Instrument Impulse Line Questions and Answers
Instrument impulse lines play a critical role in various industrial processes where accurate measurements of fluid pressure are essential. These lines serve as the connection between the process and the instrument, ensuring the transmission of pressure without compromising accuracy.
Instrument impulse lines are designed to withstand the harsh conditions often present in industrial environments, including high temperatures, corrosive substances, and high-pressure levels. They are constructed using materials that offer resistance to these conditions, such as stainless steel or other corrosion-resistant alloys.
Instrument Impulse Line
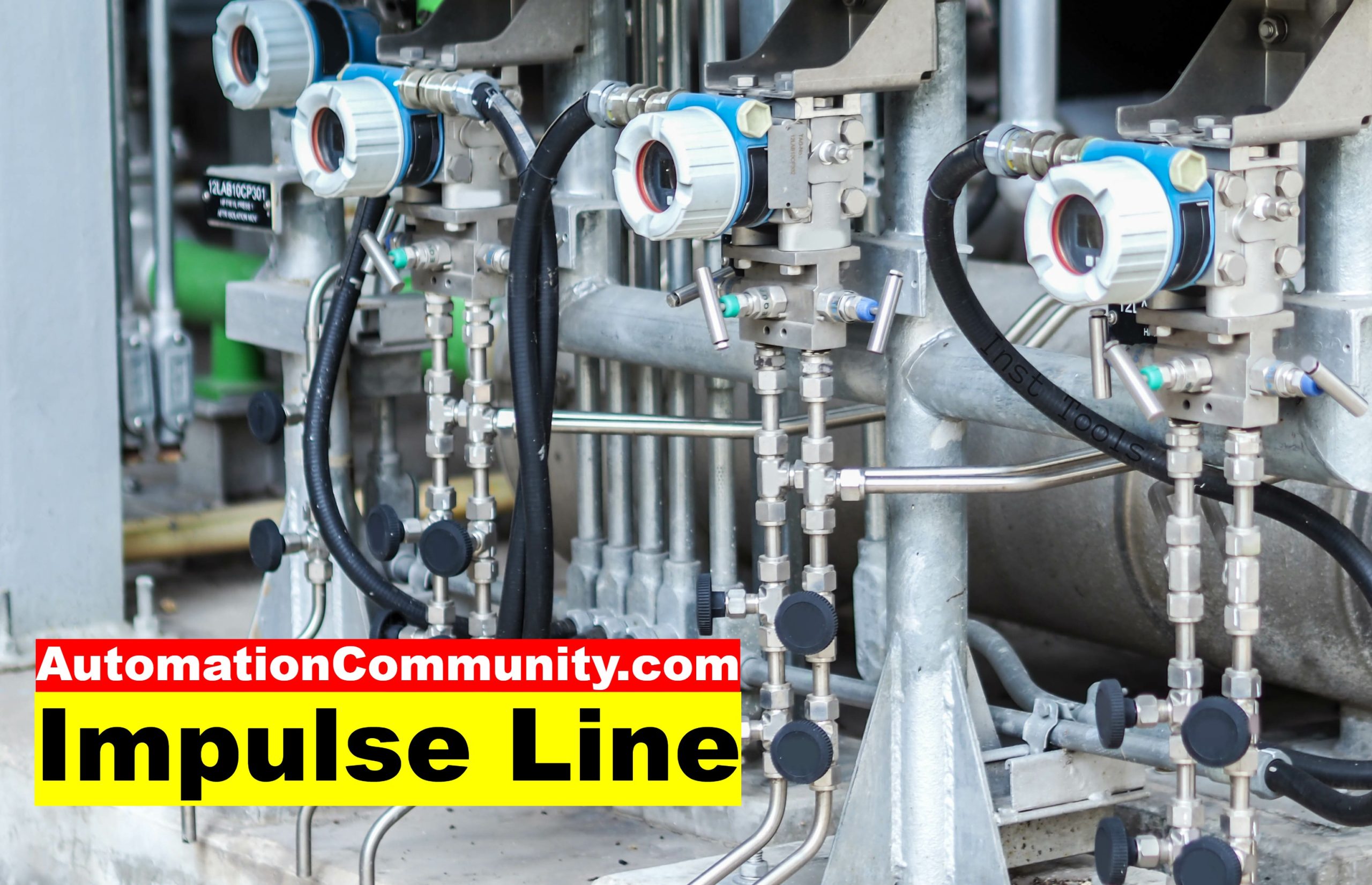
The primary purpose of instrument impulse lines is to protect the instrument from the adverse effects of the process fluid. They act as a barrier, preventing the fluid from directly contacting the instrument while allowing pressure to be transmitted accurately. This separation ensures the instrument’s longevity and reliability, even in demanding industrial settings.
What are impulse lines in instrumentation?
Impulse lines are small-bore pipes used to transmit the pressure signal from the process to the pressure sensor in a process control system. They help maintain accuracy and safety.
What is the purpose of filling impulse lines with liquid?
Filling impulse lines with liquid is done to prevent freezing in low-temperature conditions, and to prevent the process fluid from directly reaching the instrument when the process fluid is corrosive or viscous.
What are the considerations for installing impulse lines?
Some key considerations include avoiding high points where gas can be trapped in liquid service, and avoiding low points where liquid can be trapped in gas or steam service. They should also be arranged to minimize mechanical stress.
How can you avoid gas pockets in liquid service impulse lines?
You can avoid gas pockets by installing the impulse lines in a continuous uphill gradient towards the instrument.
What problems might occur if impulse lines are installed improperly?
Improper installation could lead to measurement errors due to gas or liquid pockets, hydrostatic pressure differences, or unequal heat transfer. It may also increase the risk of blockages or damage.
What is the difference between wet and dry leg in impulse lines?
A wet leg is a reference leg filled with liquid for use with a differential pressure transmitter measuring the level in a pressurized tank. A dry leg is an impulse line that’s empty or filled with gas.
How can impulse lines be arranged for a differential pressure transmitter?
Impulse lines can be arranged in a three-valve or five-valve manifold configuration, allowing for safe calibration and maintenance without disrupting the process.
What might be some potential issues of impulse lines with steam applications?
In steam applications, condensed steam can accumulate in the impulse lines and affect the pressure readings.
How do you ensure impulse lines remain clear in slurry applications?
In slurry applications, the impulse line should be installed at an angle to allow gravity to return the slurry to the process.
Can you explain how an equalizing valve works in relation to impulse lines?
An equalizing valve allows pressure to be balanced between the high and low-pressure sides of a differential pressure transmitter. It helps to calibrate the instrument and to safely isolate it from the process.
What is the purpose of a manifold in impulse line configuration?
A manifold allows for the isolation of the instrument from the process, safe venting of the process fluid, and equalization of pressure for calibration.
Why do we sometimes fill impulse lines with a sealing liquid?
This is done in applications where the process fluid may freeze or solidify. The sealing liquid creates a barrier that protects the instrument from these process fluids.
What are the potential dangers of impulse lines freezing and how can they be avoided?
Freezing can cause the impulse lines to block, resulting in inaccurate readings. It can be prevented by using trace heating and insulation.
Why is it important to drain impulse lines regularly?
Draining is important to remove any condensed fluid or accumulated particles that could affect the accuracy of the measurements.
Why do some systems use two impulse lines in a differential pressure transmitter setup?
Two impulse lines allow the transmitter to measure the difference in pressure between two points in the process, which is important for flow and level measurements.
How can air pockets affect the readings of impulse lines?
Air pockets can cause inaccurate readings because they affect pressure transmission. They should be avoided by proper installation and regular maintenance.
Can you explain the role of purging in impulse line maintenance?
Purging helps clear blockages in the impulse lines, ensuring the accurate and consistent transmission of process pressure to the instrument.
How does impulse piping configuration differ for liquid, gas, and steam services?
For liquid services, impulse lines should be sloped downwards towards the process; for gas services, they should be sloped upwards towards the instrument; for steam, a condensate leg should be used to prevent direct contact of steam with the instrument.
What are the best practices for impulse line installation?
These include choosing the right materials, considering process conditions, minimizing the length and number of bends, and maintaining proper slope and insulation.
How do you diagnose impulse line problems?
Common methods include visual inspections for leaks or damage, pressure testing to check for blockages, and checking for measurement discrepancies that could indicate issues with the impulse line.
Why is it important to have a vent in an impulse line?
A vent allows trapped air or gases to be released from the impulse line, ensuring accurate pressure transmission.
What materials are typically used for impulse lines and why?
Common materials include stainless steel and carbon steel due to their strength, durability, and resistance to corrosion and temperature fluctuations.
What is the purpose of a condensate pot in an impulse line system?
A condensate pot is used in steam applications to collect and remove condensate, preventing it from entering the impulse line and affecting the readings.
What does the term “hydrostatic head” mean in relation to impulse lines?
Hydrostatic head refers to the pressure exerted by a fluid due to its height in the impulse line. This pressure can affect the instrument’s reading.
Why might it be necessary to heat trace an impulse line?
Heat tracing is used to maintain the temperature of the process fluid in the impulse line above its freezing point or below its boiling point.
What factors would you consider when choosing the diameter of an impulse line?
Factors to consider include the type and viscosity of the process fluid, the process conditions, the desired response time, and the risk of blockages.
How does a closed-loop impulse line system work?
In a closed-loop system, the process fluid in the impulse line is continuously circulated back to the process. This helps to maintain accuracy and prevent blockages.
Why are elbows and bends minimized in impulse line design?
Elbows and bends can cause pressure drops and increase the risk of blockages. They also make the line more difficult to clean and maintain.
How would you handle a leaking impulse line?
The line should be isolated and repaired or replaced as soon as possible. If it cannot be immediately repaired, the instrument should be taken out of service to prevent inaccurate readings.
What is the purpose of a syphon in an impulse line system?
A syphon provides a barrier between the process fluid and the instrument, protecting the instrument from high-temperature steam and preventing direct contact with corrosive or dirty fluids.
Can you describe the potential impact of impulse line length on measurement accuracy?
Longer impulse lines can result in greater pressure drops and slower response times, reducing measurement accuracy. The line length should be minimized wherever possible.
Why are quick-connect fittings sometimes used in impulse lines?
Quick-connect fittings allow for easy installation and removal of the impulse line for maintenance or replacement. They also reduce the risk of leaks compared to threaded connections.
How do you ensure the impulse line is properly aligned with the process and instrument connections?
Proper alignment is ensured through careful measurement and fitting during installation. Misalignment can cause stress on the line and lead to leaks or damage.
Why is stress analysis sometimes performed on impulse lines?
Stress analysis can identify potential issues with vibration, thermal expansion, or pressure-induced stress that could lead to the failure of the impulse line.
Can you explain the concept of a “wet leg” in impulse line configurations?
A wet leg refers to an impulse line filled with a liquid (usually water or a similar sealing liquid) to prevent the process fluid from contacting the instrument. This is typically used in applications with high-temperature or corrosive process fluids.
What measures would you take to prevent impulse line vibration?
Vibration can be minimized by securing the impulse line with supports and by avoiding resonance with the process vibrations. Pulsation dampeners can also be used in some cases.
How do you calculate the pressure drop in an impulse line?
The pressure drop can be calculated using fluid dynamics principles, considering factors like the length and diameter of the line, the flow rate, and the viscosity of the process fluid.
Why might an impulse line need to be insulated?
Insulation helps maintain the temperature of the process fluid in the line, preventing issues like freezing or condensation that can affect the accuracy of the readings.
What are some safety considerations when working with impulse lines?
Safety considerations include isolation of the line from the process during maintenance, proper venting of trapped pressure, and appropriate handling of the process fluid to avoid exposure to harmful substances.
How does a double block and bleed configuration work in impulse lines?
In a double block and bleed configuration, two isolation valves allow the instrument to be safely removed from service while a bleed valve allows trapped pressure to be safely vented.
Can you explain how a pressure snubber might be used with an impulse line?
A pressure snubber can be used to dampen pressure surges in the impulse line, protecting the instrument from damage and ensuring steady readings.
Why is it important to check the impulse line for leaks?
Leaks can cause inaccurate readings and potentially expose personnel to harmful process fluids. Regular leak checks are an important part of impulse line maintenance.
How can process fluid contamination be prevented in impulse lines?
Contamination can be prevented through the use of appropriate materials and sealing liquids, regular cleaning and purging of the line, and proper design to avoid the accumulation of particles.
How can you mitigate the impact of temperature changes on impulse line readings?
Temperature impacts can be mitigated by insulating the impulse line, using heat tracing where appropriate, and compensating for temperature effects in the instrument calibration.
What are some common issues that can arise with impulse lines and how can they be detected?
Common issues include blockages, leaks, vibration damage, and temperature effects. These can be detected through visual inspection, pressure testing, vibration analysis, and monitoring of the instrument readings for discrepancies.
Read Next: