Modbus Communication between Mitsubishi HMI and Delta VFD
Modbus communication between Mitsubishi HMI (GS series) and Delta VFD (VFD-L)
In this topic, an Induction motor is controlled by delta VFD through Mitsubishi HMI.
There is no PLC used in this application.
The speed of the motor is controlled by feeding the values in the Numeric inputs placed on the HMI screen as directed by the Instruction manual of the VFD just to show the communication of HMI and VFD.
Here, the Induction motor is not controlled by the external terminals (Digital or Analog Inputs) of the VFD, rather we will use the RS485 port for running, stopping, and speed varying.
Different VFDs require different sorts of values for the specific Modbus Addresses to start, stop and vary the speed when the RS485 protocol is used. We are here to use those values only, to execute the said process.
For the implementation,
a) VFD and HMI should be correctly connected through the communication cable
b) VFD needs to be properly parameterized with the communication settings such as Baud rate, Parity bits, Device Address, etc.
c) HMI configuration should be done according to the communication parameters set in VFD
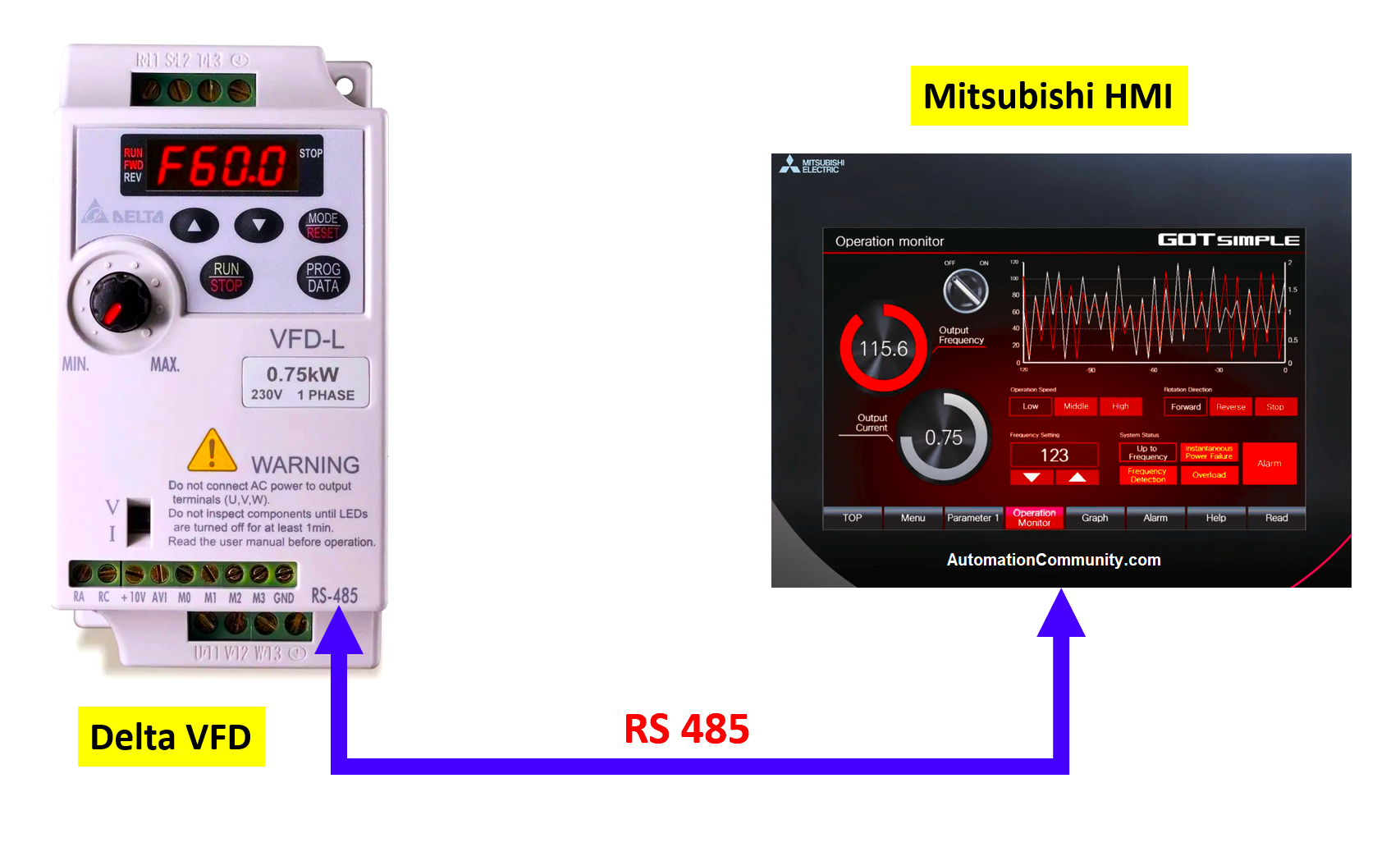
Cable Connection details of HMI and VFD on RS485 protocol are shown below.
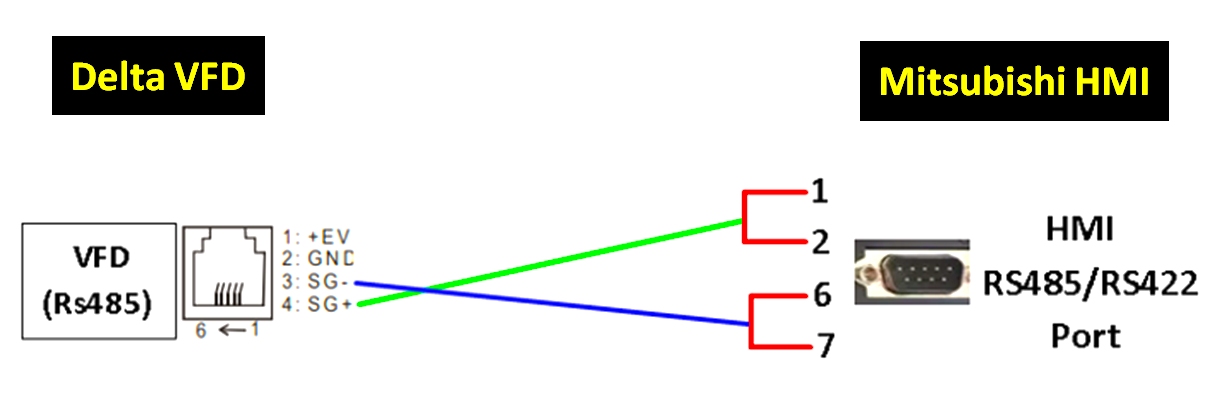
The mode of Communication is defined in the Group 2 parameter section of the VFD.
Set both 2-00 and 2-01 as “4”
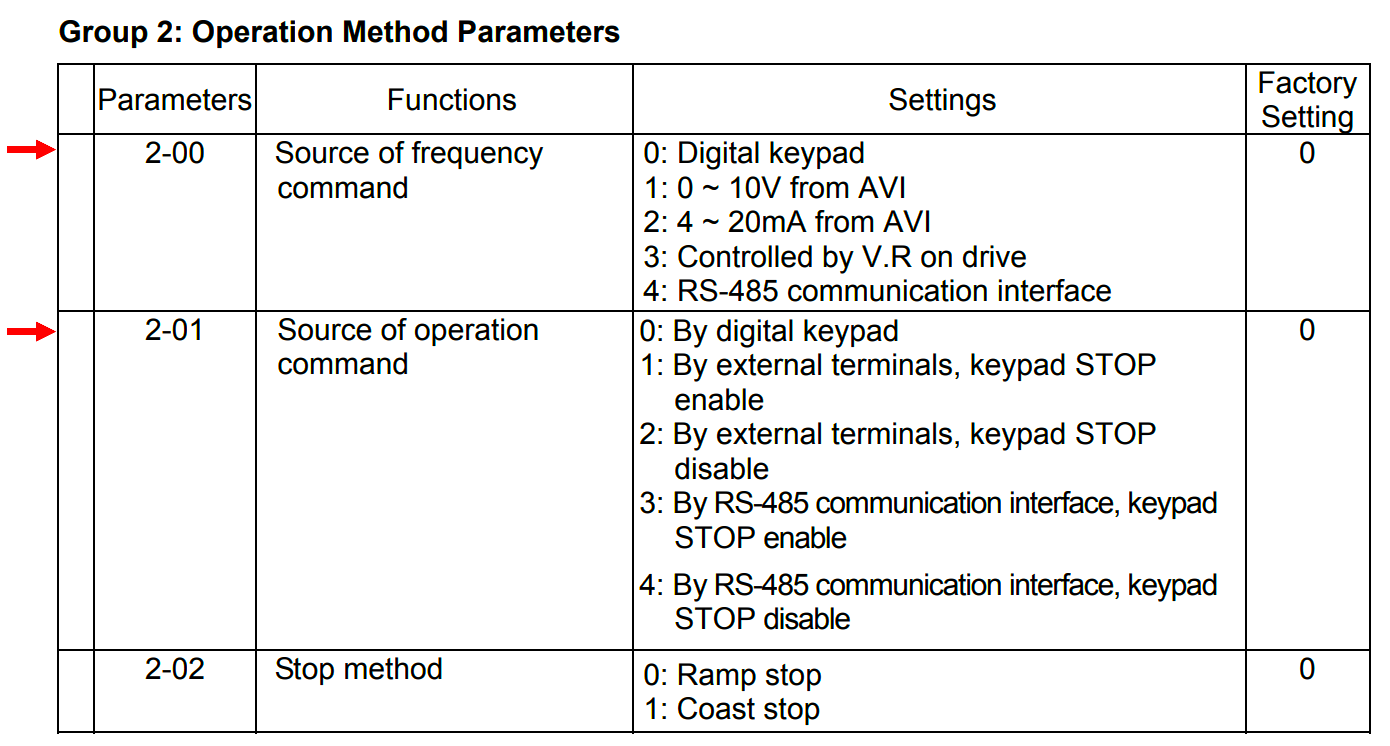
Communication settings are done in the Group 9 parameter section of the VFD.
The station address (Slave ID) of any device is used to identify each device in a system. All the other parameters need to be matched at each station.
Define the Slave ID as “2” in the parameter 9-00 and set 9-01 (Baud rate) to “2”
Set 9-04 to “6” (RTU mode, parity None and Stop bits equal to 2)
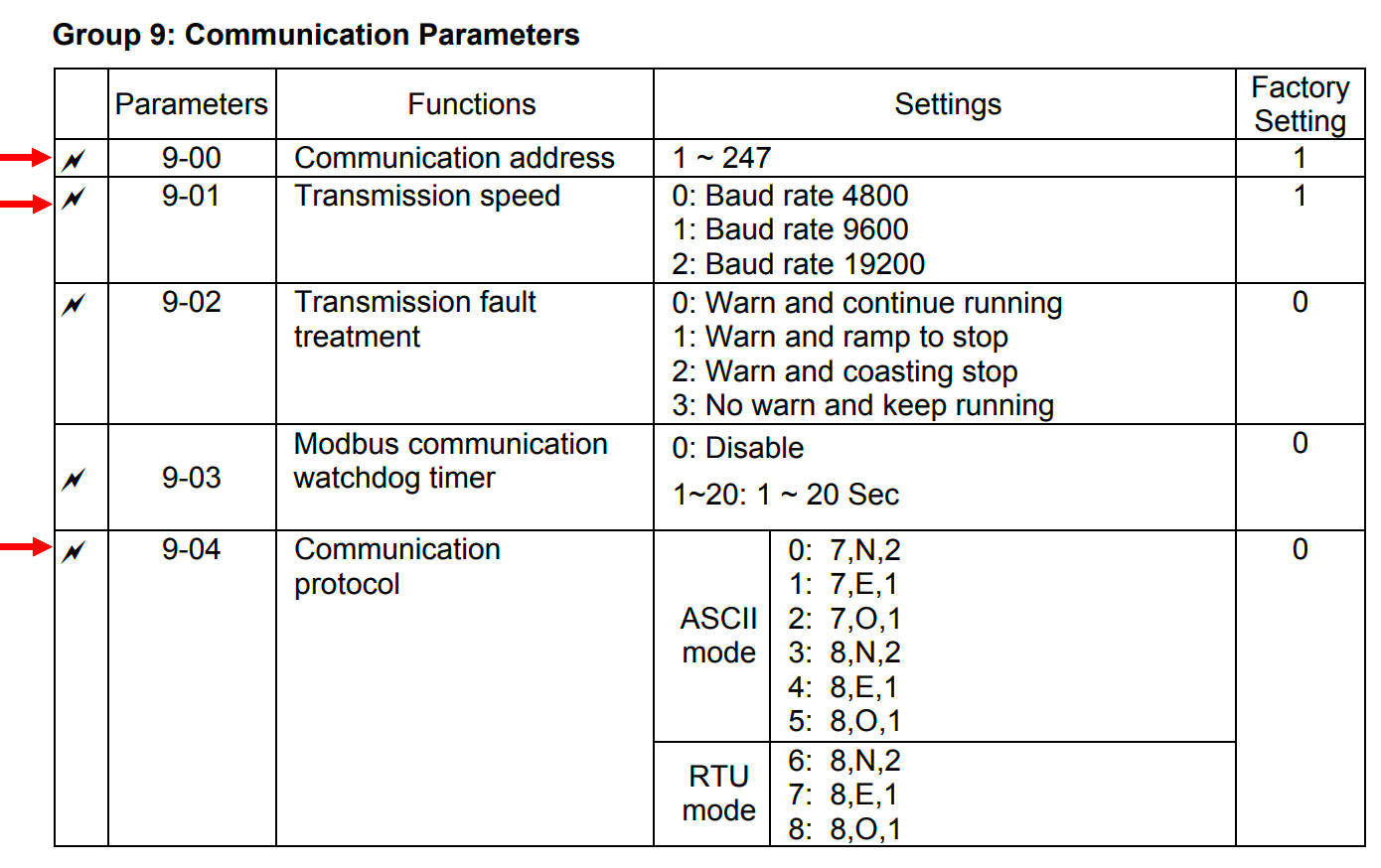
After selecting “New” in the “Project” Section, choose the series as “GS”. In GOT Type setting, choose the model as “GS2107-WTBD-N”. Then Click “Next”.
After confirming the above settings on the next page, select “Modbus” as Manufacturer and define HMI as “Modbus Master” in Controller type. Then Click “Next”.
Click Next after selecting the Interface as RS422/RS485
In Communication Driver’s “Detail setting” window, settings should be made according to the set parameters in VFD.
Define the Host address (Station address) differently from the VFD one. Here, 1 is defined which is different from 2. Ensure that Function codes 0F and 10F are selected as “Unused”.
After confirming the above settings, leave the screen switching settings as the default one and press “Next”.
Select a screen design on the previous page and Click Finish on confirming all the settings
Before moving further, one should know the Modbus addresses of VFD using which the operation and frequency is controlled.
2000H is the address for operational command where 2001H is for frequency control where “H” denotes Hexadecimal.
As per VFD’s instruction manual, when 2000H holds 10 (Dec), the motor will run and when it holds 1 (Dec), the motor will stop.
Also, when 2001H holds 5000(dec), the motor would run at 50Hz
The format in which the Mitsubishi HMI accepts the Modbus address is shown below.
Similarly, 2000H is accepted as 408193 and 2001H as 408194 when delta VFD-L is used.
Place a “Numeric Input” Element from the Object section, highlighted at the top.
Expand and double-click it to tag the address.
In the device addressing setting, 4 represents the Holding Register, and 8193 is addressed with 2 as the Station Address of VFD. Take the format as Signed Decimal (Highlighted). Then Click Ok.
This Numeric input is reserved for Operation control.
Take a similar input with the device address as “8194” for Frequency control.
The final screen may look as below.
Feeding 10 (Dec) in Operation CTRL numeric input would run the motor and 1 (Dec) would stop it.
5000(dec) is required to be fed in FRQ CTRL numeric input to attain the frequency of 50Hz. Change the value accordingly, to vary the speed.
Conclusion: An Induction motor is controlled from the Mitsubishi HMI using delta drive on RS485 protocol.
Comments
3
Can we connect multiple VFD’s to the same HMI using a Switch or HUB.?
Can we connect and control multiple VFD’s to single HMI ?
yes