What is a Human Machine Interface (HMI)? Types, Advantages
In this article, you will learn what is a Human Machine Interface, the types of HMI, the selection of HMI, advantages, and disadvantages of HMI.
What is a Human Machine Interface?
A Human-Machine Interface (HMI) is a user interface that allows a human operator to interact with a machine or process. HMI is typically used in industrial settings to allow operators to monitor and control processes, such as those in a factory or power plant.
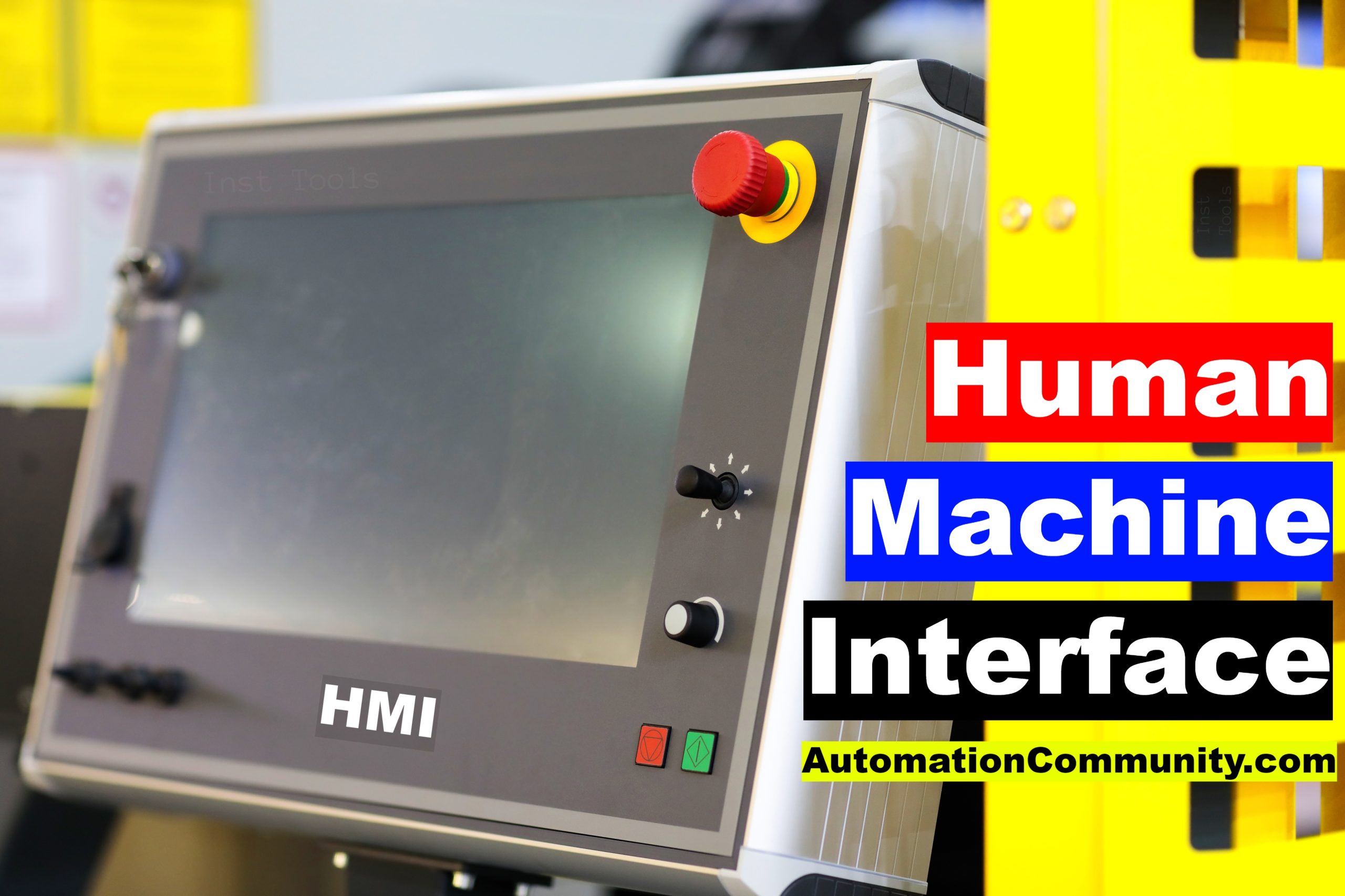
HMI can take a variety of forms, including graphical user interfaces (GUIs) on a computer, touchscreens, or physical control panels with buttons and displays. They are used to present process data to the operator, allow the operator to input commands and setpoints, and present alarms and other information.
