Pressure Gauge Questions and Answers
Welcome to our Pressure Gauge Questions and Answers. In this section, we cover a wide range of topics related to pressure gauges including their principles of operation, parts, calibration, maintenance, and more.
Pressure Gauge Questions and Answers
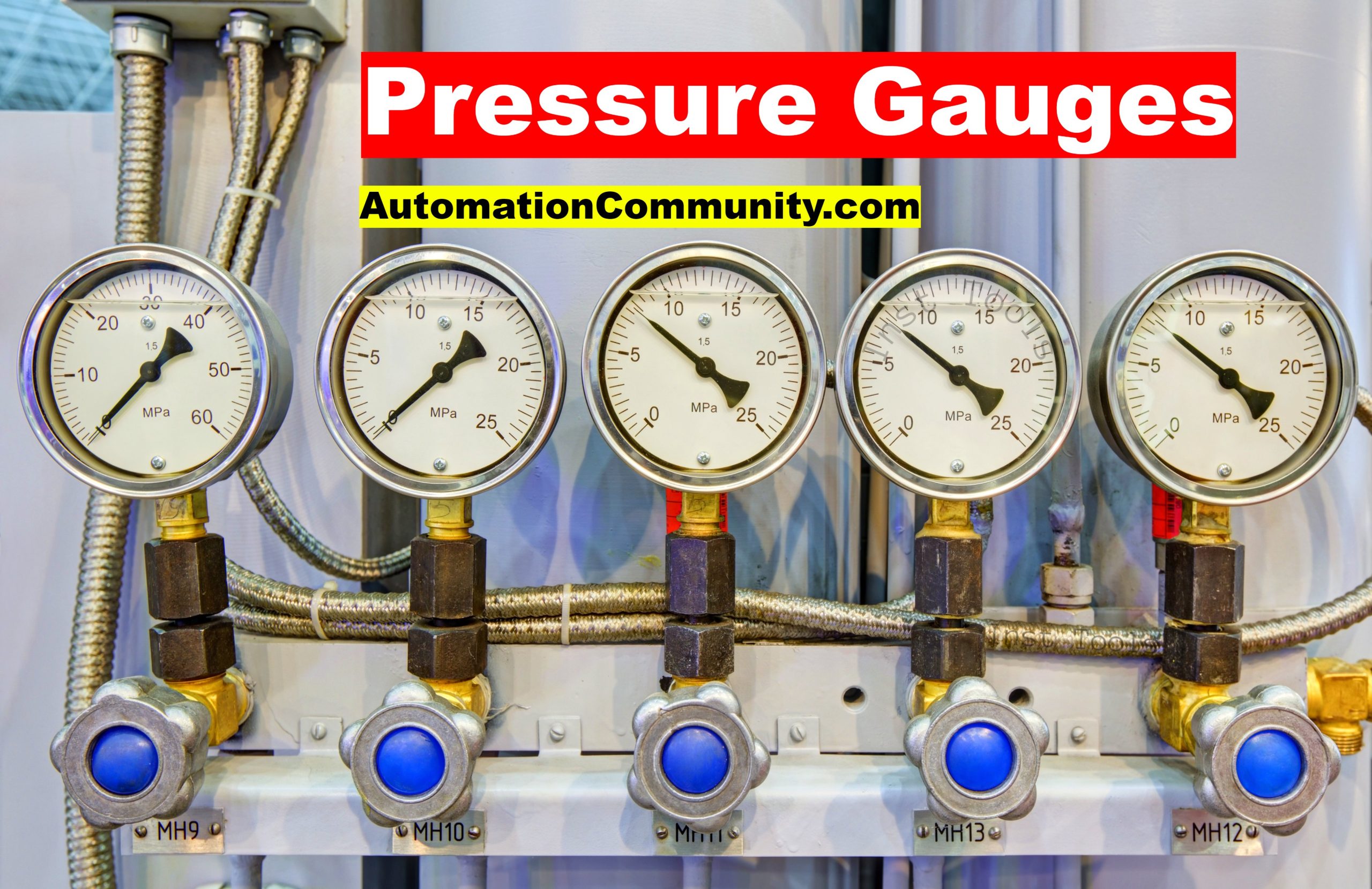
These questions and answers can help you deepen your understanding of pressure gauges and ensure that you’re using them correctly and safely. From common causes of gauge failure to best practices for maintenance, we have you covered with comprehensive and informative answers to your pressing pressure gauge questions.
What type of pressure gauge uses a U-shaped tube filled with liquid as its sensing element?
A) Bourdon tube gauge
B) Diaphragm gauge
C) Manometer gauge
D) Bellows gauge
Answer: C) Manometer gauge
Explanation: Manometer gauges use a U-shaped tube filled with liquid, such as mercury or water, to measure pressure. The pressure exerted on one end of the tube causes the liquid to rise on the other end, indicating the pressure.
Which type of pressure gauge is most commonly used in industrial applications?
A) Bourdon tube gauge
B) Diaphragm gauge
C) Capsule gauge
D) Bellows gauge
Answer: A) Bourdon tube gauge
Explanation: Bourdon tube gauges are the most commonly used type of pressure gauge in industrial applications due to their durability, reliability, and ability to measure a wide range of pressures.
What is the range of pressure that a low-pressure gauge typically measures?
A) 0-15 psi
B) 0-30 psi
C) 0-60 psi
D) 0-100 psi
Answer: A) 0-15 psi
Explanation: Low-pressure gauges are designed to measure pressures in the range of 0-15 psi, which is typically used in applications such as HVAC systems and pneumatic controls.
Which type of pressure gauge is best suited for measuring very high pressures?
A) Bourdon tube gauge
B) Diaphragm gauge
C) Piston gauge
D) Bellows gauge
Answer: C) Piston gauge
Explanation: Piston gauges are designed for measuring very high pressures, typically above 10,000 psi. They use a small piston that is subjected to the pressure being measured, and the movement of the piston is used to indicate the pressure.
What is the most common unit of measurement used for pressure gauges?
A) PSI
B) Bar
C) Pascal
D) Atmosphere
Answer: A) PSI
Explanation: PSI (pounds per square inch) is the most common unit of measurement used for pressure gauges, especially in the United States.
What is the difference between a pressure gauge and a pressure transmitter?
A) A pressure gauge is mechanical, while a pressure transmitter is electronic
B) A pressure gauge is more accurate than a pressure transmitter
C) A pressure gauge is less expensive than a pressure transmitter
D) A pressure gauge can measure a wider range of pressures than a pressure transmitter
Answer: A) A pressure gauge is mechanical, while a pressure transmitter is electronic
Explanation: A pressure gauge uses mechanical elements to indicate pressure, while a pressure transmitter uses electronic sensors and circuitry to measure and transmit pressure readings.
Which type of pressure gauge is best suited for measuring vacuum pressures?
A) Bourdon tube gauge
B) Diaphragm gauge
C) Bellows gauge
D) Manometer gauge
Answer: D) Manometer gauge
Explanation: Manometer gauges are best suited for measuring vacuum pressures, as they use a U-shaped tube filled with liquid to indicate the pressure difference between the vacuum and atmospheric pressure.
What is the purpose of a pressure gauge snubber?
A) To protect the gauge from damage due to vibration or pulsation
B) To increase the accuracy of the gauge reading
C) To reduce the effects of temperature changes on the gauge reading
D) To prevent contamination of the gauge with foreign substances
Answer: A) To protect the gauge from damage due to vibration or pulsation
Explanation: A pressure gauge snubber is a device that is installed between the gauge and the process being measured to protect the gauge from damage due to vibration or pulsation in the system. It helps to smooth out the pressure fluctuations and prevent the gauge from being damaged.
What is the purpose of a glycerin-filled pressure gauge?
A) To reduce the effects of temperature changes on the gauge reading
B) To increase the accuracy of the gauge reading
C) To protect the gauge from damage due to vibration or pulsation
D) To improve the visibility of the gauge reading
Answer: C) To protect the gauge from damage due to vibration or pulsation
Explanation: Glycerin-filled pressure gauges are designed to protect the gauge from damage due to vibration or pulsation in the system. The glycerin acts as a damping fluid that absorbs the shock and helps to smooth out the pressure fluctuations.
What is the purpose of a pressure gauge snubber with a porous metal element?
A) To protect the gauge from damage due to vibration or pulsation
B) To increase the accuracy of the gauge reading
C) To reduce the effects of temperature changes on the gauge reading
D) To prevent contamination of the gauge with foreign substances
Answer: D) To prevent contamination of the gauge with foreign substances
Explanation: A pressure gauge snubber with a porous metal element is designed to prevent the gauge from being contaminated with foreign substances that may be present in the process being measured. The porous metal element acts as a filter that allows the pressure to pass through but prevents any particles or contaminants from entering the gauge.
Which type of pressure gauge is best suited for measuring corrosive or highly viscous fluids?
A) Bourdon tube gauge
B) Diaphragm gauge
C) Capsule gauge
D) Bellows gauge
Answer: D) Bellows gauge
Explanation: Bellows gauges are best suited for measuring corrosive or highly viscous fluids, as they are designed to withstand harsh environments and can accommodate small amounts of solids or viscous fluids without clogging.
What is the purpose of a differential pressure gauge?
A) To measure the pressure in a closed system
B) To measure the difference in pressure between two points in a system
C) To regulate the pressure in a system
D) To maintain constant pressure in a system
Answer: B) To measure the difference in pressure between two points in a system
Explanation: A differential pressure gauge is used to measure the difference in pressure between two points in a system, such as across a filter or a valve.
What is the purpose of a pressure gauge with a back connection?
A) To allow the gauge to be mounted directly onto the process being measured
B) To allow the gauge to be mounted remotely from the process being measured
C) To protect the gauge from damage due to vibration or pulsation
D) To improve the visibility of the gauge reading
Answer: A) To allow the gauge to be mounted directly onto the process being measured
Explanation: A pressure gauge with a back connection is designed to allow the gauge to be mounted directly onto the process being measured, which provides a more accurate reading and reduces the risk of damage to the gauge.
What is the purpose of a pressure gauge with a front-flush diaphragm?
A) To reduce the effects of temperature changes on the gauge reading
B) To protect the gauge from damage due to vibration or pulsation
C) To prevent contamination of the gauge with foreign substances
D) To measure the pressure of fluids with high viscosity or containing solids
Answer: D) To measure the pressure of fluids with high viscosity or containing solids
Explanation: A pressure gauge with a front-flush diaphragm is designed to measure the pressure of fluids with high viscosity or containing solids, such as slurries or pastes. The front-flush diaphragm is flat and smooth, allowing it to easily slide over any solids or viscous materials in the process being measured, without clogging or affecting the accuracy of the reading.
What is the purpose of a snubber on a pressure gauge?
A) To protect the gauge from damage due to overpressure
B) To improve the accuracy of the gauge reading
C) To reduce the effects of vibration or pulsation on the gauge
D) To prevent the gauge from being contaminated with foreign substances
Answer: C) To reduce the effects of vibration or pulsation on the gauge
Explanation: A snubber is a small device that is installed between the process being measured and the pressure gauge, which reduces the effects of vibration or pulsation on the gauge. It works by restricting the flow of fluid to the gauge, which helps to dampen any sudden changes in pressure that could cause the gauge needle to fluctuate.
What is a pigtail syphon and what is it used for?
A) A coiled tube used to protect the gauge from damage due to overpressure
B) A device used to regulate the flow of fluid to the gauge
C) A device used to reduce the effects of temperature changes on the gauge reading
D) A tube used to protect the gauge from contamination by foreign substances
Answer: C) A device used to reduce the effects of temperature changes on the gauge reading
Explanation: A pigtail syphon is a coiled tube that is installed between the process being measured and the gauge, which helps to reduce the effects of temperature changes on the gauge reading. The coiled design allows for expansion and contraction of the fluid, which prevents damage to the gauge due to thermal stress.
What is a U syphon and what is it used for?
A) A coiled tube used to protect the gauge from damage due to overpressure
B) A device used to regulate the flow of fluid to the gauge
C) A device used to reduce the effects of temperature changes on the gauge reading
D) A tube used to protect the gauge from contamination by foreign substances
Answer: A) A coiled tube used to protect the gauge from damage due to overpressure
Explanation: A U syphon is a coiled tube that is installed between the process being measured and the gauge, which protects the gauge from damage due to overpressure. The coiled design allows for expansion and contraction of the fluid, which prevents damage to the gauge due to pressure spikes.
What is a gauge saver and what is it used for?
A) A device used to protect the gauge from damage due to overpressure
B) A device used to regulate the flow of fluid to the gauge
C) A device used to reduce the effects of temperature changes on the gauge reading
D) A device used to protect the gauge from contamination by foreign substances
Answer: A) A device used to protect the gauge from damage due to overpressure
Explanation: A gauge saver is a device that is installed between the process being measured and the gauge, which protects the gauge from damage due to overpressure. It prevents the gauge from being exposed to pressure levels that exceed its maximum range.
What is a gauge adapter and what is it used for?
A) A device used to connect the gauge to the process being measured
B) A device used to regulate the flow of fluid to the gauge
C) A device used to reduce the effects of temperature changes on the gauge reading
D) A device used to protect the gauge from damage due to overpressure
Answer: A) A device used to connect the gauge to the process being measured
Explanation: A gauge adapter is a device that is used to connect the gauge to the process being measured. It is used when the process connection is different from the connection on the gauge. The adapter allows the gauge to be installed without modifying
What is a gauge union and what is it used for?
A) A device used to connect two different gauges together
B) A device used to connect the gauge to the process being measured
C) A device used to regulate the flow of fluid to the gauge
D) A device used to protect the gauge from damage due to overpressure
Answer: B) A device used to connect the gauge to the process being measured
Explanation: A gauge union is a device that is used to connect the gauge to the process being measured. It is typically used when the process connection is different from the connection on the gauge, and the adapter is not suitable for the application. The union provides a tight and secure connection between the process and the gauge.
What is the purpose of a gauge isolation valve?
A) To regulate the flow of fluid to the gauge
B) To protect the gauge from damage due to overpressure
C) To isolate the gauge from the process being measured
D) To prevent the gauge from being contaminated with foreign substances
Answer: C) To isolate the gauge from the process being measured
Explanation: A gauge isolation valve is a device that is installed between the process being measured and the gauge, which allows the gauge to be isolated from the process when necessary. This is useful for maintenance and calibration purposes, as well as for safety reasons.
What is a diaphragm seal and what is it used for?
A) A device used to regulate the flow of fluid to the gauge
B) A device used to protect the gauge from damage due to overpressure
C) A device used to isolate the gauge from the process being measured
D) A device used to reduce the effects of corrosive or viscous fluids on the gauge
Answer: D) A device used to reduce the effects of corrosive or viscous fluids on the gauge
Explanation: A diaphragm seal is a device that is installed between the process being measured and the gauge, which protects the gauge from corrosive or viscous fluids. The seal consists of a flexible diaphragm that is in contact with the process fluid, and a fluid-filled chamber that transmits the pressure to the gauge. This allows the gauge to be used in applications where the process fluid is aggressive or difficult to measure.
What is a capillary tube and what is it used for?
A) A tube used to protect the gauge from damage due to overpressure
B) A tube used to regulate the flow of fluid to the gauge
C) A tube used to reduce the effects of temperature changes on the gauge reading
D) A tube used to protect the gauge from contamination by foreign substances
Answer: C) A tube used to reduce the effects of temperature changes on the gauge reading
Explanation: A capillary tube is a long, thin tube that is installed between the process being measured and the gauge, which reduces the effects of temperature changes on the gauge reading. The tube is filled with a fluid that expands and contracts with changes in temperature, which helps to compensate for the effects of temperature on the gauge.
What is a gauge cock and what is it used for?
A) A device used to protect the gauge from damage due to overpressure
B) A device used to isolate the gauge from the process being measured
C) A device used to regulate the flow of fluid to the gauge
D) A device used to shut off the flow of fluid to the gauge
Answer: D) A device used to shut off the flow of fluid to the gauge
Explanation: A gauge cock is a valve that is installed between the process being measured and the gauge, which allows the flow of fluid to be shut off to the gauge when necessary.
What is the principle behind a pressure gauge?
A) It uses a diaphragm to convert pressure into a mechanical deflection
B) It uses a bourdon tube to convert pressure into a mechanical deflection
C) It uses a piezoelectric crystal to convert pressure into an electrical signal
D) It uses a thermocouple to convert pressure into a temperature reading
Answer: B) It uses a bourdon tube to convert pressure into a mechanical deflection
Explanation: A bourdon tube is a curved, hollow metal tube that is closed at one end and open at the other. When pressure is applied to the tube, it tends to straighten out, which causes the free end to move in response to changes in pressure. This motion is then transmitted to a mechanical linkage, which drives the pointer on the gauge face.
How does a pressure gauge measure absolute pressure?
A) It measures the difference between the pressure being measured and a reference pressure
B) It measures the pressure being measured with respect to a perfect vacuum
C) It measures the pressure being measured with respect to atmospheric pressure
D) It cannot measure absolute pressure
Answer: B) It measures the pressure being measured with respect to a perfect vacuum
Explanation: Absolute pressure is the pressure of a fluid with respect to a perfect vacuum. A pressure gauge that measures absolute pressure has a sealed reference chamber inside, which is evacuated to create a perfect vacuum. The pressure being measured is then applied to the other side of the gauge diaphragm or bourdon tube, and the difference in pressure between the vacuum and the process is indicated on the gauge face.
How does a pressure gauge measure gauge pressure?
A) It measures the difference between the pressure being measured and a reference pressure
B) It measures the pressure being measured with respect to a perfect vacuum
C) It measures the pressure being measured with respect to atmospheric pressure
D) It cannot measure gauge pressure
Answer: A) It measures the difference between the pressure being measured and a reference pressure
Explanation: Gauge pressure is the pressure of a fluid with respect to atmospheric pressure. A pressure gauge that measures gauge pressure has a reference chamber open to the atmosphere on one side, and the pressure being measured applied to the other side of the gauge diaphragm or bourdon tube. The difference in pressure between the process and the atmospheric reference is indicated on the gauge face.
How does a pressure gauge measure differential pressure?
A) It measures the difference between the pressure being measured and a reference pressure
B) It measures the pressure being measured with respect to a perfect vacuum
C) It measures the difference in pressure between two points in a system
D) It cannot measure differential pressure
Answer: C) It measures the difference in pressure between two points in a system
Explanation: Differential pressure is the difference in pressure between two points in a fluid system. A pressure gauge that measures differential pressure has two pressure connections, one for each point being measured, and the gauge mechanism measures the difference between the two pressures and indicates it on the gauge face.
How does a pressure gauge measure compound pressure?
A) It measures the difference between the pressure being measured and a reference pressure
B) It measures the pressure being measured with respect to a perfect vacuum
C) It measures the pressure being measured with respect to atmospheric pressure
D) It measures both positive and negative pressures relative to a reference point
Answer: D) It measures both positive and negative pressures relative to a reference point
Explanation: Compound pressure is a combination of positive and negative pressures relative to a reference point. A pressure gauge that measures compound pressure has two pressure connections, one for positive pressure and one for negative pressure, and the gauge mechanism measures the difference between the two pressures and indicates it
What are the main parts of a bourdon tube pressure gauge?
A) Dial face, pointer, movement, bourdon tube, connection
B) Glass cover, bezel, bourdon tube, movement, pointer
C) Connection, bezel, dial face, bourdon tube, pointer
D) Bezel, dial face, movement, bourdon tube, connection
Answer: D) Bezel, dial face, movement, bourdon tube, connection
Explanation: The main parts of a bourdon tube pressure gauge include a bezel or ring that secures the dial face, a dial face that displays the pressure measurement, a movement or mechanism that translates the deflection of the bourdon tube into a pointer movement, a bourdon tube that deflects in response to pressure changes, and a connection that connects the bourdon tube to the process being measured.
What is the purpose of the bourdon tube in a pressure gauge?
A) To magnify the pressure reading
B) To provide a visual indication of pressure changes
C) To convert pressure into a mechanical deflection
D) To protect the gauge from overpressure
Answer: C) To convert pressure into a mechanical deflection
Explanation: The bourdon tube is the sensing element of a pressure gauge that converts pressure changes into a mechanical deflection. It is typically made of a curved, hollow metal tube that tends to straighten out when pressure is applied to it. The amount of deflection is proportional to the difference between the pressure being measured and a reference pressure.
What is the purpose of the pointer in a pressure gauge?
A) To hold the glass cover in place
B) To indicate the pressure reading on the dial face
C) To protect the gauge from overpressure
D) To connect the bourdon tube to the process being measured
Answer: B) To indicate the pressure reading on the dial face
Explanation: The pointer on a pressure gauge is connected to the gauge movement and moves in response to the deflection of the bourdon tube. It points to the pressure measurement on the dial face and provides a visual indication of the pressure being measured.
What is the purpose of the glass cover on a pressure gauge?
A) To protect the pointer from damage
B) To magnify the pressure reading
C) To provide a visual indication of pressure changes
D) To protect the dial face from damage
Answer: D) To protect the dial face from damage
Explanation: The glass cover on a pressure gauge is typically made of clear or tinted glass and is designed to protect the dial face from damage due to impact, dirt, or moisture. It is usually held in place by a bezel or ring that secures the gauge components in place.
What is the purpose of the connection on a pressure gauge?
A) To hold the bourdon tube in place
B) To provide a visual indication of pressure changes
C) To connect the gauge to the process being measured
D) To protect the gauge from overpressure
Answer: C) To connect the gauge to the process being measured
Explanation: The connection on a pressure gauge is the interface between the gauge and the process being measured. It typically consists of a threaded or flanged connection that allows the gauge to be connected directly to the process. The connection also provides a secure attachment point for the bourdon tube or other sensing element.
What is the purpose of the movement in a pressure gauge?
A) To convert pressure into a mechanical deflection
B) To provide a visual indication of pressure changes
C) To protect the gauge from overpressure
D) To hold the bourdon tube in place
Answer: A) To convert pressure into a mechanical deflection
Explanation: The movement in a pressure gauge is responsible for translating the deflection of the bourdon tube into a mechanical movement of the pointer. It typically consists of a series of gears, levers, and pivots that amplify and transmit the motion of the bourdon tube to the pointer.
What is the purpose of the bezel on a pressure gauge?
A) To hold the dial face in place
B) To protect the gauge from overpressure
C) To provide a visual indication of pressure changes
D) To hold the bourdon tube in place
Answer: A) To hold the dial face in place
Explanation: The bezel on a pressure gauge is a ring or collar that holds the dial face and glass cover in place. It is usually threaded or snap-fit onto the gauge case and provides a secure attachment point for the gauge components.
What is the purpose of the case on a pressure gauge?
A) To provide a visual indication of pressure changes
B) To protect the gauge from overpressure
C) To hold the bourdon tube in place
D) To hold the movement in place
Answer: B) To protect the gauge from overpressure
Explanation: The case on a pressure gauge is typically made of a durable material such as stainless steel or brass and is designed to protect the gauge components from damage due to overpressure, impact, or other environmental factors. It also provides a mounting surface for the gauge and may include a vent or relief port to prevent damage in the event of overpressure.
What is the purpose of the gauge fill fluid in a filled-type pressure gauge?
A) To magnify the pressure reading
B) To provide a visual indication of pressure changes
C) To lubricate the bourdon tube
D) To dampen vibration and pulsation effects
Answer: D) To dampen vibration and pulsation effects
Explanation: Filled-type pressure gauges are filled with a special fluid that helps to dampen the effects of vibration and pulsation on the gauge components. The fluid is typically a viscous oil or glycerin-based solution that is selected based on the process conditions and application requirements.
What is the purpose of the dial face on a pressure gauge?
A) To provide a mounting surface for the gauge
B) To hold the bourdon tube in place
C) To provide a visual indication of pressure changes
D) To dampen vibration and pulsation effects
Answer: C) To provide a visual indication of pressure changes
Explanation: The dial face on a pressure gauge is the part of the gauge that displays the pressure measurement in a clear and easy-to-read format. It typically includes a series of markings, such as numbers or graduations, that correspond to different pressure values. The dial face may also include other features, such as color-coding or warning zones, to help users quickly identify pressure conditions.
What is the purpose of the scale plate on a pressure gauge?
A) To provide a visual indication of pressure changes
B) To hold the bourdon tube in place
C) To convert pressure into a mechanical deflection
D) To dampen vibration and pulsation effects
Answer: A) To provide a visual indication of pressure changes
Explanation: The scale plate on a pressure gauge is the part of the gauge that includes the markings or graduations that correspond to different pressure values. It is typically mounted behind the dial face and provides a visual reference for the user to read the current pressure measurement.
Why is calibration important for pressure gauges?
A) To ensure the gauge is installed correctly
B) To verify the accuracy of the gauge’s measurement
C) To protect the gauge from damage
D) To ensure the gauge is properly grounded
Answer: B) To verify the accuracy of the gauge’s measurement
Explanation: Calibration is the process of verifying the accuracy of a pressure gauge’s measurement against a known reference standard. It is important to ensure that the gauge is providing reliable and accurate measurements, which is crucial for maintaining process safety, product quality, and regulatory compliance.
What are some common methods used for calibrating pressure gauges?
A) Hydraulic deadweight testers, digital indicators, and analog gauges
B) Sight glasses, pressure relief valves, and flow meters
C) Temperature sensors, thermocouples, and RTDs
D) None of the above
Answer: A) Hydraulic deadweight testers, digital indicators, and analog gauges
Explanation: There are several methods used for calibrating pressure gauges, but some of the most common include using hydraulic deadweight testers, digital indicators, and analog gauges. These methods provide accurate and reliable measurements that can be used to determine the gauge’s accuracy and make any necessary adjustments.
How often should pressure gauges be calibrated?
A) Once a year
B) Every two years
C) Every five years
D) It depends on the application and the manufacturer’s recommendations
Answer: D) It depends on the application and the manufacturer’s recommendations
Explanation: The frequency of calibration for pressure gauges depends on the application, the environment, and the manufacturer’s recommendations. In some cases, gauges may need to be calibrated more frequently, such as in critical applications or harsh environments.
What is the purpose of maintenance for pressure gauges?
A) To prevent damage to the gauge
B) To extend the life of the gauge
C) To ensure the gauge is functioning properly
D) All of the above
Answer: D) All of the above
Explanation: Regular maintenance of pressure gauges is important to prevent damage, extend the life of the gauge, and ensure that the gauge is functioning properly. Maintenance may include cleaning, inspection, and replacement of damaged or worn components.
What are some common maintenance tasks for pressure gauges?
A) Cleaning, inspection, and replacement of damaged or worn components
B) Lubrication of moving parts and tightening of connections
C) Verification of accuracy and adjustment of calibration as necessary
D) All of the above
Answer: D) All of the above
Explanation: Common maintenance tasks for pressure gauges include cleaning, inspection, and replacement of damaged or worn components, lubrication of moving parts, and verification of accuracy and adjustment of calibration as necessary. These tasks can help ensure that the gauge is functioning properly and providing accurate measurements.
What are some common causes of pressure gauge failure?
A) Overpressure, vibration, and temperature extremes
B) Exposure to corrosive or abrasive materials
C) Incorrect installation or use
D) All of the above
Answer: D) All of the above
Explanation: Pressure gauge failure can be caused by a number of factors, including overpressure, vibration, temperature extremes, exposure to corrosive or abrasive materials, and incorrect installation or use. Regular maintenance and calibration can help prevent some of these issues and ensure the gauge is functioning properly.
How can overpressure damage a pressure gauge?
A) By causing the gauge to become inaccurate
B) By causing the gauge to fail catastrophically
C) By causing the gauge to rupture or explode
D) All of the above
Answer: D) All of the above
Explanation: Overpressure can cause a number of issues with pressure gauges, including inaccuracies in measurement, catastrophic failure, or even rupture or explosion of the gauge. It is important to use pressure gauges that are rated for the intended application and to avoid subjecting them to pressures beyond their capabilities.
What is a common method for verifying the accuracy of a pressure gauge?
A) Comparing its readings to another gauge
B) Using a multimeter
C) Measuring the gauge’s electrical output
D) All of the above
Answer: A) Comparing its readings to another gauge
Explanation: A common method for verifying the accuracy of a pressure gauge is to compare its readings to those of another gauge that is known to be accurate. This can help identify any discrepancies and determine if calibration is necessary.
How can vibration damage a pressure gauge?
A) By causing the gauge to become inaccurate
B) By causing the gauge to fail catastrophically
C) By causing the gauge’s internal components to become damaged or dislodged
D) All of the above
Answer: C) By causing the gauge’s internal components to become damaged or dislodged
Explanation: Vibration can cause damage to a pressure gauge’s internal components, leading to inaccuracies in measurement or even catastrophic failure. It is important to select gauges that are designed to withstand the levels of vibration present in the application and to properly secure them in place.
What are some best practices for maintaining pressure gauges?
A) Regular calibration and inspection
B) Proper installation and use
C) Protecting gauges from damage and exposure to harsh environments
D) All of the above
Answer: D) All of the above
Explanation: Best practices for maintaining pressure gauges include regular calibration and inspection, proper installation and use, and protecting gauges from damage and exposure to harsh environments. These practices can help ensure the gauge is providing accurate measurements and functioning properly.
What can happen if a pressure gauge is exposed to corrosive materials?
A) The gauge may become inaccurate
B) The gauge may fail completely
C) The gauge may become damaged and need repair
D) All of the above
Answer: D) All of the above
Explanation: Exposure to corrosive materials can damage the gauge’s casing or internal components, leading to inaccuracies or complete failure. Regular maintenance and cleaning can help prevent damage from exposure to corrosive materials.
Can pressure gauge failure be caused by overpressure?
A) Yes
B) No
Answer: A) Yes
Explanation: Overpressure can cause a pressure gauge to become inaccurate or fail completely, leading to potentially dangerous situations. Gauges should be selected based on the intended application and the maximum pressure they will be subjected to.
How can exposure to extreme temperatures affect a pressure gauge?
A) It can cause the gauge to become inaccurate
B) It can damage the gauge
C) It can cause the gauge to fail completely
D) All of the above
Answer: D) All of the above
Explanation: Exposure to extreme temperatures can cause a pressure gauge to become inaccurate, damage the gauge’s components, or even cause it to fail completely. Gauges should be selected based on the intended temperature range.
Can pressure gauge failure pose a safety hazard?
A) Yes
B) No
Answer: A) Yes
Explanation: Pressure gauge failure can pose a safety hazard if it leads to inaccurate measurements or complete failure, potentially
Can pressure gauge failure be prevented with regular maintenance?
A) Yes
B) No
Answer: A) Yes
Explanation: Regular maintenance, including calibration, cleaning, and inspection, can help prevent pressure gauge failure and ensure accurate measurements.
Read Next: