What is Industrial Automation? History, Types, Advantages, Disadvantages
Industrial automation refers to the use of control systems and technology to monitor and control industrial processes and equipment. It involves the use of computers, programmable logic controllers (PLCs), and other devices to automatically perform tasks that were previously done by human operators.
The goal of industrial automation is to increase efficiency, reduce the need for human labor, and improve the quality and consistency of the products being produced. It is used in a wide variety of industries, including manufacturing, power generation, water and wastewater treatment, oil and gas production, and chemical processing.
Industrial automation systems can include a variety of components, such as sensors and actuators to monitor and control processes, human-machine interfaces (HMIs) to allow operators to monitor and input commands, and communication networks to allow different components to communicate with one another.
Industrial automation is an important tool for improving the efficiency and effectiveness of industrial processes.
History of Industrial Automation
The history of industrial automation can be traced back to the late 1800s when the first electric motor was used to automate the production of locks and other products.
However, it was not until the 1950s and 1960s that industrial automation began to take off, with the development of programmable logic controllers (PLCs) and other technologies.
Some key events and milestones in the history of industrial automation include:
- 1882: Charles Babbage’s Analytical Engine, a mechanical computer, is designed but never built.
- 1890: The first electric motor is used to automate the production of locks.
- 1922: The Ford Motor Company opens the first assembly line, which uses conveyor belts and other mechanical devices to automate the production of cars.
- 1937: George Devol patents the first programmable device, which eventually leads to the development of programmable logic controllers (PLCs).
- 1968: The first PLC, the Programmable Controller, is developed by General Motors and Westinghouse.
- 1970s: PLCs become widely used in industry for automating processes.
- 1980s: The use of computers and other digital technologies begins to increase in industrial automation.
- 1990s: The internet becomes widely available, leading to the development of web-based industrial automation systems.
The history of industrial automation has seen the development of many important technologies and systems that have greatly increased the efficiency and effectiveness of industrial processes.
Types of Industrial Automation
There are several different types of industrial automation, which can be classified based on the level of control and the degree to which tasks are automated:
- Fixed Automation: This is the most basic level of automation, in which a machine is designed to perform a specific task without the need for operator intervention. An example of fixed automation is an assembly line in which each machine performs a specific task and then passes the workpiece on to the next machine.
- Programmable Automation: This type of automation involves the use of programmable logic controllers (PLCs) or other devices to control machines or processes. PLCs can be programmed to perform a variety of tasks and can be reprogrammed as needed to adapt to changing needs.
- Computer-Integrated Manufacturing (CIM): This type of automation involves the integration of computers and other digital technologies into the manufacturing process. CIM systems can control and monitor multiple machines and processes, and can be programmed to make decisions and adjust processes as needed.
- Robotic Automation: This type of automation involves the use of robots to perform tasks that were previously done by humans. Robots can be programmed to perform a variety of tasks, including welding, painting, and assembly.
The type of automation used will depend on the specific needs of the application, including the type of tasks being performed, the level of precision required, and the degree to which tasks need to be automated.
The below video explains the overview of industrial automation.
Importance of Industrial Automation
Industrial automation is an important tool for improving the efficiency and effectiveness of industrial processes. It involves the use of control systems and technology to monitor and control equipment and processes and can be used in a wide variety of industries, including manufacturing, power generation, water and wastewater treatment, oil and gas production, and chemical processing.
The use of industrial automation has many advantages, including increased efficiency, improved quality, reduced costs, and increased safety. It can also lead to increased competitiveness for businesses that adopt it, as it can help them to produce goods more efficiently and at a lower cost than their competitors.
Automation Systems
Industrial automation systems are used to control and monitor industrial processes, machinery, and equipment. These systems can range from simple, standalone devices to complex, multi-layered systems that involve a wide range of technologies, such as sensors, controllers, and communication networks.
Industrial automation systems are used in a variety of industries, including manufacturing, oil and gas, power generation, water and wastewater treatment, and transportation. They can be used to control and optimize processes, reduce labor costs, improve quality and accuracy, and increase productivity.