HMI is typically connected to a programmable logic controller (PLC), which is responsible for controlling the process based on input from the HMI and sensors in the field. The HMI simply presents information to the operator and allows them to input commands, which are then sent to the PLC to be implemented.
Types of HMI
There are several different types of Human-Machine Interfaces (HMI), which can take a variety of forms depending on the needs of the application.
Some common types of HMI include:
- Graphical User Interfaces (GUIs): These are computer-based HMI that use a graphical interface to present process data and allow the operator to input commands. GUIs can be created using software such as Microsoft Windows or a specialized HMI software package.
- Touchscreens: These are HMI that use a touchscreen display to present process data and allow the operator to input commands. They are often used in applications where a physical control panel is not practical, such as in environments where space is limited.
- Physical Control Panels: These are physical HMI that use buttons, switches, and displays to present process data and allow the operator to input commands. They are often used in industrial settings where a GUI or touchscreen may not be practical, such as in environments with high levels of vibration or dust.
- Web-based HMI: These are HMI that use a web browser to present process data and allow the operator to input commands. They can be accessed from any device with a web browser, allowing operators to monitor and control processes remotely.
How to Choose an HMI?
When choosing a Human Machine Interface (HMI) for an industrial process or system, there are several factors to consider to ensure that the HMI is the best fit for the specific application.
- Compatibility: It is important to choose an HMI that is compatible with the equipment and systems that it will be controlling. This includes compatibility with the control system, communication protocols, and data formats used by the equipment.
- Hardware: The HMI should be designed to be rugged and durable, suitable for the environment where it will be installed. It should be able to withstand the temperature, humidity, and vibration that it will be exposed to.
- Display: The HMI should have a display that is clear, easy to read, and easy to navigate. The screen should be of a good resolution, with a high-quality display and backlight.
- Usability: The HMI should be easy to operate and understand, with intuitive navigation and clear, concise displays. It should be easy to use and understand by operators with different levels of expertise.
- Data visualization: The HMI should be able to display data in a clear and meaningful way, using graphics, charts, and other types of visual representations to help operators understand the process and make informed decisions.
- Customizability: The HMI should be customizable, with the ability to adapt to the specific needs of the process or equipment, as well as to the preferences of the operator.
- Remote access: The HMI should be designed to allow remote access so that operators can monitor and control the process from a remote location.
- Scalability: The HMI should be designed to be scalable, with the ability to handle more complexity and data as the process or equipment becomes more advanced.
- Support: The HMI vendor should provide good technical support and documentation, as well as software updates and upgrades.
- Cost: The HMI should be cost-effective and provide a good return on investment.
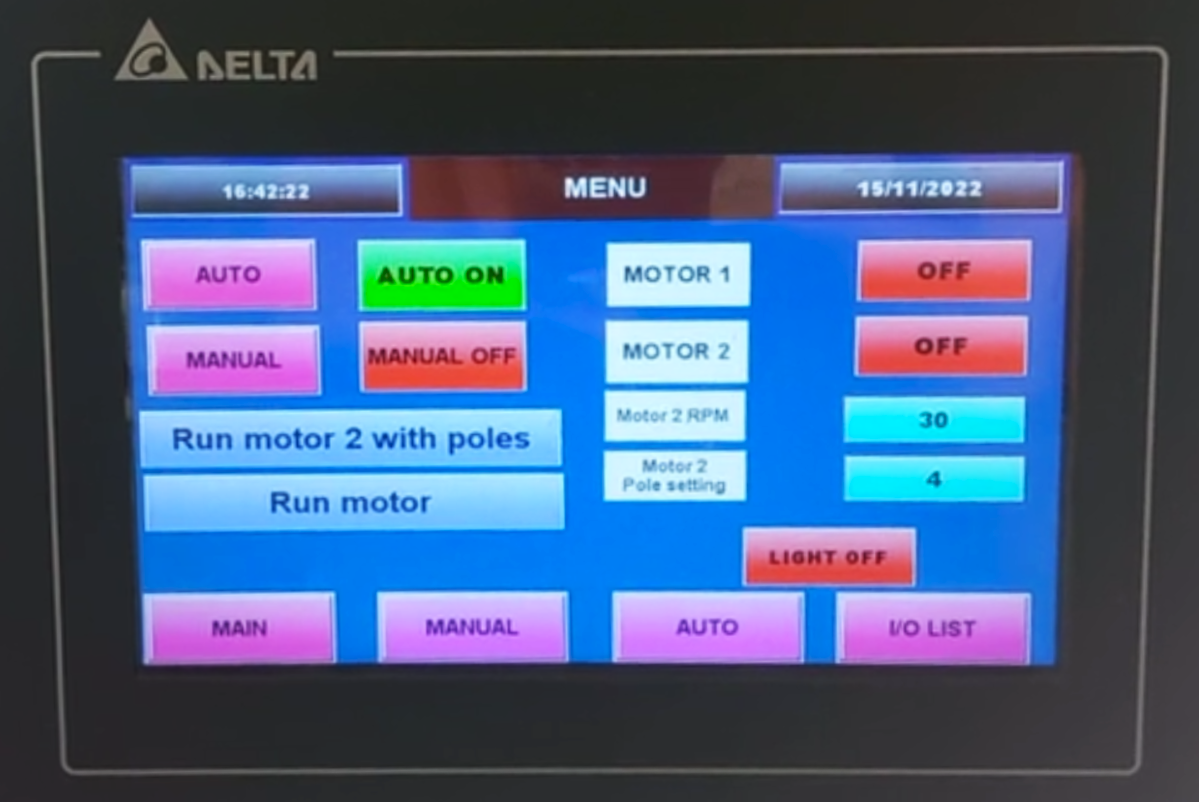
Advantages of Human-Machine Interface
Human-Machine Interfaces (HMI) have several advantages that make them useful for controlling and monitoring industrial processes:
- Improved Efficiency: HMI allows operators to easily access process data and input commands, which can improve the efficiency of the process being controlled. By presenting data in a clear and concise manner, operators can make more informed decisions and take timely action when necessary.
- Increased Safety: HMI can improve safety by presenting alarms and other important information to the operator. This allows operators to take timely action to address potential problems before they become serious.
- Remote Monitoring and Control: Many HMI can be accessed remotely, allowing operators to monitor and control processes from a distance. This can be particularly useful in applications where the process is located in a remote or hazardous location.
- Easy to Use: HMI is designed to be easy to use, even for operators who may not have technical expertise. This makes them an accessible tool for controlling and monitoring industrial processes.
Disadvantages of Human-Machine Interface
Human-Machine Interfaces (HMI) have some potential disadvantages that should be considered when determining whether to use one:
- Dependency on the HMI: If the HMI fails or becomes unavailable, the operator may not be able to access process data or input commands, which can hinder the operation of the process being controlled.
- Potential for Human Error: Operators can make mistakes when using HMI, such as inputting incorrect commands or failing to notice an alarm. This can lead to problems with the process being controlled.
- Additional Cost: Implementing an HMI can be an additional cost, as it requires the purchase and installation of the HMI itself as well as any associated hardware and software.
- Complexity: Some HMI can be complex, which can make them difficult to use or require additional training for operators. This can be a disadvantage in applications where the operator needs to be able to quickly and easily access process data and input commands.
Applications of HMI
Human-Machine Interfaces (HMI) are used in a variety of industrial applications where they can help improve the efficiency, safety, and accessibility of the process being controlled.
Some common applications of HMI include:
- Manufacturing: HMI is commonly used in manufacturing settings to control and monitor production processes, such as those on a factory floor. They can be used to present process data to operators, allow them to input commands and setpoints, and present alarms and other important information.
- Power Generation: HMI is also used in power generation plants, such as those that use fossil fuels or renewable energy sources, to monitor and control processes such as boiler operation, turbine control, and electrical generation and distribution.
- Water and Wastewater Treatment: HMI is used in water and wastewater treatment plants to control and monitor processes such as pumping, treatment, and distribution.
- Oil and Gas: HMI are used in oil and gas production and refining to control and monitor processes such as drilling, pumping, and refining.
- Chemical Processing: HMI is used in chemical processing plants to control and monitor processes such as mixing, reaction, and distillation.
Read Next: