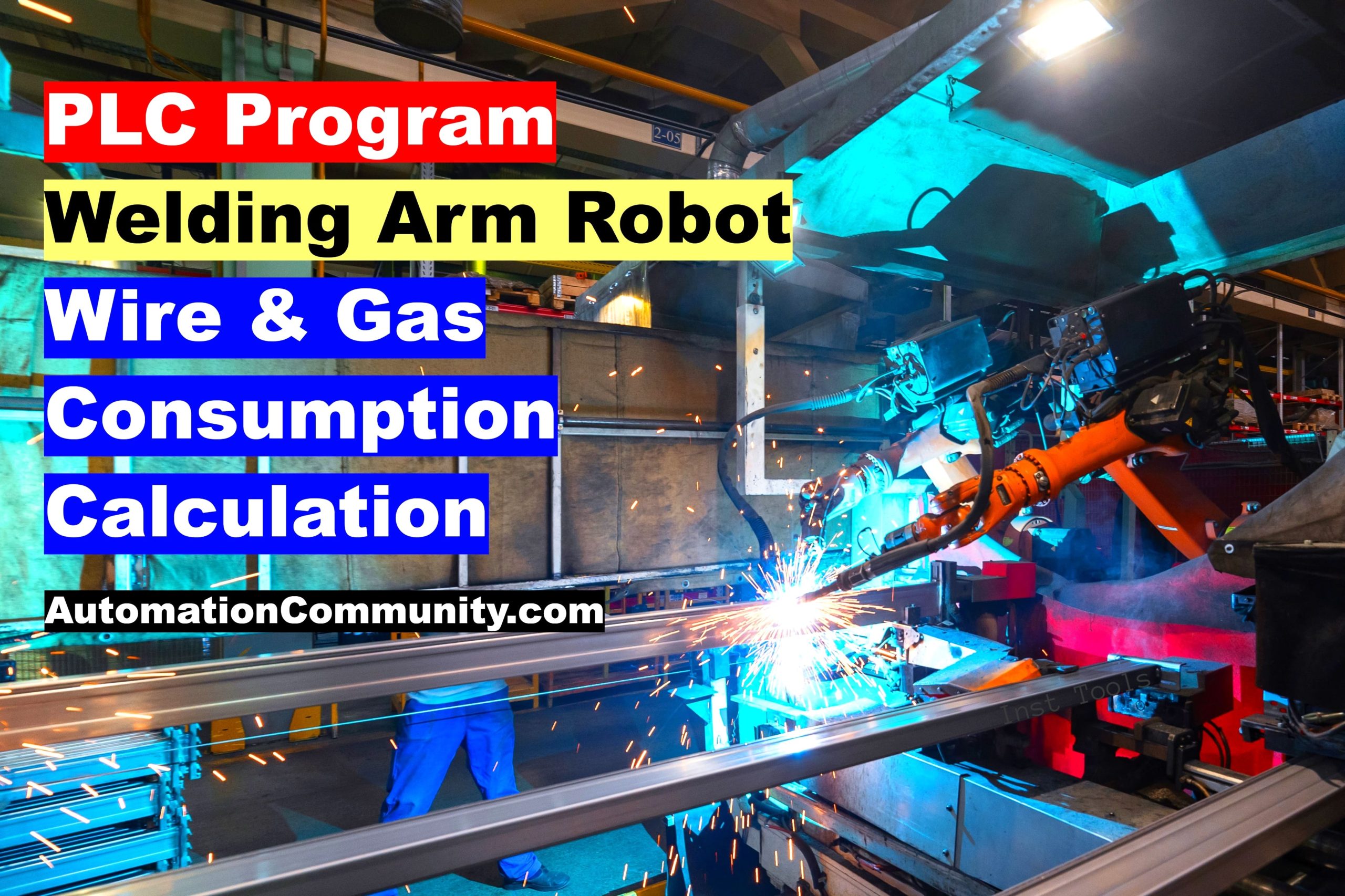
To do this, an encoder is installed inside the elbow joint section so that as the wire is drawn into the wire feeding tube, the encoder shaft rotates. Thus, the wire is measured using an encoder, and then its weight is calculated.
Through the Flow Transducer installed in the pipeline’s path, the gas is transported to the “Torch Travel” area.
Ladder Logic
The below program shows the PLC logic for the welding robot gas and wire consumption calculation part.
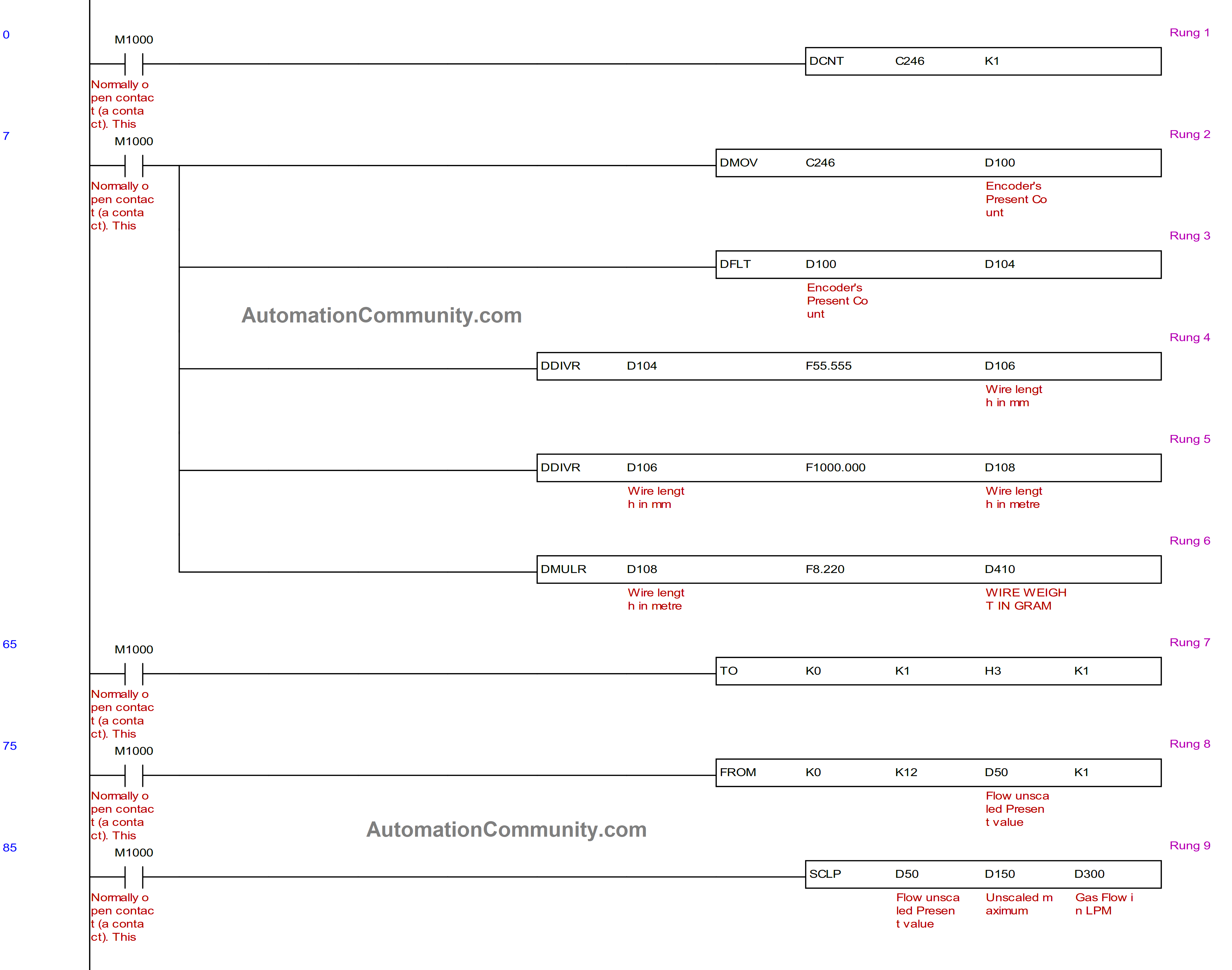
Rung 1
Encoder is set up using the PLC’s X0 and X1 inputs (which can only be used for encoders), and the high-speed counter’s counter no. 246 reads the encoder’s current count.
Rung 2 and 3
The current encoder count is initially recorded in D100 before being translated to float format and saved in D104.
Rung 4
Encoder produces a total of 5000 pulses per rotation. Each time the encoder turns by one revolution, it is physically measured that 90 mm of wire is taken out.
Applying the Unitary method, It takes around 55.55 pulses to draw out 1 mm.
The wire length in mm is then determined by dividing the pulses detected in D104 by 55.55. This data is stored in D106.
Rung 5
The total wire length calculated in millimeters is then converted into meters and stored in D108.
Rung 6
The weight of 1 mm of wire, as determined by physical measurement, is 8.22 grams. The total weight of the wire in grams is calculated using the unitary method by multiplying the whole wire length by 8.22. This weight is stored in D410.
Rung 7
A 4 to 20 mA signal from the flow transducer is received at one of the Analog input card’s Channels to calculate the gas flow rate.
The Analog Input Card’s input mode setting is defined by “TO K0 K1 H3 K1,” where H3 specifies that the first channel is set to mA signal mode.
Rung 8
The present decimal value on the first channel of the Analog Input module is read with the command “FROM K0 K12 D50 K1.” The value is stored in D50.
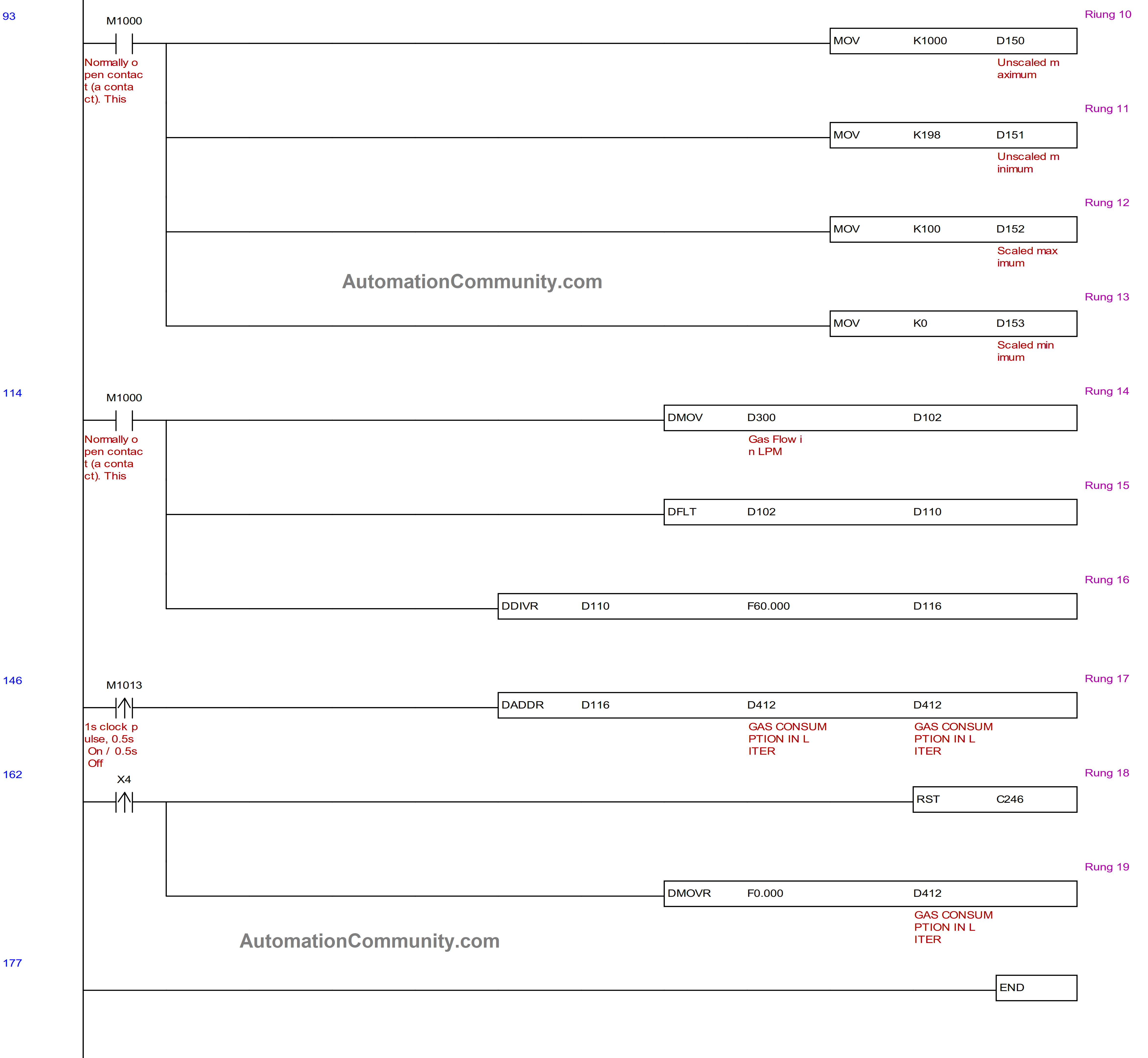
Rung 9, 10, 11, 12, and 13
The flow transducer shows the flow rate in liters per minute, ranging from 0 to 100. It generates a 4mA signal at 0 LPM and a 20mA signal at 100 LPM.
In this instance, the decimal value read at maximum flow is 1000, however, it is 198 at minimum or no flow. This value must be scaled into the appropriate unit, which is LPM.
D150 sets the maximum unscaled value, whereas D151 specifies the minimum unscaled value. D152 defines the maximum scale, whereas D153 defines the minimum scale.
Based on the constraints defined in D150 to D153, the SCLP instruction is used to produce the resulting scaled value in D300 with regard to the current unscaled decimal value read in D50. The unit of the value registered in D300 is liters per minute.
Rung 14, 15, and 16
D300’s value is transformed into float format and saved in D110.
The value is then divided by 60 to convert it to liters per second, and it is saved in D116.
Rung 17
Using an internal one-second clock pulse bit M1013, the value in D116 is then totaled in D412 once every second. Thus, D412 records total gas consumption in liters.
Rung 18, 19
The encoder counts and liters consumed are both reset to zero when the Reset button X4 is pushed.
Conclusion
To determine the weight of the wire and the number of liters used during welding, the encoder, and flow transducer are integrated with the welding robot.
Read Next:
Comments
1
Thanks. Please provide complete program