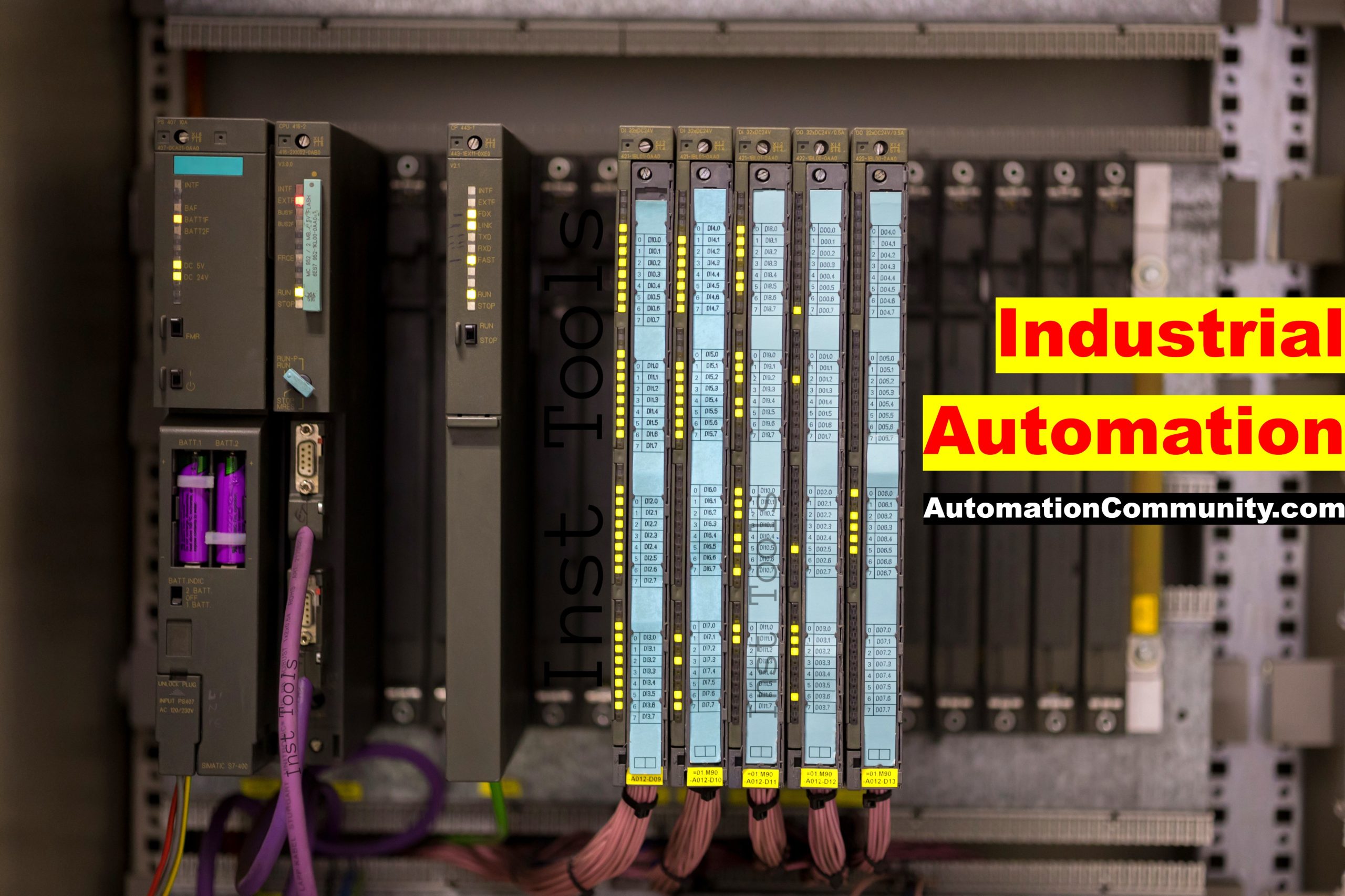
There are many different types of industrial automation systems, including:
- Programmable Logic Controllers (PLC): These are used to control industrial processes and machinery using a set of programmed instructions.
- Supervisory Control and Data Acquisition (SCADA) systems: These are used to monitor and control industrial processes over long distances, using a combination of hardware and software.
- Human-Machine Interfaces (HMI): These are used to interface between humans and industrial systems, allowing operators to monitor and control processes through a graphical user interface.
- Distributed Control Systems (DCS): These are used to control and monitor complex industrial processes that require high levels of accuracy and reliability.
- Manufacturing Execution Systems (MES): These are used to manage and optimize manufacturing processes, including scheduling, quality control, and inventory management.
There are many other types of industrial automation systems, each with its own specific features and capabilities.
Advantages of Industrial Automation
Industrial automation has several advantages that make it a useful tool for improving the efficiency and effectiveness of industrial processes:
- Increased Efficiency: Automation can increase the efficiency of processes by reducing the need for human labor and allowing machines to work around the clock. This can lead to increased production and reduced costs.
- Improved Quality: Automation can improve the quality of products by increasing consistency and reducing the potential for human error. This can lead to reduced defects and increased customer satisfaction.
- Reduced Costs: Automation can reduce costs by increasing production and reducing the need for labor. This can lead to increased profitability for businesses.
- Increased Safety: Automation can improve safety by reducing the need for human operators to perform tasks in hazardous environments. This can lead to a decrease in workplace accidents and injuries.
Industrial automation is a useful tool for increasing efficiency, improving quality, reducing costs, and improving safety in industrial processes.
Disadvantages of Industrial Automation
While industrial automation has many advantages, there are also some potential disadvantages that should be considered:
- Initial Costs: Implementing an automated system can be expensive, as it requires the purchase and installation of equipment and software. This can be a barrier for small businesses or those with limited resources.
- Lack of Flexibility: Automated systems are typically designed to perform specific tasks and may not be able to easily adapt to changing needs. This can make them inflexible and may require the purchase of additional equipment to handle new tasks.
- Lack of Creativity: Automated systems do not have the ability to think creatively or come up with new ideas. This can limit the types of tasks that they are capable of performing.
- Unemployment: Automation can lead to unemployment, as it reduces the need for human labor. This can be a concern for workers who may lose their jobs as a result of automation.
Industrial automation can bring many benefits, but it is important to carefully consider the potential disadvantages before implementing an automated system.
Read Next:
Comments
1
great information, thank you.