145 Control Valve Interview Questions and Answers
A control valve is a vital component used in process control systems to regulate the flow, pressure, level, or temperature of fluids in industrial applications. With the control valve’s ability to precisely control process variables, control valves play a crucial role in maintaining optimal performance, efficiency, and safety across various industries.
Control Valve Interview Questions
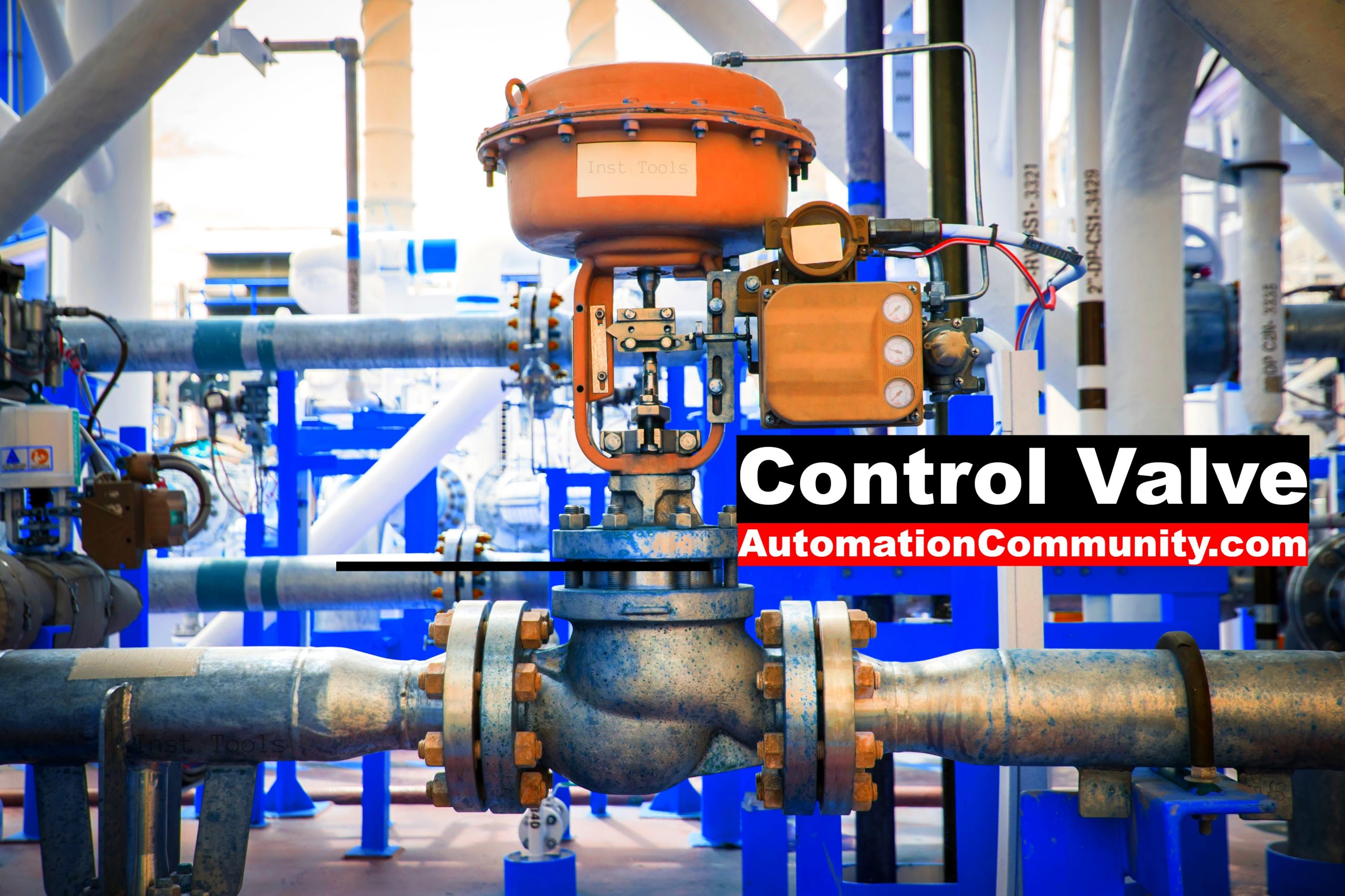
Prepare for your control valve interview with our questions and answers from fundamental concepts to advanced topics, this resource covers a wide range of control valve principles, types, applications, and troubleshooting. Boost your knowledge and impress interviewers with expert insights on control valve selection, operation, maintenance, and performance evaluation.
What is a control valve?
A control valve is a device that regulates the flow of a fluid, such as gas, liquid, or steam, by varying the size of the flow passage as directed by a signal from a controller.
What are the key components of a control valve?
The key components of a control valve are the valve body, the actuator, and the positioner.
Can you explain the function of a valve actuator?
A valve actuator is a component that physically moves the valve to open, close, or partially obstruct the flow path. It could be powered by air, electricity, or hydraulic fluid.
What is a control valve positioner?
A positioner is a device that ensures the control valve reaches the desired position accurately. It compares the actual position of the control valve with the control signal and makes the necessary adjustments.
Can you name different types of control valves?
Some types of control valves include globe valves, gate valves, butterfly valves, ball valves, diaphragm valves, and pinch valves.
What is the role of a control valve in process control?
In process control, control valves are used to maintain desired conditions, such as pressure, temperature, or flow rate, by manipulating the fluid flow in response to signals from a control system.
What are the two main types of control valve actuators?
The two main types of control valve actuators are rotary and linear actuators.
Can a control valve be manually operated?
Yes, a control valve can be manually operated, but in most industrial applications, they are automated for more precise and efficient control.
What is a fail-safe position for a control valve?
A fail-safe position is a position that a control valve will move to in the event of a power or control signal failure. It is typically either fully open or fully closed, depending on the specific application.
Can a control valve regulate multiple process variables at once?
No, a control valve typically regulates one process variable at a time, such as pressure, flow rate, or temperature.
What is the function of a valve body?
The valve body is the primary component of the control valve. It houses the internal parts of the valve, including the flow path and the seat for the closure member.
What does ‘Cv’ refer to in valve specifications?
Cv is a measure of the flow capacity of a valve. It represents the volume of fluid in US gallons per minute that can pass through the valve with a pressure drop of 1 psi at room temperature.
How does a solenoid valve differ from a control valve?
A solenoid valve is a type of control valve that uses an electromagnetic solenoid to operate the valve. It usually operates in an on/off manner, whereas most control valves can be adjusted to any position between fully open and fully closed.
What is a globe valve and where is it used?
A globe valve is a type of control valve with a spherical body and a movable disc-type element that modulates the flow. It’s often used in applications that require precise throttling and frequent operation.
What is the trim of a control valve?
The trim of a control valve refers to the internal parts that come into contact with the process fluid, including the stem, plug, and seat.
What factors should be considered when selecting a control valve?
Some factors to consider when selecting a control valve include the type of process fluid, the required flow rate, the operating pressure and temperature, the required level of control precision, and the need for fail-safe operation.
How does a ball valve work?
A ball valve works by rotating a ball with a hole drilled through the middle. When the hole is aligned with the flow, the valve is open; when the ball is rotated so that the hole is perpendicular to the flow, the valve is closed.
What is a butterfly valve and where is it used?
A butterfly valve is a control valve with a circular disc as the flow control element. By rotating the disc, flow can be started, stopped, or regulated. It’s often used in applications requiring low-pressure loss and a compact design.
What is a valve sizing calculation?
Valve sizing is a process of determining the suitable valve size for a specific application. It considers factors like flow rate, pressure drop, and the characteristics of the fluid to ensure the valve will operate efficiently and effectively.
How does a diaphragm valve function?
A diaphragm valve controls flow by using a flexible diaphragm that moves up and down to change the size of the flow path. It’s often used in applications requiring a sterile or clean operation.
What is a control valve’s rangeability?
Rangeability, also known as turndown, is the ratio of the maximum to the minimum controllable flow rate of a control valve. It is an indication of the control valve’s ability to regulate flow over a wide range.
What are smart control valves?
Smart control valves, also known as intelligent or digital control valves, are equipped with microprocessors and sensors to provide diagnostic information, self-calibration, and enhanced control performance.
How is a control valve calibrated?
Calibration of a control valve involves adjusting the valve so that its output accurately corresponds to the control signal. This usually involves comparing the valve’s actual position with the desired position and making necessary adjustments.
What does ‘normally open’ or ‘normally closed’ mean in control valve terminology?
‘Normally open’ or ‘normally closed’ refers to the default position of a control valve when there is no power or control signal applied. A normally open valve will default to an open position, allowing flow, while a normally closed valve will default to a closed position, blocking the flow.
What causes cavitation in control valves and how can it be prevented?
Cavitation in control valves is caused by a rapid drop and subsequent increase in pressure, causing the fluid to flash into vapor and then collapse back into liquid. It can be prevented by reducing the pressure drop across the valve, using a valve with an anti-cavitation trim, or by controlling the flow rate.
What is flashing in a control valve?
Flashing in a control valve is a condition where the pressure downstream of the valve drops below the vapor pressure of the fluid, causing some of the fluid to vaporize. This can lead to damage to the valve and piping system.
Can a control valve be used for both liquid and gas applications?
Yes, control valves can be used for both liquid and gas applications. However, the specific design and materials of the valve may differ depending on the type of fluid.
What is a control valve’s flow coefficient?
A control valve’s flow coefficient, often denoted as Cv or Kv, is a measure of the valve’s capacity to flow a fluid. It is defined as the flow rate in gallons per minute (or cubic meters per hour) that will create a pressure drop of one psi (or one bar) across the valve.
What are some common issues encountered with control valves?
Some common issues with control valves include leakage, stiction (where the valve sticks in place), wear and tear on the valve components, calibration issues, and problems with the actuator or positioner.
What is the purpose of a control valve packing gland?
The packing gland, or stuffing box, of a control valve, is designed to prevent process fluid from leaking out along the valve stem. It typically contains a packing material that can be compressed to form a tight seal.
Can a control valve operate without a positioner?
Yes, a control valve can operate without a positioner, but it might not provide the same level of control accuracy. A positioner ensures the valve accurately reaches the desired position.
What is a control valve stroke test?
A control valve stroke test is a diagnostic procedure used to check the performance of the valve. It involves moving the valve from fully closed to fully open and back again, while observing the response of the valve.
What is an equal percentage valve characteristic?
An equal percentage valve characteristic means that for each increment of valve opening, the flow rate increases by a constant percentage of the flow at the start of that increment. This characteristic provides good control in processes with large load changes.
What is a linear valve characteristic?
A linear valve characteristic means that the flow rate changes linearly with the valve opening. This characteristic provides good control in processes with small load changes.
What is a quick opening valve characteristic?
A quick opening valve characteristic means that a large change in flow rate occurs with a small initial change in valve opening. This characteristic is typically used in on-off applications.
What is the function of a control valve’s I/P converter?
An I/P (current to pressure) converter is a device that converts an electric signal (usually 4-20 mA) into a pneumatic signal (usually 3-15 psi) to operate the control valve actuator.
What is the difference between a direct-acting and a reverse-acting control valve?
A direct-acting control valve opens when the control signal increases, while a reverse-acting valve opens when the control signal decreases.
What is a split-range control valve arrangement?
A split-range control is a setup where two or more control valves share a single control signal, but each valve operates over a different portion of the control signal range. This allows for greater control flexibility.
What is hysteresis in a control valve?
Hysteresis in a control valve is a phenomenon where the valve’s position depends not only on the current control signal but also on its past positions. It can lead to inaccuracies in the control process.
What is the difference between a two-way and a three-way control valve?
A two-way control valve has two ports (an inlet and an outlet) and can either stop or allow flow. A three-way valve has three ports and can be used to switch between different sources or destinations of flow or to mix flows from two inlets.
Can control valves be used for both flow control and shut-off purposes?
Yes, many control valves are designed to provide both flow control and shut-off capability. However, some specialized control valves are designed for only one of these functions.
How is the leakage rate defined for control valves?
The leakage rate of a control valve is defined as the quantity of fluid that passes through the valve when it is in the closed position. It’s usually expressed as a percentage of the valve’s maximum flow capacity.
How does a pinch valve work?
A pinch valve controls flow by pinching a flexible tube (the valve body) with a mechanism (the actuator). It is well-suited for handling slurries, liquids with large amounts of suspended solids, and highly corrosive or abrasive materials.
How is the pressure drop across a control valve calculated?
The pressure drop across a control valve is calculated by subtracting the downstream pressure from the upstream pressure. This calculation is used in determining the valve’s flow capacity and its effect on the overall system performance.
What happens when a control valve is undersized?
An undersized control valve may not be able to handle the required flow rate, resulting in inadequate process control and potentially causing damage to the valve due to excessive velocity.
What happens when a control valve is oversized?
An oversized control valve can lead to poor control performance due to a lack of sensitivity at low flow rates. It can also lead to higher costs due to the unnecessary expense of a larger valve.
What is a control valve data sheet?
A control valve data sheet is a document that provides detailed information about a control valve’s specifications, including its type, size, materials, flow capacity, and other operational parameters.
How does temperature affect the performance of a control valve?
Temperature can affect the performance of a control valve by changing the properties of the fluid and the valve materials. High temperatures can cause thermal expansion, while low temperatures can cause materials to become brittle.
What is the role of a control valve in a PID controller?
In a PID controller, the control valve manipulates the process variable (e.g., flow rate, pressure, temperature) in response to the controller’s output signal. The valve’s position is adjusted to minimize the difference between the process variable and the setpoint.
How is the flow direction indicated on a control valve?
The flow direction on a control valve is usually indicated by an arrow on the valve body. It’s important to install the valve in the correct orientation to ensure proper operation.
What is a balanced control valve?
A balanced control valve is a valve design that minimizes the impact of differential pressure across the valve on the force needed to operate the valve. This is usually achieved by designing the valve so that the process pressure acts on equal and opposite areas.
What materials are commonly used to make control valves?
Common materials for control valves include carbon steel, stainless steel, bronze, and various types of plastic. The choice of material depends on the characteristics of the process fluid and the operating conditions.
What is an air-to-close control valve?
An air-to-close (or normally open) control valve is a valve that closes when air pressure is applied to the actuator. If the air supply fails, the valve will move to its fail-safe position, which is fully open.
What is an air-to-open control valve?
An air-to-open (or normally closed) control valve is a valve that opens when air pressure is applied to the actuator. If the air supply fails, the valve will move to its fail-safe position, which is fully closed.
What is a double-acting control valve actuator?
A double-acting control valve actuator uses air pressure to open and close the valve. It applies air pressure to one side of a piston to open the valve and applies pressure to the opposite side to close the valve.
What is a single-acting control valve actuator?
A single-acting control valve actuator uses air pressure to move the valve in one direction (either open or close), and a spring to move the valve in the opposite direction. This design provides a fail-safe position in case of air supply failure.
What is position feedback in a control valve?
Position feedback in a control valve is a signal provided by a position sensor that indicates the actual position of the valve. This feedback is used by the control system to verify that the valve has reached the desired position.
What is valve authority in a control system?
Valve authority is a measure of the impact of a control valve on the total system pressure drop. A high valve authority means that a large proportion of the total system pressure drop occurs across the control valve.
What is a valve characteristic curve?
A valve characteristic curve is a graph that shows how the flow rate through a valve changes with the valve opening. Different types of valves have different characteristic curves, which affect their control performance.
How can noise generation in control valves be minimized?
Noise generation in control valves can be minimized by selecting the appropriate valve size and type, using noise reduction trim, and controlling the fluid velocity and pressure drop across the valve.
What is stick-slip in control valves?
Stick-slip in control valves is a phenomenon where the valve moves in small, jerky steps instead of a smooth motion. This can be caused by friction in the valve stem or actuator, or by problems with the control signal.
What is a control valve’s dead band?
A control valve’s dead band is the range of control signal values within which the valve does not respond. It can be caused by factors like friction, hysteresis, and calibration errors, and it can degrade the control performance.
What are some signs that a control valve needs maintenance?
Signs that a control valve may need maintenance include an increase in leakage, erratic or inaccurate control, unusual noises, and an increase in the energy required to operate the valve.
How is the performance of a control valve evaluated?
The performance of a control valve can be evaluated in terms of its control accuracy, response speed, reliability, and longevity. This evaluation can involve tests like the stroke test, leakage test, and response time test.
What are some safety considerations when working with control valves?
Safety considerations when working with control valves include ensuring that the valve is not under pressure before maintenance, using appropriate personal protective equipment, and following lockout-tagout procedures to ensure that the valve cannot be accidentally operated.
What is a fail-fixed control valve?
A fail-fixed control valve is a valve that stays in its last position if the control signal or power supply fails. This is different from fail-open or fail-closed valves, which move to a specific position in the event of a failure.
What is a control valve plug?
A control valve plug, also known as a disc or a ball, is the part of the valve that moves to control the flow of fluid. The shape and material of the plug can affect the valve’s flow characteristic and its resistance to wear and corrosion.
What are some common types of actuators used in control valves?
Common types of actuators used in control valves include pneumatic actuators, hydraulic actuators, electric motor actuators, and solenoid actuators. The choice of the actuator depends on factors like the required control precision, response speed, and energy availability.
What is the function of a control valve bonnet?
The bonnet of a control valve is part of the valve body that houses the stem and the packing. It provides a seal to prevent process fluid from leaking out along the stem.
How can the life of a control valve be extended?
The life of a control valve can be extended by regular maintenance, correct sizing and selection for the application, protecting the valve from extreme operating conditions, and using appropriate materials for the process fluid.
How is a control valve’s set point defined?
A control valve’s set point is the desired value of the process variable that the valve is controlling. The control system adjusts the position of the valve to maintain the process variable at the set point.
What is the function of a control valve seat?
The seat of a control valve is the part of the valve where the plug makes contact to stop the flow of fluid. The material and design of the seat can affect the valve’s sealing performance and resistance to wear.
What is the difference between a control valve and a regulating valve?
A control valve is a valve that can be adjusted to any position to control the flow rate, while a regulating valve, or regulator, is typically used to maintain a constant downstream pressure or flow rate, regardless of changes in the upstream pressure or flow.
What is a control valve’s gain?
A control valve’s gain is the ratio of the change in flow rate to the change in the control signal. It is a measure of the sensitivity of the valve to changes in the control signal.
What is a pneumatic control valve?
A pneumatic control valve is a valve that is operated by a pneumatic actuator, which uses air pressure to move the valve plug. Pneumatic control valves are widely used in industrial control systems due to their reliability and compatibility with hazardous environments.
What is a hydraulic control valve?
A hydraulic control valve is a valve that is operated by a hydraulic actuator, which uses fluid pressure to move the valve plug. Hydraulic control valves can provide high force and precise control, but they require a hydraulic power supply.
What is an electric control valve?
An electric control valve is a valve that is operated by an electric motor or solenoid actuator. Electric control valves can offer precise control and easy integration with electronic control systems, but they may not be suitable for high-force or high-speed applications.
What is a modulating control valve?
A modulating control valve is a valve that can be adjusted to any position to accurately control the flow rate. It is used in applications that require precise control of process variables.
What is a globe control valve?
A globe control valve is a type of control valve that has a spherical body and a linear motion plug. It is widely used in control applications due to its good flow control characteristics and its ability to handle high-pressure drops.
What is a butterfly control valve?
A butterfly control valve is a type of control valve that uses a disc, or butterfly, that rotates in the flow path to control the flow rate. Butterfly valves are compact and economical, but they may not provide as precise control as some other valve types.
What is a ball control valve?
A ball control valve is a type of control valve that uses a ball with a hole through it, which can be rotated to control the flow rate. Ball valves provide good shut-off capability and are resistant to wear and corrosion, but their control characteristics can be nonlinear.
What is a diaphragm control valve?
A diaphragm control valve is a valve that uses a flexible diaphragm to control the flow rate. The diaphragm can be moved by a pneumatic or hydraulic actuator. Diaphragm valves are resistant to clogging and can handle corrosive or slurry fluids.
What is a gate control valve?
A gate control valve is a type of control valve that uses a gate, or wedge, that moves linearly in the flow path to control the flow rate. Gate valves are often used for on-off control, but they can also be used for modulating control in some applications.
What is cavitation in control valves?
Cavitation in control valves is a phenomenon where vapor bubbles form in the fluid due to a rapid drop in pressure, and then collapse when the pressure recovers. This can cause noise, vibration, and damage to the valve and piping.
What is flashing in control valves?
Flashing in control valves is a phenomenon where a liquid turns into a vapor due to a drop in pressure below its vapor pressure. Unlike cavitation, the vapor does not collapse back into a liquid, which can cause erosion and other problems.
What is a mixing control valve?
A mixing control valve is a valve that can combine flows from two or more inlets into a single outlet. This can be used for temperature control, pH control, and other applications.
What is a diverting control valve?
A diverting control valve is a valve that can direct the flow from a single inlet to one of two or more outlets. This can be used for switching between different process paths, or for safety purposes.
What is an angle control valve?
An angle control valve is a type of control valve where the inlet and outlet are at a 90-degree angle. This design can simplify piping arrangements, and it can also provide good resistance to cavitation and flashing.
What is a three-way control valve?
A three-way control valve is a valve that has three ports and can be used for mixing or diverting applications. It can combine flows from two inlets, or split a flow into two outlets.
What is a control valve trim?
The trim of a control valve is the set of internal parts that come into contact with the process fluid, including the plug, seat and stem. The material and design of the trim can affect the valve’s performance and durability.
What is a rotary control valve?
A rotary control valve is a type of control valve where the flow is controlled by rotating a part in the flow path. Examples of rotary control valves include ball valves, butterfly valves, and plug valves.
What is a linear control valve?
A linear control valve is a type of control valve where the flow is controlled by moving a part linearly in the flow path. Examples of linear control valves include globe valves, gate valves, and diaphragm valves.
What is a control valve’s hysteresis?
A control valve’s hysteresis is the difference between the valve positions for increasing and decreasing control signals, due to factors like friction and backlash. It can degrade the control accuracy.
What is an anti-cavitation control valve?
An anti-cavitation control valve is a valve that is designed to prevent cavitation by managing the pressure drop and fluid velocity, or by redirecting the cavitation bubbles to areas where they will not cause damage.
What are the common reasons for control valve failure?
Common reasons for control valve failure can include wear and corrosion of the valve components, improper installation, improper sizing or selection for the application, cavitation or flashing, and problems with the control signal or actuator.
What are some of the materials used in the construction of control valves?
Control valves can be constructed from a variety of materials including cast iron, stainless steel, and various types of plastic. The material used often depends on the nature of the fluid being controlled.
What is a top-guided control valve?
A top-guided control valve is a type of valve where the plug is guided by the bonnet or cage. This can provide good alignment and stability, especially for smaller valve sizes.
What is a bottom-guided control valve?
A bottom-guided control valve is a valve where the plug is guided by the seat or cage. This can provide good alignment and stability for larger valve sizes or high differential pressures.
What is a control valve cage?
A control valve cage is a component that surrounds the plug and can provide flow control and guiding functions. It often has ports or openings that align with the plug to control the flow rate.
What does it mean when a control valve is chattering?
Chattering in a control valve refers to rapid, small movements of the valve plug that can cause vibration and noise. It can be caused by factors like instability in the control loop, excessive dynamic forces, or mechanical problems in the valve or actuator.
What is an equal percentage control valve?
An equal percentage control valve is a valve with a flow characteristic where each increment of valve travel produces an equal percentage change in the flow rate. This can provide good control performance over a wide range of flows.
What is a quick-opening control valve?
A quick-opening control valve is a valve with a flow characteristic where a small change in valve travel produces a large change in flow rate. This is often used for on-off control or for applications that require a fast response.
What is a parabolic control valve?
A parabolic control valve is a valve with a parabolic plug shape that provides a linear flow characteristic. Each increment of valve travel produces an equal increment in flow rate.
How is a control valve selected for a specific application?
Control valve selection involves considering factors like the type of control required, the nature of the process fluid, the operating conditions, the valve material and construction, the flow characteristic, and the actuator type.
What is a flanged control valve?
A flanged control valve is a valve that has flanges for connecting to the piping. This can provide a secure and leak-tight connection, but it may require more space and effort to install than other types of connections.
What is a threaded control valve?
A threaded control valve is a valve that has threads for connecting to the piping. This can be a compact and economical option for small valve sizes and lower pressures.
What is a wafer-style control valve?
A wafer-style control valve is a valve that is installed between pipe flanges, without any threaded or flanged connection to the valve body. This can provide a compact and economical solution for certain applications.
What is an unbalanced control valve?
An unbalanced control valve is a valve where the pressure drop across the valve affects the force required to move the plug. While simpler and less expensive than balanced valves, unbalanced valves may require larger actuators and may have more hysteresis.
What is a high recovery control valve?
A high-recovery control valve is a valve that is designed to maximize the recovery of pressure downstream of the valve. This can reduce the risk of cavitation or flashing.
What is a low recovery control valve?
A low recovery control valve is a valve that is designed to minimize the recovery of pressure downstream of the valve. This can provide a larger pressure drop for flow control, but it may increase the risk of cavitation or flashing.
How can noise be reduced in control valves?
Noise in control valves can be reduced by using designs that minimize turbulence and cavitation, by using noise reduction trim, by isolating or insulating the valve and piping, and by selecting the correct size and type of valve for the application.
What is an air-to-close control valve?
An air-to-close control valve is a valve that uses air pressure to move the plug to the closed position. When the air pressure is removed, a spring or other force moves the plug to the open position. This is also known as a normally open valve.
What is an air-to-open control valve?
An air-to-open control valve is a valve that uses air pressure to move the plug to the open position. When the air pressure is removed, a spring or other force moves the plug to the closed position. This is also known as a normally closed valve.
What is a fail-safe control valve?
A fail-safe control valve is a valve that is designed to move to a safe position (either fully open or fully closed) if the control signal or power is lost. This can prevent uncontrolled flow or other unsafe conditions.
What is a split range control valve?
A split range control valve is one of two or more control valves that share a control signal, with each valve controlling a different range of the signal. This can be used to provide better control over a wide range of flow rates or conditions.
How is a control valve calibrated?
Control valve calibration involves adjusting the valve and the control system to ensure that the valve position accurately corresponds to the control signal. This can involve adjusting the actuator, positioner, and feedback devices, and checking the valve’s performance.
What is a pressure-independent control valve?
A pressure-independent control valve is a valve that maintains a constant flow rate regardless of changes in the pressure drop across the valve. This can improve control accuracy in systems with variable pressure conditions.
What is a cryogenic control valve?
A cryogenic control valve is a valve that is designed to handle extremely low-temperature fluids, such as liquid nitrogen or liquid helium. It often has special materials and design features to withstand low temperatures and prevent heat transfer.
What is a high-temperature control valve?
A high-temperature control valve is a valve that is designed to handle high-temperature fluids, such as steam or hot oil. It often has special materials and design features to withstand high temperatures and to prevent heat damage.
What is a self-operated control valve?
A self-operated control valve is a valve that controls the flow rate based on the pressure, temperature, or flow rate of the fluid itself, without the need for an external control signal or power source.
What is a multi-stage control valve?
A multi-stage control valve is a valve that controls the pressure drop in multiple stages to reduce the risk of cavitation or flashing. This can be achieved using a series of restrictions and expansions in the flow path.
How does a control valve affect the stability of a control loop?
The characteristics of a control valve can affect the stability of a control loop. Factors like valve gain, deadband, and hysteresis can influence the loop’s response to disturbances and its ability to maintain the setpoint.
What are the advantages and disadvantages of different types of control valve actuators?
Pneumatic actuators are simple, reliable, and capable of producing large forces, but they require a supply of compressed air. Hydraulic actuators can produce very large forces and have good speed and positioning control, but they require a hydraulic supply system and can be more complex. Electric actuators can be easily integrated with digital control systems and don’t require a fluid supply, but they can be slower and produce less force than pneumatic or hydraulic actuators.
How can leakage be prevented in control valves?
Leakage in control valves can be prevented by proper selection and maintenance of the valve and seal materials, correct installation and adjustment of the valve and packing, and periodic inspection and replacement of worn or damaged parts.
What are some safety considerations for control valves?
Safety considerations for control valves include selecting the correct valve and materials for the process conditions, using proper installation and operating procedures, providing appropriate pressure relief and containment measures, and implementing regular inspection and maintenance programs.
How can a control valve’s performance be monitored and diagnosed?
Control valve performance can be monitored and diagnosed by observing the valve’s operation and the process conditions, checking for signs of wear or damage, measuring the valve position and control signal, and using diagnostic tools or software that analyze the valve’s response and control characteristics.
How does a control valve’s size affect its performance?
The size of a control valve can affect its performance in terms of the flow capacity, pressure drop, and actuation force. An oversized valve can be difficult to control at low flow rates, while an undersized valve may not provide enough flow capacity or pressure drop for the application.
How does a control valve’s design affect its performance?
The design of a control valve can affect its performance in terms of flow characteristic, stability, noise, cavitation, and maintenance requirements. Different designs may be better suited for different applications or operating conditions.
What is the role of a control valve in a process control system?
A control valve is a critical component in a process control system that regulates the flow of fluid in response to a control signal. It can adjust the process conditions to maintain a setpoint, respond to changes in demand, or correct disturbances.
What is a control valve’s deadband?
A control valve’s deadband is the range of control signal values for which there is no appreciable change in the valve position. It can be caused by friction, backlash, or other mechanical factors, and it can degrade the control accuracy.
What is a control valve’s actuation speed?
A control valve’s actuation speed is the speed at which the valve can change its position in response to a change in the control signal. It can be affected by the actuator type, the valve size and design, and the process conditions.
What is a control valve’s response time?
A control valve’s response time is the time it takes for the valve to respond to a change in the control signal. It includes the time for the control signal to reach the actuator, the actuation time, and any delays due to the valve design or process conditions.
What is a control valve’s resolution?
A control valve’s resolution is the smallest change in the control signal that produces a measurable change in the valve position. It is a measure of the precision with which the valve can be controlled.
What is a control valve’s linearity?
A control valve’s linearity is the degree to which the valve’s flow characteristic follows a straight line. Perfect linearity means that each increment of the control signal produces an equal increment of flow rate.
What is a control valve’s repeatability?
A control valve’s repeatability is the ability of the valve to return to the same position for a given control signal, under the same conditions, over multiple cycles. It is a measure of the consistency of the valve’s performance.
How can control valve stick-slip be mitigated?
Stick-slip can be mitigated by ensuring proper maintenance of the control valve, including regular lubrication of moving parts and replacement of worn components. Additionally, using a valve positioner with enough resolution and control precision can help manage this issue.
What is a cage-guided control valve?
A cage-guided control valve is a design where the valve plug is guided by a cage that surrounds the plug. This type of design is often used in larger valves or when the forces or flow rates are high.
How does a solenoid operate in a control valve?
A solenoid in a control valve acts as an actuator, moving the valve stem and hence the valve plug to control the fluid flow. When the solenoid is energized, it generates a magnetic field that moves a plunger, and when it’s de-energized, the plunger returns to its original position, usually by a spring.
How can you determine if a control valve is passing?
A control valve is passing (leaking) if fluid is flowing through it when it should be fully closed. This can often be detected by a higher-than-normal downstream pressure or flow rate, or by direct observation or testing of the valve.
How can flashing and cavitation in control valves be prevented?
Flashing and cavitation can be prevented by designing the system to avoid conditions where the fluid pressure falls below its vapor pressure, by using control valves designed to handle these conditions, and by using cavitation suppressors or other methods to manage the pressure recovery.
What is a balanced plug control valve?
A balanced plug control valve is a design where the forces on the valve plug are balanced to reduce the actuation force needed. This can be achieved by having equal pressures on both sides of the plug or by using a double-seated design.
Why might a control valve vibrate?
Control valve vibration can be caused by several factors, including turbulence in the fluid flow, pressure pulsations, mechanical resonance, or improper alignment or mounting of the valve or actuator. Prolonged vibration can lead to wear and damage to the valve and associated equipment.
What is a double-seated control valve?
A double-seated control valve is a design with two seats and a plug that contacts both seats. This can provide a balanced force on the plug, reducing the actuation force needed, but it may have less shut-off tightness than a single-seated design.
How do control valves handle mixed-phase flow?
Control valves handle mixed-phase flow (i.e., mixtures of gas and liquid) by maintaining a flow path that allows both phases to flow together. However, the flow characteristics can be complex and unpredictable, and special valve designs or operating procedures may be needed to avoid problems such as cavitation, erosion, or improper control.
What is the role of a control valve in a bypass line?
A control valve in a bypass line allows some of the fluid to be diverted around a main valve or piece of equipment. This can be used to control the total flow rate, to provide a backup flow path, or to protect equipment from excessive flow or pressure.
How can control valves be tested?
Control valves can be tested by applying a control signal and observing the response, by measuring the flow rate or pressure at different valve positions, or by using specialized testing equipment or software. Tests can check for accuracy, repeatability, hysteresis, deadband, and other performance characteristics, and for problems such as leakage or stick-slip.
Read Next: