Instrumentation Engineers Case Study – Problems & Solutions
In this article, you will learn about the instrumentation engineers’ case studies, the types of problems that they face, and their solutions.
Case Study 1 – Control Valve Problem
Problem: A chemical plant is experiencing problems with a control valve that is responsible for controlling the flow of a certain chemical. The valve is not responding correctly to the control signals, causing the flow to fluctuate. This is causing the process to become unstable and resulting in product losses.
Solution: The instrumentation engineer first performed a thorough inspection of the control valve and related equipment to identify the problem. It was discovered that the control valve actuator was malfunctioning, causing the valve to stick and not respond correctly to the control signals.
The instrumentation engineer replaced the actuator and calibrated the valve to the correct position. The engineer also implemented a regular maintenance schedule to ensure the valve is working correctly and to prevent future problems.
Case Study 2 – Pressure Measurement Error
Problem: A gas pipeline company is facing problems with the pressure measurement system on one of their pipelines. The pressure readings are consistently higher than expected, which is causing the compressors to shut down frequently. This is resulting in lost production and increased maintenance costs.
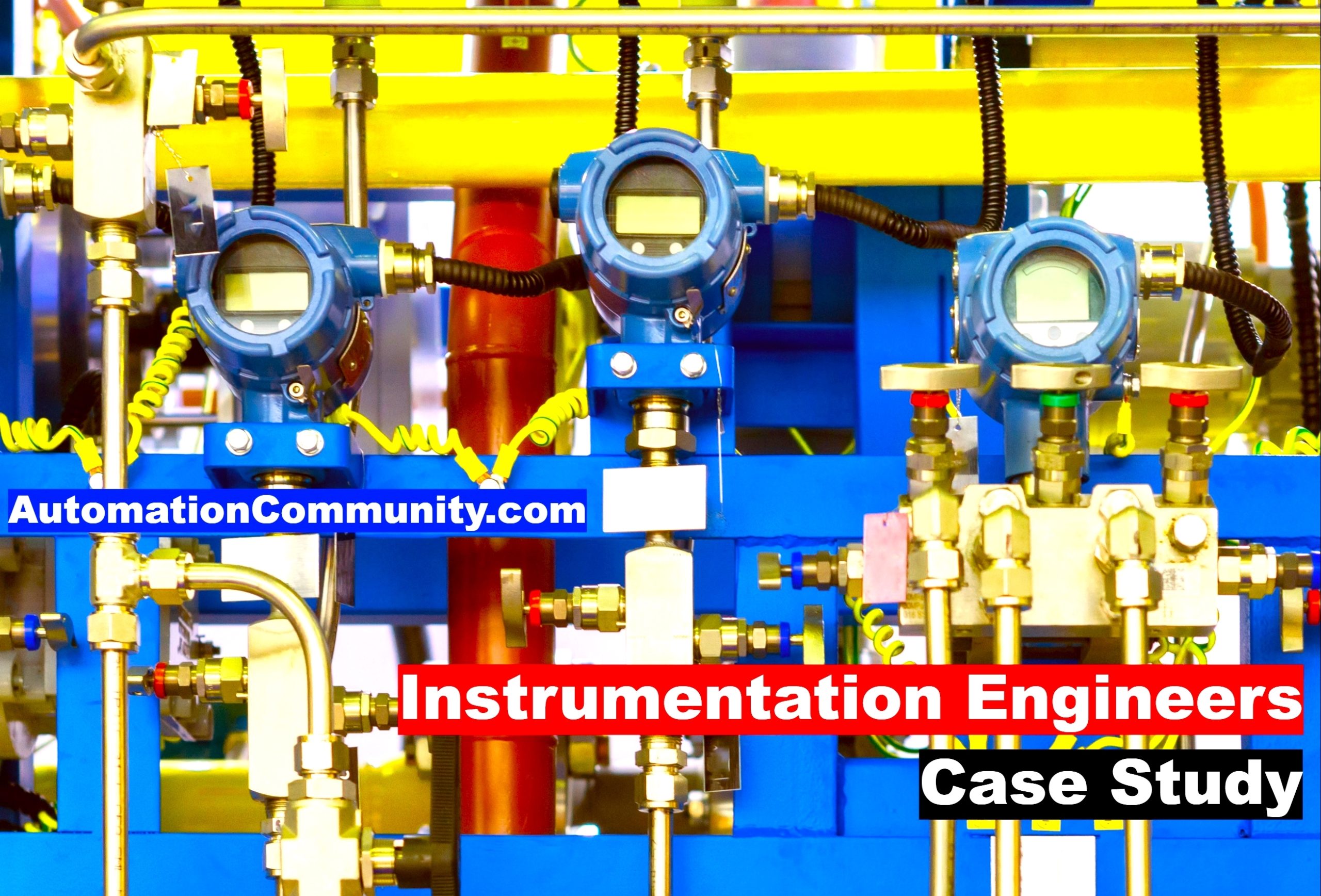
Solution: The instrumentation engineer first performed a thorough investigation of the pressure measurement system, including the sensors and the control system. It was discovered that the pressure sensors were configured with the wrong LRV and URV parameters causing the pressure readings to be higher than actual.
The instrumentation engineer reconfigured the pressure transmitter, and also modified the control system to account for the correct pressure range.
Case Study 3 – Flow Measurement Error
Problem: A water treatment plant is experiencing problems with its flow measurement system. The flow readings are consistently lower than expected, which is causing the treatment process to become inefficient. This is resulting in higher operating costs and increased discharge of pollutants.
Solution: The instrumentation engineer discovered that the flow sensors were clogged with debris, causing the flow readings to be lower than actual.
The instrument engineer cleaned the sensors, and also implemented a regular cleaning schedule to ensure the flow measurement system is working correctly and to prevent future problems. Additionally, the engineer improved the design of the flow measurement system to make it more resistant to clogging.
Case Study 4 – Temperature Measurement Error
Problem: A power plant is experiencing problems with its temperature measurement system in a boiler. The temperature readings are consistently lower than expected, which is causing the boiler to not operate at optimal efficiency. This is resulting in increased fuel consumption and higher operating costs.
Solution: The instrument engineer discovered that the temperature sensors were not properly installed, causing the temperature readings to be lower than actual.
The instrumentation engineer re-installed the sensors and also calibrated the temperature transmitter to the correct temperature range.
Case Study 5 – Calibration and Maintenance of Instruments
In a chemical processing plant, an instrumentation engineer was responsible for maintaining and calibrating a variety of instruments used to measure temperature, pressure, and flow.
Over time, the engineer noticed that the temperature readings were consistently off by a few degrees.
After investigating, the engineer discovered that the temperature transmitter had not been calibrated in over a year. The engineer calibrated the transmitter and the temperature readings became accurate again.
This case study highlights the importance of regular calibration and maintenance of instruments to ensure accurate measurements.
Case Study 6 – Interference from External Sources
In a power generation facility, an instrumentation engineer was responsible for monitoring the voltage and current in the electrical distribution system. The engineer noticed that the voltage and current readings were fluctuating randomly.
After investigating, the engineer discovered that the readings were being affected by electromagnetic interference (EMI) from a nearby radio tower.
The engineer installed EMI filters on the instrumentation and the readings became accurate again.
This case study illustrates the importance of identifying and mitigating external sources of interference that can affect instrumentation.
Case Study 7 – Signal Noise
In a wastewater treatment plant, an instrumentation engineer was responsible for monitoring the pH of the water. The engineer noticed that the pH readings were fluctuating randomly, even when the water was not being chemically treated.
After investigating, the engineer discovered that the pH probe was picking up noise from the pump motor, which was located in close proximity to the probe. The engineer installed a noise filter on the signal, and the pH readings became stable. This case study highlights the importance of addressing signal noise to ensure accurate measurements.
Case Study 8 – Cybersecurity Concerns
In the Pharmaceutical Industry, an instrumentation engineer was responsible for monitoring and controlling the temperature and humidity of the cleanroom. The engineer noticed that the temperature and humidity readings were fluctuating randomly.
Free CyberSecurity Course – Register Now
After checking, the engineer discovered that the control system had been hacked and the temperature and humidity were being manipulated remotely. The engineer installed firewalls and other security measures to protect the control system from further hacking attempts. This case study illustrates the importance of addressing cybersecurity concerns in industrial control systems.
These are just a few examples of the types of problems that instrumentation engineers may face. However, the specific problems will vary based on the project, industry, and the instruments used.
Read Next:
Comments
2
je suis un apprenti en instrumentation avec un niveau d’étude BTS je voulais avoir encore plus de connaissance. don’t speak english well i want to leanr a instrumentation thank u
Translated – I am an apprentice in instrumentation with a BTS level of study I wanted to have even more knowledge. don’t speak English well I want to learn instrumentation thank u
good